[introduction] in various industrial fields, such as widely used mechanical seal seal device. However, there are many limitations in the practical application of the device. To design and produce excellent mechanical seal products, it is necessary to carry out professional analysis and calculation of the relevant parts, to solve the problems to improve the use of results. Chemical machinery is in the process of chemical production, processing in order to meet the specifications of products, a series of professional chemical machinery used in each processing link, the reliability of chemical mechanical seal is becoming more and more important. Therefore, it is necessary to analyze the common seal failure and the cause of the chemical machinery, and find out the method to solve the seal failure.
First, the concept of mechanical seals
1, the origin and structure of mechanical seals
The mechanical seal is also called the seal, or “ mechanical seal ”, is a rotating device for pump, hydraulic transmission and related equipment of high-tech products, sealing. With the progress of science and technology, new materials and new processing technology of seal mechanical seal progress and emerge in an endless stream, considerable development has been made in the theory of seal and other related aspects, mainly for the sealing theory: including sealing friction and lubrication, sealing principle, sealing dynamics and hydrodynamic lubrication theory. Seal structure: there are two main face seals and multi end seals, single spring and multi spring, floating, contact and other related structures. The mechanical seal system includes a movable ring and the static ring; the sealing ring; the spring and thrust ring; bomb Kei seat and a key or a fixed screw.
2, the composition of mechanical seals
There are many kinds of standards for the composition of mechanical seals. The spring element is divided into a rotating type and a stationary type. Each has its advantages and disadvantages. Strong corrosion is the main deficiency of the rotating type, while the static type does not exist. Because this kind of medium is the main part of the mechanical seal, it directly affects the quality of the seal. Therefore, in the processing process, the sealing of the various indicators have strict requirements. To seal the direction of leakage of media to divide, including the internal