
Hengyi (Brunei) PMB Petrochemical Project Base under construction. (Li Junwei)
Two years ago, the area was deserted and deserted; two years later, an international large-scale petrochemical base with crude oil processing capacity of 8 million tons per year was built. This is the Hengyi (Brunei) PMB Petrochemical Project Base on Damora Island, Brunei. Two years later, China's chemical engineering two was built on this deserted island, with the amazing &ldquo of the world, the speed of China &rdquo, and the completion of the &ldquo with high standards; &rdquo along the way; and the construction task of the international large-scale petrochemical project. What kind of courage and courage did the founder of China Chemical Industry write such a legend? A reporter from China Chemical Daily went to the project site recently to explore it.
Build “ along the way ” bright card.
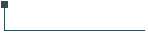
Reporters learned that this time, Sinochem II undertook the second and fourth bidding stages of the first phase of Hengyi (Brunei) PMB petrochemical project, including 30 units of hydrogenation unit, coking unit, public works and ancillary facilities, auxiliary production facilities, oil storage and transportation, wharf facilities, with a total planned investment of 3.45 billion US dollars. Bi Jiawei, deputy general manager and project manager of the two chemical and Chemical Engineering Department of China, said that this is the largest project in China now in &ldquo and &rdquo along the way. It is also the largest contract petrochemical project in the history of Sinochem two chemical construction.
Bi Jiawei said that the first phase of the project designed a crude oil processing capacity of 8 million tons per year. The main production facilities include six individual projects, such as refining, chemical production, oil storage and transportation. China Chemical Engineering Diversification has built 1.3 million tons/year kerosene hydrogenation unit, 2.2 million tons/year diesel oil hydrogenation unit, 2.2 million tons/year hydrocracking unit and 1 million tons/year flexible coking unit of this project, and has completed the operation of 2.23 billion yuan. At present, all the facilities under construction of chemical engineering in China have been smoothly transferred to China, and will gradually enter the stage of production and transportation.
& At one time I wanted to give up. & rdquo; & ldquo; I don't want to do it, but I have to do it. & rdquo; This is the voice of many employees who have fought on the project site. It is conceivable that there are many difficulties to accomplish this arduous task. Bi Jiaweilian used 11 & ldquo; unprecedented & rdquo; to express the difficulty of the project implementation, the test faced by enterprises and the significance of the project implementation. Bi Jiawei admitted that during the peak period of project implementation, the number of construction workers reached 4500. Among them, there are 3300 Chinese employees and nearly 1200 foreign workers. In order to complete the task according to the time node, they grasp the progress and quality, and carry out high-load operation day and night. Finally, in just two years, &ldquo was created; &rdquo was built in China, and the bright card was shining on &ldquo and &rdquo.

Sinochem Second Construction Holds the Initiation and Mobilization Conference of Hengyi (Brunei) PMB Petrochemical Project
Build the First Flexible Coking Unit
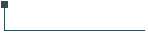
As part of the project, & ldquo; the highlight of the project, & rdquo; and the flexible coking unit was officially handed over to China on July 10. Bi Jiawei introduced that the device is the first set of domestic and seventh sets of flexible coking units built by the Chinese enterprises in &ldquo and &rdquo along the belt. The device can gasify the raw materials containing up to 95% coke, and the gasifier provides the heat needed in the reaction process, and produces low calorific value gas which can be used as fuel. The remaining coke accounts for only 1% of the feed, so as to realize the full utilization of raw materials, such as ldquo, rdquo and resources.
& The flexible coking unit has compact design, narrow road and more large equipment. To this end, the project department carefully organized and rationally planned, all tower equipment to carry out ‘ wear clothes and hats ’ construction, all to achieve the goal of lighting the tower. In addition, the flexible coking pipeline has many kinds of materials and is difficult to construct. During the construction process, the emphasis is placed on controlling the welding quality of the alloy pipeline, and 100% of the high alloy pipelines in the installation area are tested nondestructively. All 804 pressure test packages of flexible coking unit were completed on June 8 and successfully handed over to China on July 10. & rdquo; flexible coking sub-project manager Yan Junfeng told reporters.
