[introduction] gasket is between two objects of the mechanical seal, if used properly, usually can effectively prevent the leakage of materials between two objects; the improper selection, will cause unnecessary losses.
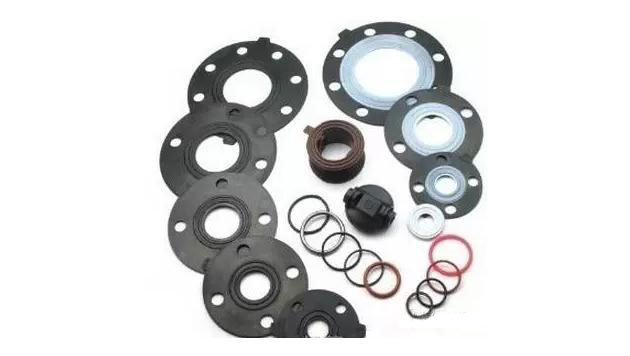
Sealing mechanism of flange gasket
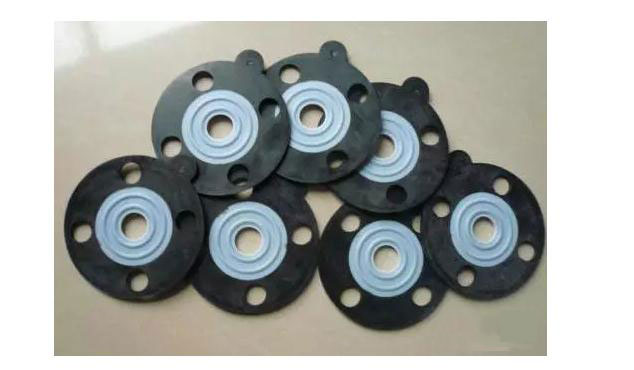
Media flow through the internal and external space of the interface leakage occurs when the sealing surface leakage. The root cause of the leakage is due to the existence of the contact surface gap, and the pressure difference on both sides of the contact surface, the concentration difference is the driving force of leakage. To reduce the leakage, it is necessary to make the contact surface to the greatest degree of fitting, that is, reduce the leakage channel cross-sectional area, increase the leakage resistance, and make it more than the leakage force. When the pressure load on the sealing surface to produce pressing force, can improve the sealing contact surface, when the stress increases enough to cause the surface of the plastic deformation obviously, it can fill the gap seal cover, plug leakage channel.
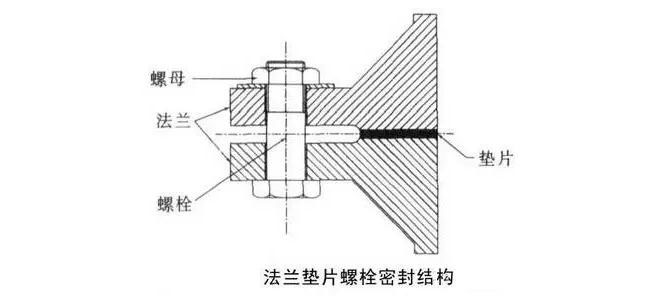
The sealing mechanism of the flange gasket can be divided into the following 2 cases:
1, initial seal
In the assembly when the flange gasket can complete the initial seal fastening bolt pressing gasket, the basic conditions for the production of initial seal is that enough pressure generated between the sealing surface, the preload of gasket compression deformation elastic or elastic-plastic deformation so that the gasket material is compressed, can fill the flange sealing surface is rough. In order to reach the initial channel interface plug leakage sealing requirements.
The preload of the gasket depends on the gasket material's performance, all of which are from the initial tightening force of the bolt, and the flange should have sufficient strength and adequate stiffness to prevent deflection or warping deformation.
2, work seal
The flange gasket bolts of three component system after preloading, when under the action of working medium pressure, the 2 sealing surface of flange will be forced to have a relative separation, the gaskets should be sufficient to compensate for the separation of rebound deformation. Not only such gaskets also require the ability to maintain the sealing interface, that is, there is still enough to maintain the sealing of the residual gasket stress (pressure stress), in order to ensure that the fluid seal.