flow and the outflow type. Balanced and non balanced by media. According to a spring to distinguish single spring or spring type and many other forms of division.
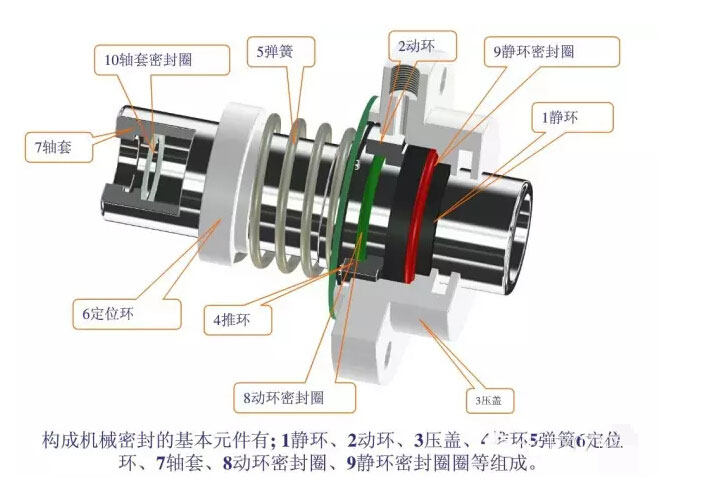
Mechanical seal structure
Principle of mechanical seal

Mechanical seal principle of pump
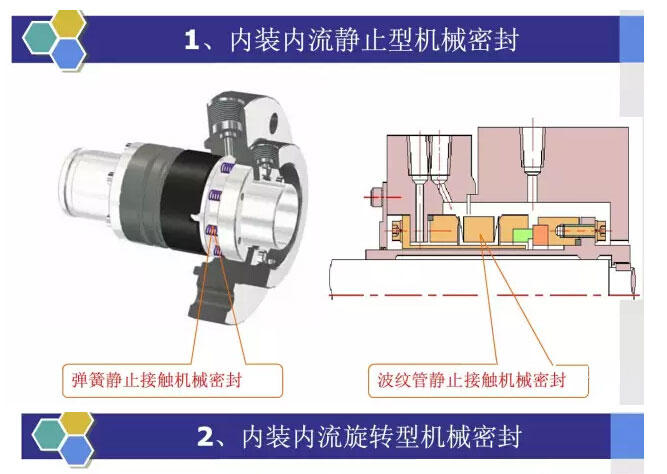
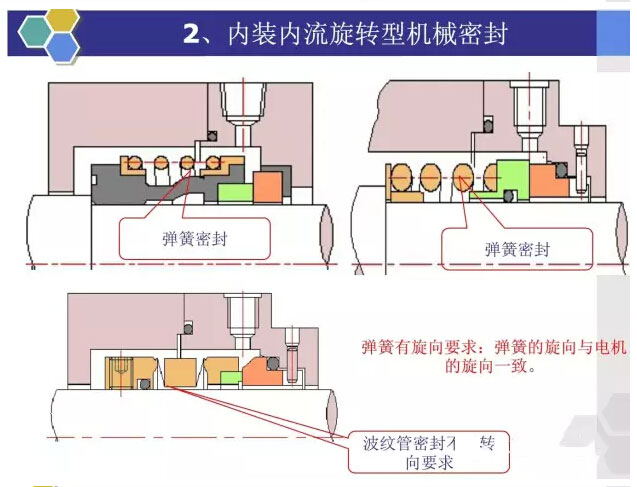
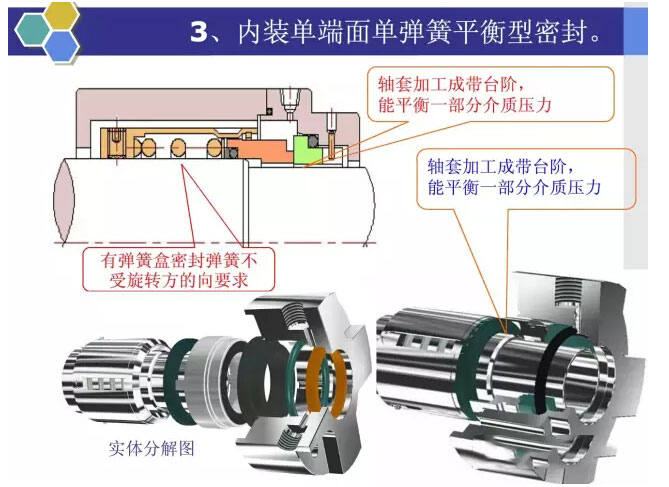
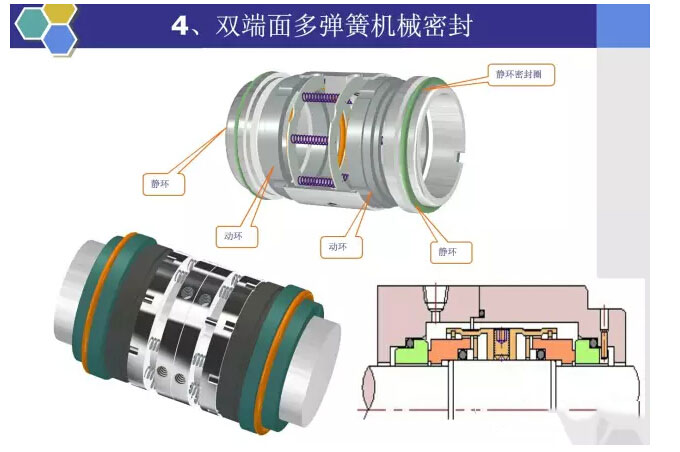
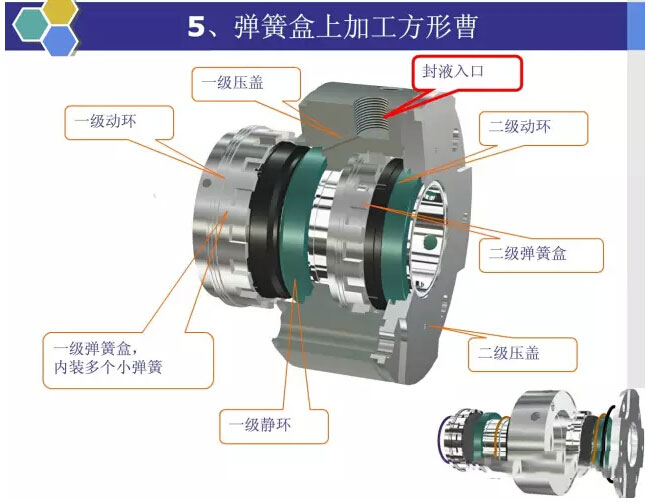
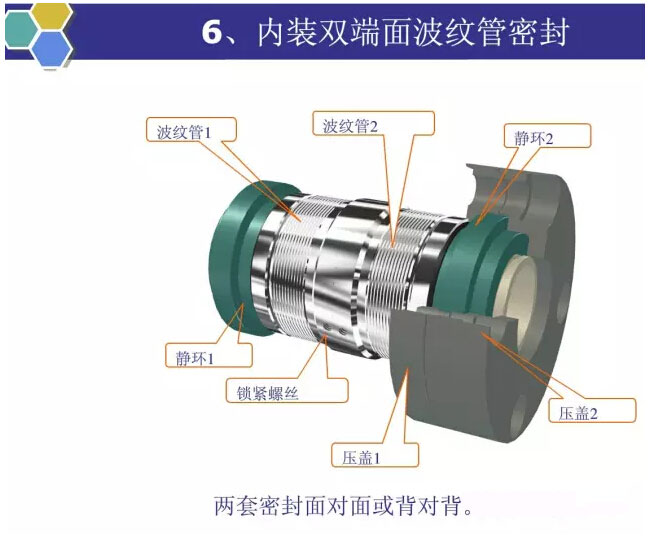
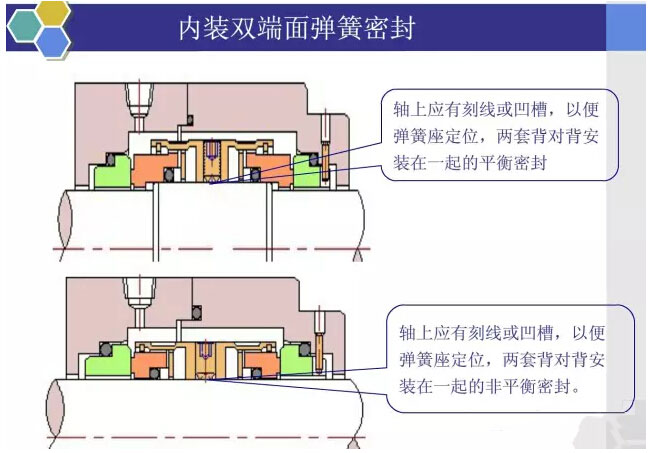
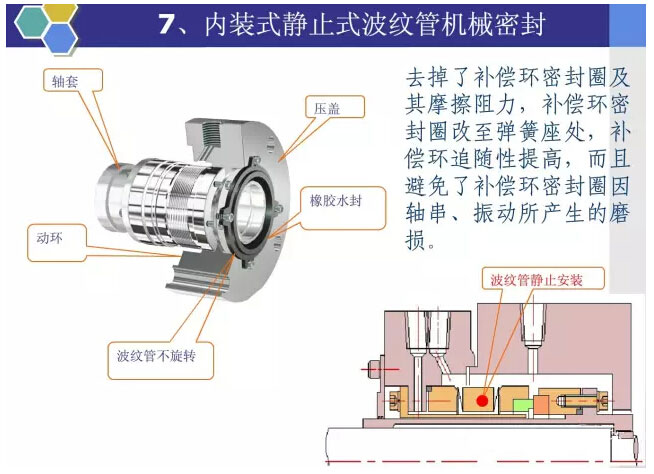
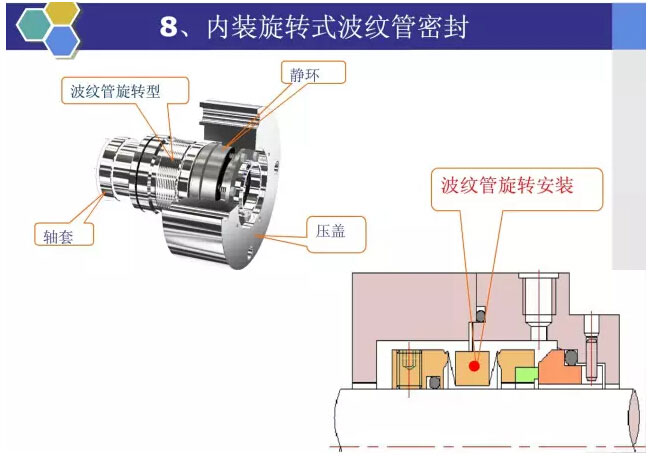

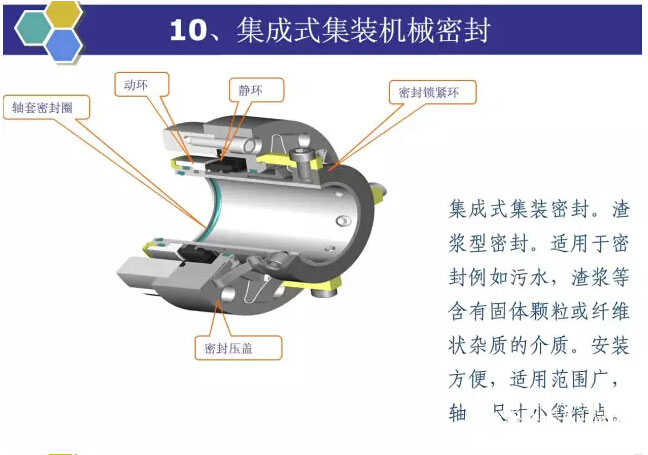

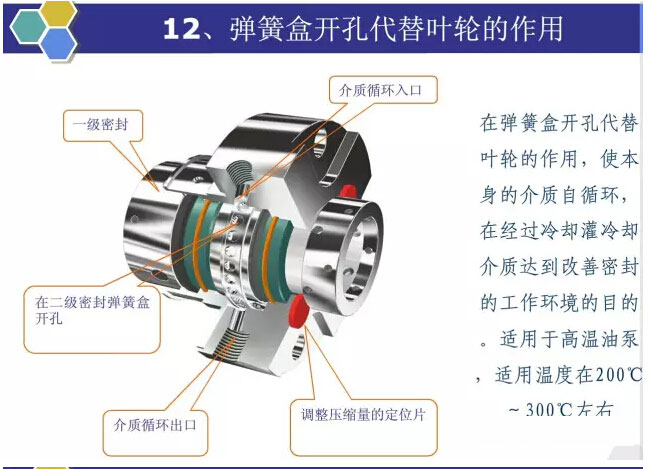
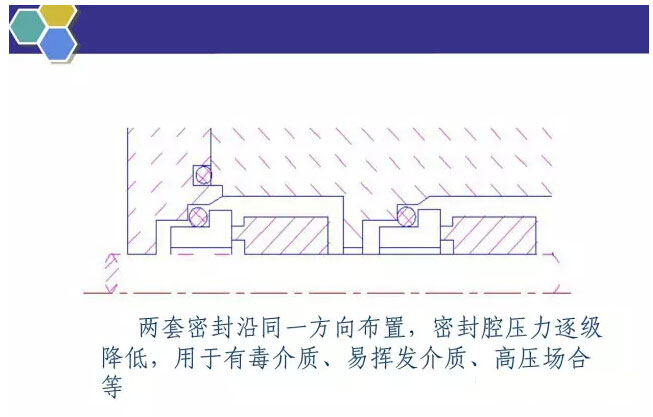
