[introduction] in the surface of the steel alloy plating a layer of zinc in surface treatment technology in appearance, such as the role of the rust, the surface of the zinc layer is a kind of electrochemical protection layer, can prevent metal decay, the method is mainly used in galvanized and galvanized.
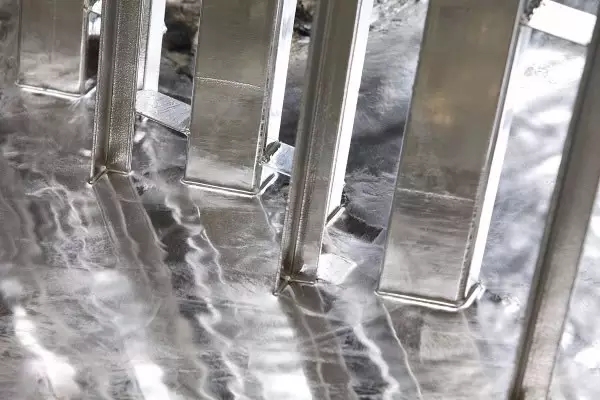
Characteristics of zinc plating
1, process costs: tooling costs, single and low cost
2, typical products: construction, bridges, transportation and furniture surface treatment, etc.
3, the yield is suitable: single piece to large quantities are available
4, quality: the perfect protection layer, the appearance of a large extent depends on the quality of steel
5, speed: fast, basic 10 minutes / cycle
Two, applicable materials

Because the zinc plating process depends on the metallurgical bonding technology, so it is only suitable for steel and iron surface treatment
Three, design considerations
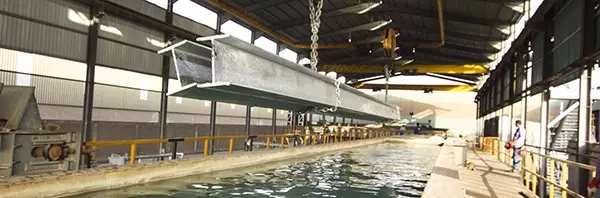
1, uses: zinc plating process uses a wide range of small to diameter 8mm (0.315in) rivets and screws, large to 12m*3m (40*10ft) of the building structure
2, can withstand the temperature: the temperature of zinc plating process is 450° C (840° F), so all galvanized parts of the material must be able to withstand the temperature
3, the existence of risk: some parts of the structure will have a burst of risk, such as the sealing pipe and the work piece of the blind angle
4, matters needing attention: in the zinc plating process, the liquid zinc can cover the exposed surface of the work piece. If you want to be a part of the surface of a workpiece galvanized, need to use high temperature adhesive tape or special coating to cover parts of the surface does not need to be galvanized
5, prior treatment: the need to deal with the surface of the workpiece in advance, if residual oxide film on the surface, will affect the normal deposition of liquid zinc
Four, process costs
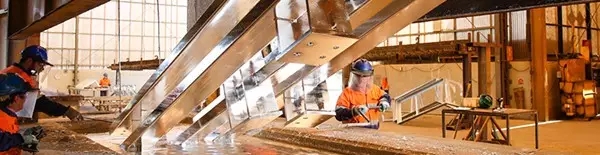
1, the basic characteristics: no mold cost, short cycle, low cost
2, depending on the factors: labor costs, because the surface quality of the workpiece depends largely on the surface of the artificial surface treatment
Five, environmental impact
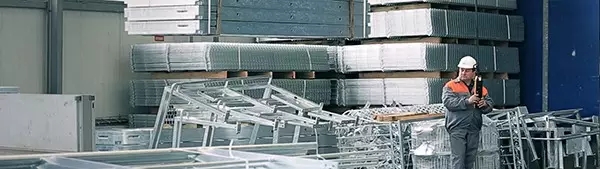
1, a growth: because of galvanizing process for iron and steel was 40-100 years of life, it is good to prevent the workpiece rust and decay, so have a positive effect on the protection of the environment
2, effect of two: zinc plated parts in the service life expires, you can re send back to galvanized trough, the repeated use of liquid zinc will not produce chemical physical waste
Six, process steps
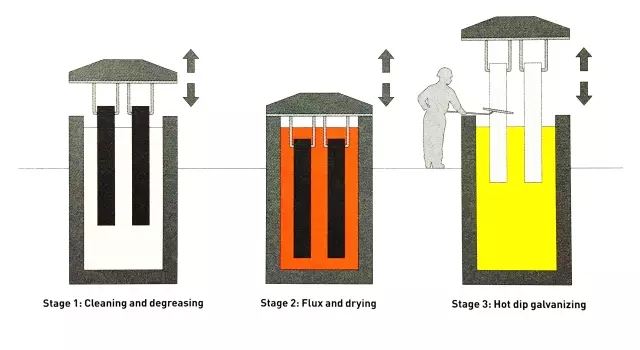
1, remove oil and rust removing oil stains: first the surface of the workpiece in hot alkali solution, and then remove the rust on the surface in hydrochloric acid tank, and is heated to 80° C for the next step of preheating
2, the depth of the surface cleaning: in the ammonium chloride in depth cleaning, to ensure that the workpiece surface can better support the deposition of liquid zinc
3, hot dip galvanized: the workpiece immersion in 450° C liquid zinc pool, 10 minutes after the completion of the removal
Galvanized factory shot