& Compared with conventional delayed coking tower technology, flexible coking has stronger adaptability to raw materials and wider range of processable raw materials. & According to Yan Junfeng, the device is designed with Exxon Mobile technology, which avoids the periodic fluctuation and operation risk caused by delayed coking cycle switching and reduces the labor intensity of coke removal work; the coke generated is used to convert into flexible gas to solve the problem of low-value coke's direction; and the high temperature source can be avoided. Coking and clogging of the furnace tube occurred before the feed entered the reactor.
Completing Construction Task with High Efficiency and Quality
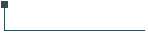
In order to accomplish the construction task efficiently and with high quality, the project department has carried out the following measures: ldquo; 100-day-long work & rdquo; activity, process pipeline & ldquo; 60-day work-long work & rdquo; Baozhong Jiao & ldquo; 60-day work-long work-rdquo; activities, and also implemented the steel structure joint reward, pipeline welding reward policy, pipeline pressure test reward and other measures to encourage employees to rush time. To catch up with the schedule and strive to complete the construction task according to the time node. In the past two years, the Brunei Project Department of Sinochem Second Construction has successfully built 12 prototype projects, such as installation and construction of hydrotreating static equipment and thermal insulation construction of fractionator of diesel hydrotreating unit, which have been fully recognized by the owners.
Zhao Jun, Project Manager of Electrical Instrument Branch of Brunei Project Department, said: & ldquo;On-site construction period requirements are tight, hot weather, frequent thunderstorms, late drawings to the factory, delayed supply of electrical equipment and materials, on-site deep cross-operation, more closed space operations, large mobility of personnel, large amount of engineering, especially flexible coking unit, which is the first set contracted by domestic enterprises, this is for on-site construction organization and safety management. High requirements have been put forward in quality management and other aspects. During the construction period, we made a deep prediction of the technological progress of each installation area, effectively solved the construction problems, avoided the blowout construction situation of instrument specialty in the later stage of construction, greatly shortened the limited construction period, and was highly affirmed by the owners many times. & rdquo;
Zhao Jun told reporters that the project officially started on July 21, 2017, Qidong Prefabrication Plant officially started on August 21, 2017, prefabricated steel structure, pipe support and pipeline equipment. Thereafter, the hydrocracking reactor of Brunei PMB single heaviest equipment was successfully hoisted in one time, the whole field process and the pressure test of thermodynamic pipeline network were started, the pressure test of flexible coking unit area was completed, and the first compressor test run in the whole field was successful-hellip; & hellip; in June and July this year, the hydrorefining, hydrocracking and flexible coking of the project were three main units. The relay of diplomatic relations marks that Hengyi (Brunei) PMB petrochemical engineering has formally entered the production stage.
Up to now, the project department has completed 100,000 cubic meters of concrete pouring, 31,000 meters of underground pipeline network installation, 22,000 tons of steel structure installation, 925 sets of main equipment installation, 1.08 million cubic meters of process pipeline welding, 912 sets of electrical cabinet and instrument cabinet installation, and 49,000 sets of bridge installation. 3.1 million meters of cable laying, 8125 sets of lamps and lanterns, and 14,000 sets of various electrical equipment have been completed. The qualified rate of quality control points is 100%, the qualified rate of radiographic inspection of weld seam is 98.5%(number of sheets), and there are no quality accidents in the whole year.