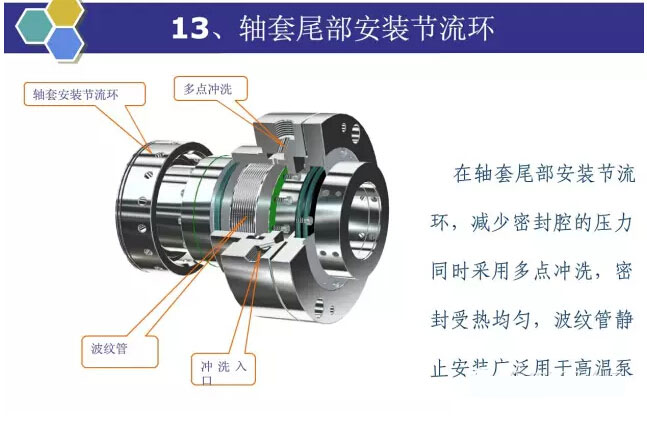

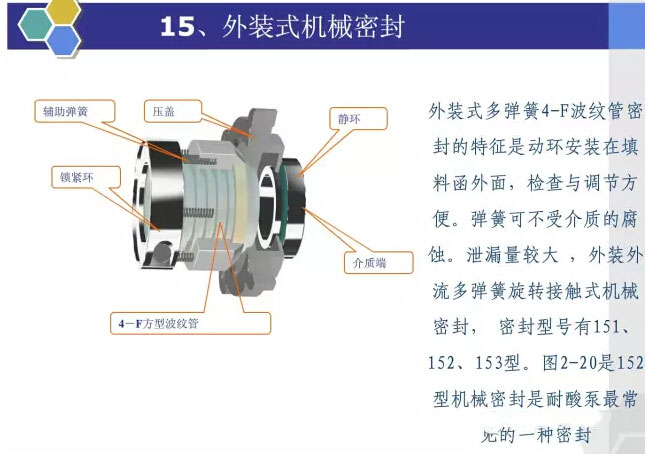
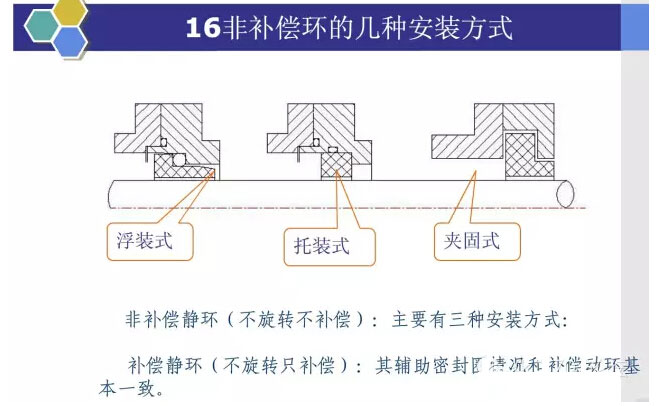

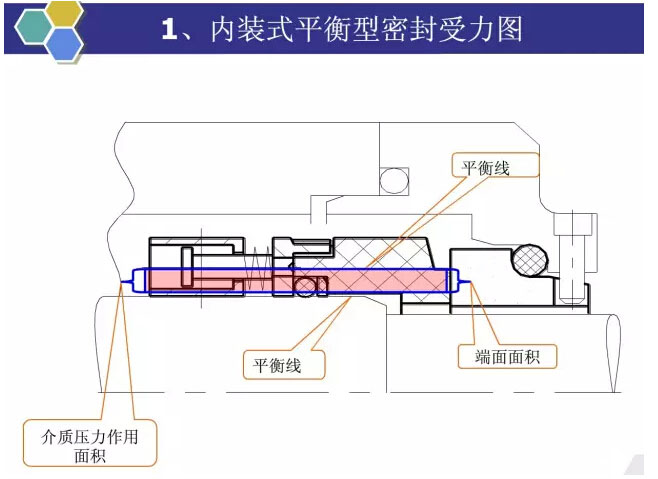
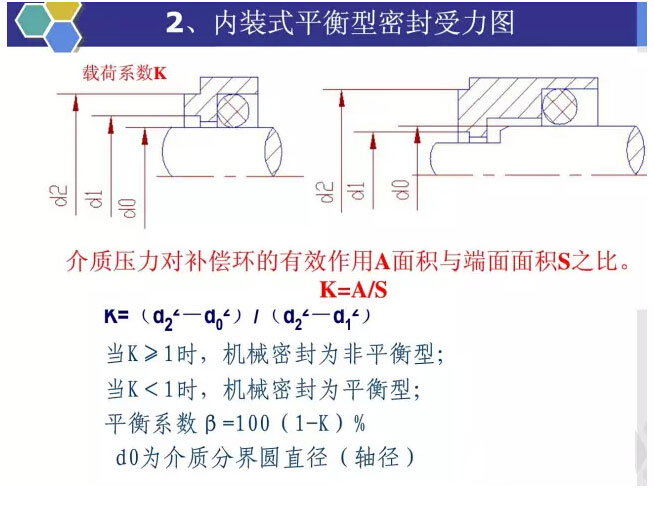
Mechanical seal physical map
Mechanical seal physical map
Two, the cause of chemical mechanical seal failure
Mechanical seal leakage
Mechanical seals mainly in the inside, it requires a very professional and deep working experience, as well as accurate measurement equipment to accurately determine the cause of the leak. First of all, it is necessary to understand the impact of the damaged parts on the sealing effect of the degree, and then gradually to the transmission parts and other parts of the investigation, to grasp the situation of damage. Other relevant systems should be tested.