Two, flange gasket performance
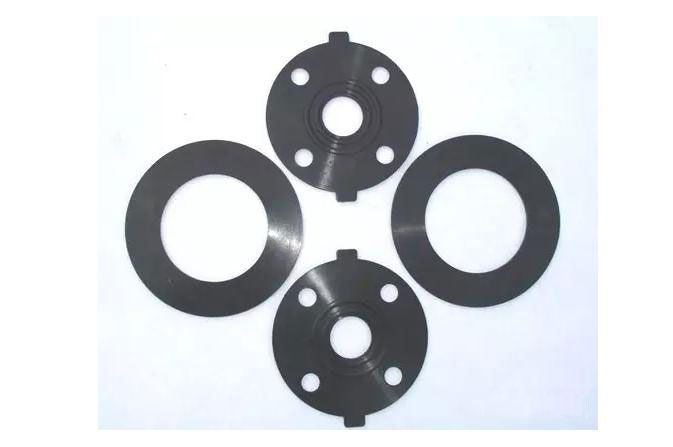
The main factors affecting the flange sealing:
1, bolt preload
2, sealing surface form
3, gasket performance
4, flange stiffness
5, operating conditions
Gasket compression and resilience capacity is a necessary condition for flange seal. The gasket includes deformation of elastic deformation and plastic deformation of two parts, it is only the resilience of the elastic deformation, the resilience of the gasket can be separated better compensation for the flange end face, to adapt to the operating pressure and temperature fluctuations, and good sealing performance.
The gasket surface of the plastic deformation ability is also very important, it can fill the micro uneven on the face, so as to achieve the initial seal between the flange.
Three, the types of flange gasket
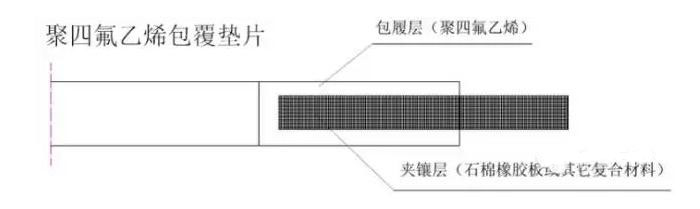
Four, flange gasket selection
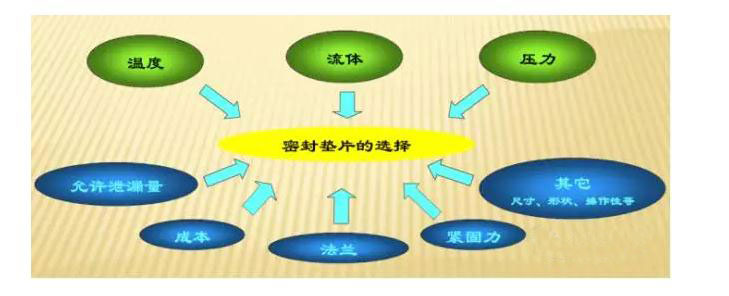
The choice of gasket material is mainly determined by the following three factors: temperature, pressure, medium.
1, the basic principles of selection of gaskets
(1) have a good compression and rebound performance, can adapt to temperature and pressure fluctuations.
(2) have good plasticity, can be a good fit with the flange sealing surface.
(3) to have some metal tendency to stress corrosion cracking (such as austenitic stainless steel flange, gasket) should ensure that the material does not contain impurities caused by excessive corrosion, such as the control of chloride ion content on Corrosion of flange gasket.
(4) non polluting medium.
(5) to seal the highly toxic chemicals, should require gasket with greater security; for the pipeline system for transporting inflammable liquid, requirements on the flange gasket for the maximum pressure and maximum temperature within limits.
(6) when low temperature is not easy to harden, shrinkage is small, high temperature is not easy to soften, creep resistance can be good.
(7) good processing performance, convenient installation and compaction.
(8) non adhesive flange sealing surface, easy removal.