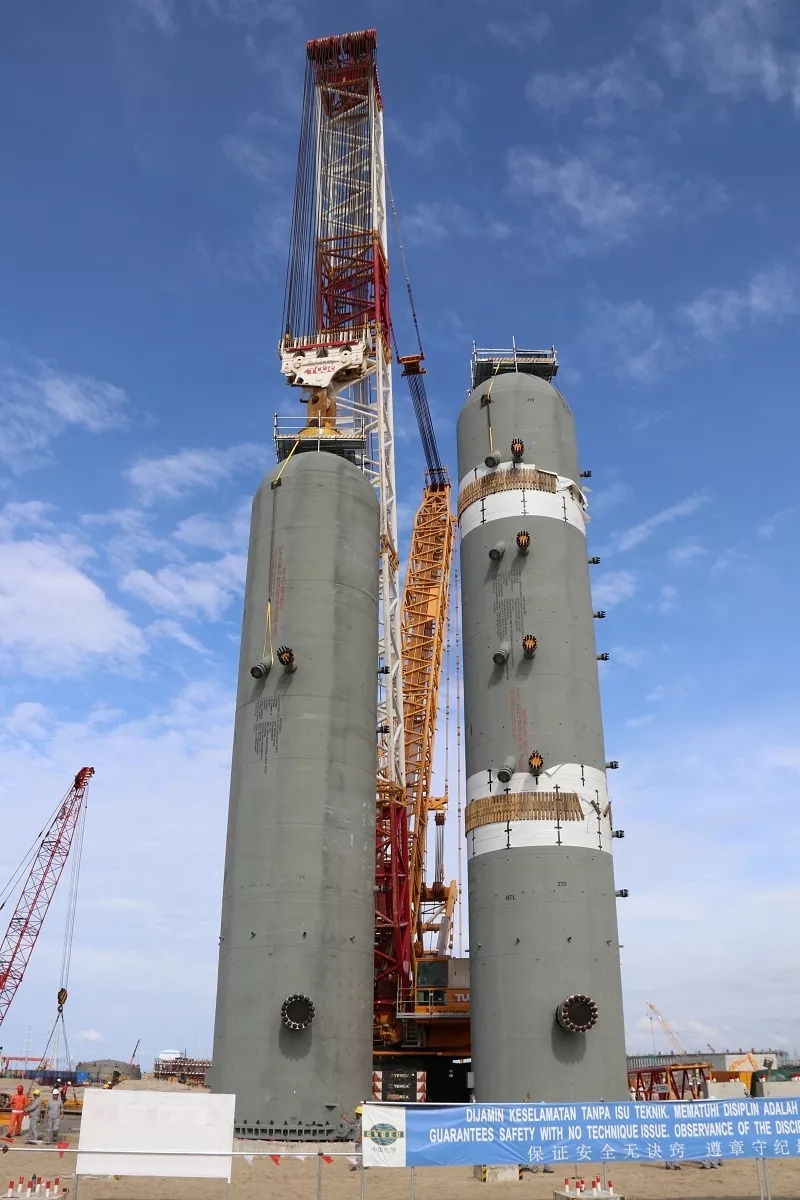
The hydrocracking reactor and Hydrofining Reactor of the second Sinochem Hengyi (Brunei) PMB petrochemical project were successfully hoisted once. (Photographed by Wen Jidong)
Safety Management Full Coverage
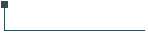
Reporters in the installation site to see, large and small signs, warning signs, safety banners can be seen everywhere, installation site roadway cables neat, clean and tidy. Li Qingzhong, General Secretary of the Party Branch of the Second Chemical Engineering Construction Brunei Project Department of China, told reporters that in order to achieve full coverage of safety factors in the plant area without dead corners and blind areas, and to ensure the safety of employees in construction, the project department has set up an independent safety management organization, which allocates safety management personnel according to the number of 50:1 on-site personnel, and adopts a zone. Responsibility system, supervision time and construction synchronization, weekly safety weekly meetings, summary and analysis. For different types of personnel, organize corresponding special safety training, implement & ldquo; three handover and one clearance & rdquo; and supervise the implementation of district security officers.
In addition, according to the local laws and regulations of Brunei and the requirements of HSE management system documents of the company and the owner, and combined with the actual management system of the project, the project department has formulated various safety management regulations and safety production responsibility system for all staff members; each safety management personnel carries out self-inspection and supervision every day according to the area division, and eliminates hidden information in time on the spot. Hazards; Weekly safety and civilized construction inspection, comprehensive investigation of hidden dangers on the site; according to the progress of construction, special safety inspection is organized irregularly. The project department has also worked out the comprehensive emergency rescue plan and the special disposal plan on the spot, established the emergency rescue organization, set up the medical room, equipped with the first aid medicine box on the spot of each device, and organized regular emergency drills such as fire fighting and restricted space.
In terms of safety management, the project department strictly carries out the management policy of safety first, prevention first and comprehensive management. Since the start of the project, no safety accidents have occurred above minor injuries. The quality control of the project is strictly carried out in accordance with the owner's quality procedure documents and the company's quality management regulations. Self-inspection and mutual inspection complement each other, special inspection and joint inspection. Combination; combination of pre-prevention and in-process control; construction quality in a completely controllable state, to truly achieve the full coverage of safety factors in the factory area, fully ensuring the safety of employees in the construction process.