1, operating errors caused by mechanical seal leakage
During the operation, due to various anomalies caused by dynamic and static ring contact failure; the installation amount of compression control errors, resulting in a large area of wear and abrasion; choose the type design properly, resulting in seal face pressure and cold compress data error is too large; or in the mechanical operation process of debris into the equipment, resulting in mechanical damage etc..
2, overheating damage to seal leakage
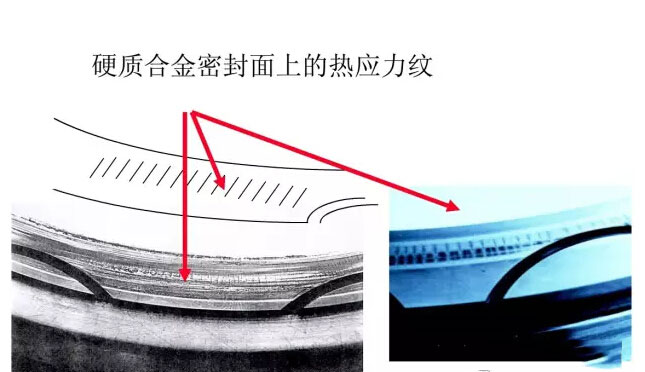
Mechanical overheating will not only wear the sealing surface, will lead to hot cracking or blistering. Thermal cracking is caused by the large thermal stress of the surface of the seal ring to produce radial cracks, it will appear in a short time under the mechanical load. In order to prevent such failures, it is necessary to design a reference to the performance and operating conditions of the raw materials to do the optimization design. Like overload, high speed, improper material and other factors will produce hot crack, resulting in leakage.
3, long-term mechanical wear lead to seal leakage
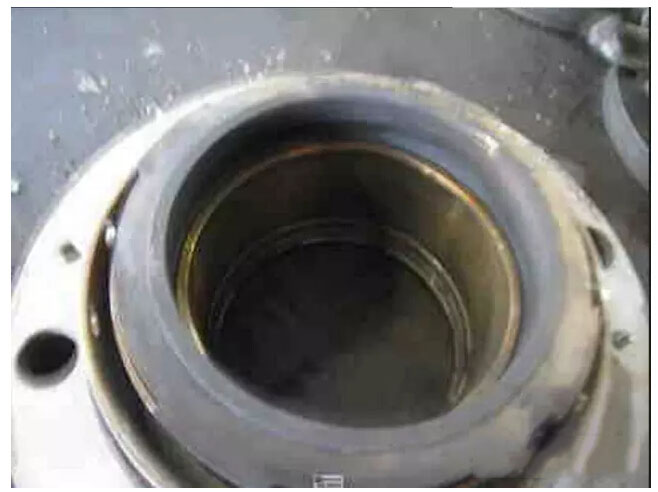
When the normal operation procedure of the seal pair is destroyed by the mechanical wear, the end face is worn out, which makes the transmission shaft to have the axial displacement or the radial swing. The damage of the machine can be judged by the wear marks caused by the action of these abnormal movements, so as to determine the cause of the leakage. If the wear is normal, the parts of the operation is good, it shows that the coaxial degree is normal, the seal end face leakage is not caused by the seal failure. The leakage is normal, it shows that there is no leakage between the two ends of the surface, but also may be a static seal leakage occurred. Or the installation of the base aperture is not in place, resulting in less than the outer diameter of the seal, resulting in the seal began to work on the production of leakage.