2, different gasket applicable conditions
Common form of flange seal
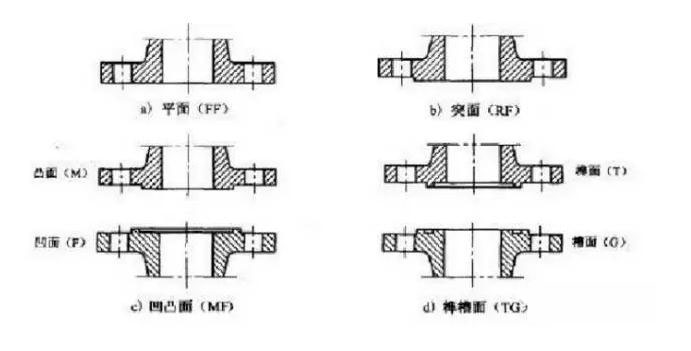
Gasket applicable condition
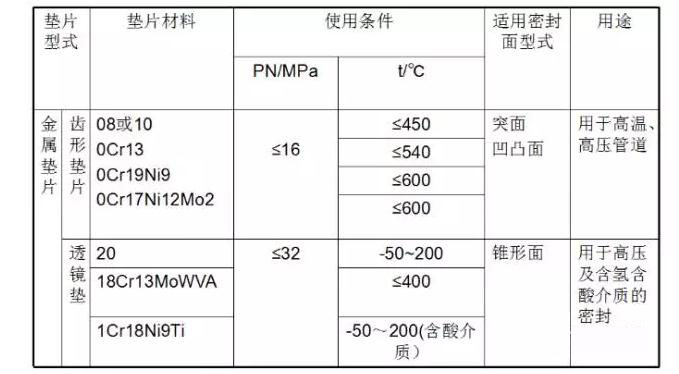
Five, flange gasket installation notes
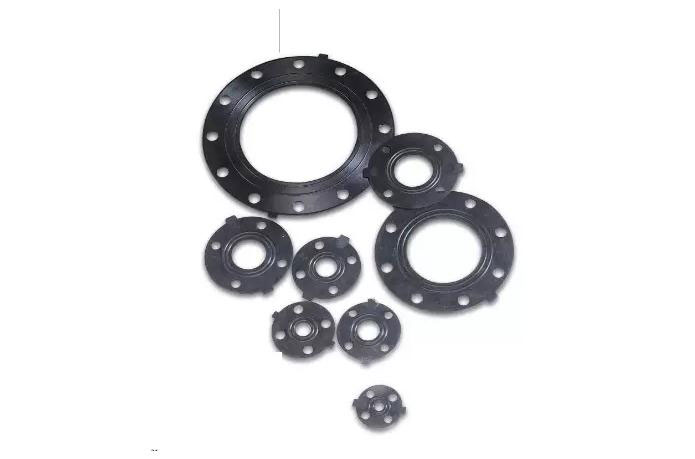
1, gasket installation notes
(1) gasket and flange sealing surface should be clean, not any impact on the sealing performance of the scratches, spots and other defects exist.
(2) gasket than the flange sealing surface diameter should be small, the inside diameter of the gasket should be slightly larger than the inner diameter of the pipe, 2 times the two diameter difference in general gasket thickness, to ensure that the gasket is compressed, not into the inner edge of a container or a pipe, in order to prevent the fluid flow in the vessel or pipe.
(3) gasket preload should not exceed the design requirements, so as to avoid excessive compression of gasket loss of resilience.
(4) when the gasket is pressed, it is best to use a torque wrench. For large bolts and high strength bolts, it is best to use the hydraulic clamping device. Tightening torque should be based on the given pressure pad obtained by calculation, the size of the hydraulic device hydraulic tightening should be determined by calculation.
(5) installation of gaskets, according to the order of the screw nut. But should not be screwed once to reach the design value. Generally at least 3 ~ 2 times should be circular so that the gasket stress distribution is uniform.
(6) pressure vessels and pipelines of flammable and explosive medium, replacing gaskets should use security tools, so as to avoid tool and flange bolts or collide, sparks, causing a fire or explosion.So.
(7) if there is a leak in the pipeline, it must be replaced or adjusted to replace or adjust the mounting pad.
2, gasket installation of special requirements
(1) in the installation of the flange and the flange to match the winding gasket, should pay attention to ensure that the seal and the pipe concentric, generally use the outer ring and the inner surface of the bolt contact to locate, do not allow eccentric installation. The basic installation of tongue and groove face flange sealing surface of spiral wound gasket, and the groove wall should pay attention to keep consistent gaps.
(2) installation of the narrow width of the metal gasket, should be a certain thickness of the gasket plate on the outside, and then press the flange, so as to avoid the filler in the compressed gasket, the metal shell interface (or lap) burst, gasket damage.
(3) when the flange working temperature is higher than 200 degrees, in the flange sealing surface and gasket should be coated with sealant, in order to prevent the high temperature gasket and flange sealing face sintering, to repair and replace the gasket to increase trouble.
(4) the sealing surface is not normal, can be coated with sealant on the sealing surface and then install the gasket. The sealant generally consists of red lead, manganese dioxide, graphite powder and boiled linseed oil (oil) formed after. According to the sealing medium, working temperature and medium pressure and other conditions, the corresponding types and grades of liquid sealant.
(5) for the installation of the ring type metal ring gasket, when the metal ring gasket and flange sealing groove processing is not ideal, can be matched with research to achieve close fitting. For large diameter metal gasket, research is difficult to fill the uneven metal surface can be small, the use of sealants.
Process equipment network finishing release, reproduced please indicate the source.