4, chemical corrosion lead to seal leakage
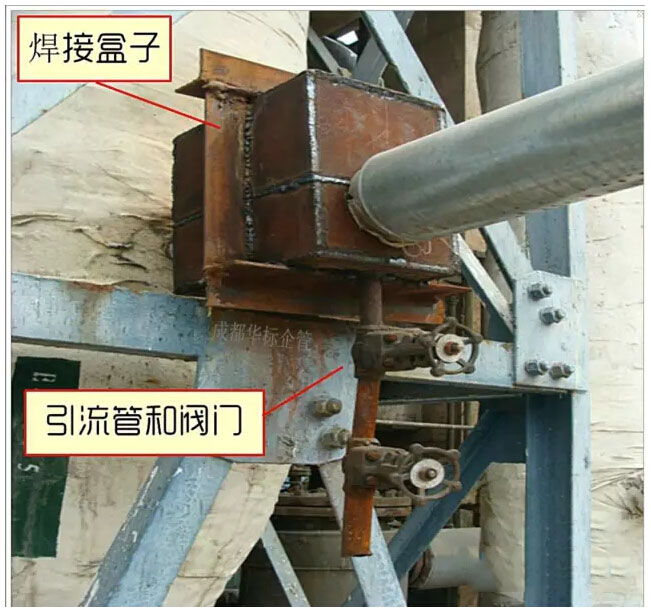
Due to the specific corrosion of the sealing medium, make it contact with the seal will corrosion surface, corrosion will even form a serious pitting corrosion. It will cause a serious impact on the performance of the seal. In the material so high corrosion resistant material to protect the seal in the host facet precision. Practice has proved that the pressure, temperature and other external factors will increase the production of corrosion. Therefore, the two end seal measures to deal with the strong corrosive fluid, it will be because of its contact with the process fluid less and greatly reduce the impact of corrosion on the seal. This is also an important basis for the selection of the sealing structure.
5, parts failure lead to seal leakage
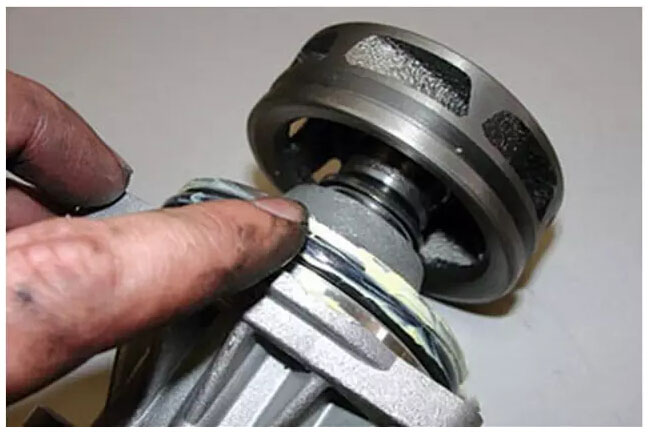
Auxiliary seal ring failure, or failure of the O ring is the two main reasons for the failure of mechanical seal components. The O type ring due to aging, deformation, distortion and other damage due to fault, so in the choice of models should refer to high temperature resistant synthetic rubber, high hardness, when necessary, can also use of composite materials such as rubber coated PTFE sealing ring.
Three, to solve the mechanical seal leakage method
Seal leakage treatment principle
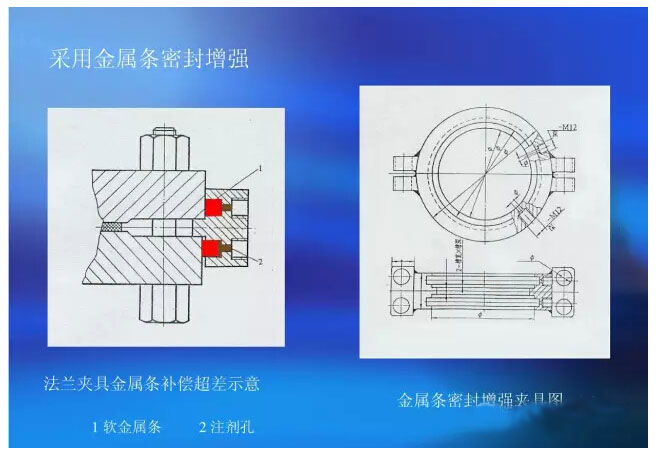
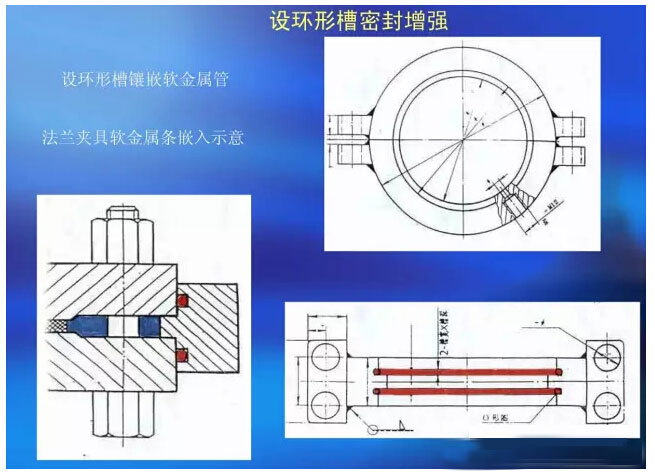
There is a layer of the sealing side of the mask, its shape will have an impact on the sealing effect. There are three kinds of liquid phase, gas phase and gas-liquid mixture, and different process levels have different forms. In the sealed liquid close to saturation, the occurrence of boiling and other conditions, the different phase transition will occur, resulting in different forms. In the design and manufacture of a variety of measures can be used to ensure the stability of the end mask to protect the mechanical seal.
1, caused by the regularity of leakage
Pump rotor shaft over the amount of surplus and channeling momentum, resulting in a flexible mobile ring can not be. Displacement compensation can not be obtained after wear. That in the installation of the seal, you need to ensure that the amount of interference and radial seal, but also in the moving ring after the assembly makes it flexible. If the seal dry friction or galling, shows that the lubricating oil is too small, it is necessary to put the oil level to the high dynamic and static ring sealing surface.
2, small submersible sewage pump leakage
Due to the anti pressure state of the double seal, the sealing surface of the medium debris into the lead grinding shaft; the upper sealing surface or due to bad lubrication of the friction torque between static rings is not balanced, resulting in relative rotation occurs, which is the main reason of grinding shaft a. In order to prevent the production of grinding shaft, the need to ensure that: the lower cover and the oil room clean, prohibit the use of bad lubricating oil, but also to make the oil chamber sealing chamber of the oil line is higher than the dynamic and static ring sealing surface.
3, the pressure caused by leakage
Due to the pressure of the spring than the pressure and the total pressure is not normal formation of high pressure or pressure waveguide mechanical seal leakage occurs, it is difficult to form a liquid membrane, causing the sealing surface to produce thermal deformation. So to strictly according to the operation requirements to assemble the machine, can not appear spring compression amount is not stable phenomenon. In addition, the use of high hardness alloy and ceramic and other high pressure materials, while strengthening the cooling protection, can make the face more reasonable stress, small deformation probability.
Four, summary
Through this paper, we can know that there are differences in the direction of sealing objects will produce vacuum sealing and positive pressure seal. In this case, the two ends of the mechanical seal should be used to improve the lubrication conditions, thus improving the quality of the seal.
Process equipment network finishing release, reproduced please indicate the source.