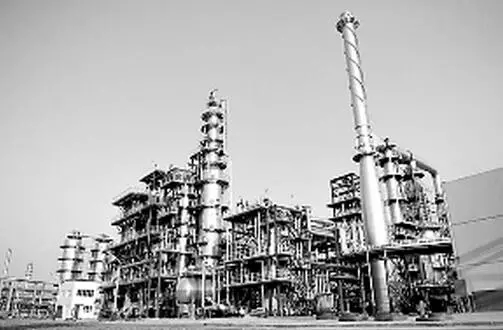
Key parts and equipment
1 key parts
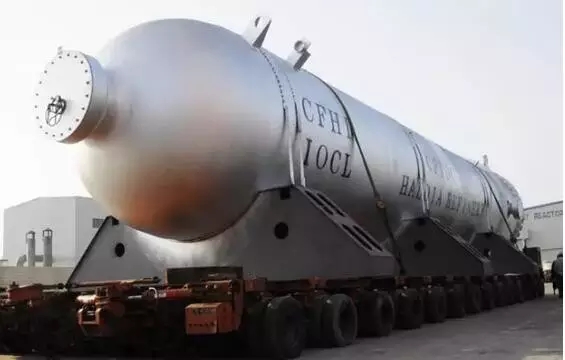
1 heating furnace and reactor area
Heating furnace and reactor zone layout hydrogenation unit with hydrogenation reaction heating furnace, heating furnace, fractions hydrogenation heater, high pressure heat exchangers and other equipment, most of equipment for high voltage equipment, medium high temperature, and heating furnace fire, therefore, the danger area potential comparison large, the main risk for fire and explosion safety is key to prevent the area.
2 high pressure separator and high pressure air cooling zone
There is a high pressure separator and a high pressure air cooler in the high pressure separator and the high pressure air cooling zone. The main risk is fire, explosion and H2S poisoning, so the region is a key security areas.
3 hydrogenation compressor plant
The hydrogen compressor plant layout cycle hydrogen compressor, hydrogen compressor, the area for hydrogen environment of high pressure hydrogen compressor, and pneumatic equipment failure probability, therefore, the potential risk is relatively large, the main risk for fire, explosion and poisoning, is safe to focus on prevention area.
4 fractionation tower area
The equipment fractionator quantity, medium for flammable and explosive materials, the heat pump is should focus on prevention equipment, high-temperature oil leak may cause fire accident, there are a lot of fractionating tower area of fuel gas, liquid hydrocarbon and oil, such as an accident, the consequences will be very serious, in addition. Debutanizer and dry gas and liquefied gas in the high concentration of H2S, a toxic hazard, so the area is safe on the key prevention areas.
2 major equipment
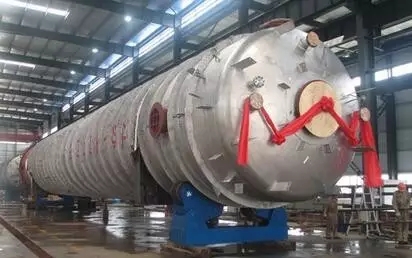
1 hydrogenation reactor
Multiple fixed bed reactor for hydrogenation reactor, hydrogenation reaction belongs to gas liquid solid three-phase trickle bed reactor, hydrogenation reactor cold wall reactor and hot wall reactor two: cold wall reactor with heat insulation lining, the reactor materials of lower grade; no hot wall reactor insulation lining, instead of using the double welding lining material for 2× 1/4Cr-1Mo. Catalyst for hydrogenation reactor for layered filling, intermediate use of quench hydrogen, so the structure of hydrogenation reactor complex, the reactor entrance with a diffuser, feed distribution plate, set scale basket, catalyst supporting plate, cold hydrogen tube, cold hydrogen box, redistribution disc, export oil collector. Component.
The operating conditions of hydrogenation reactor are high temperature, high pressure and hydrogen, and the operating conditions are harsh.
2 high pressure heat exchanger
The reactor has a high discharge temperature and a high enthalpy, so it should be recovered as much as possible. Therefore, the hydrogenation unit is equipped with a high pressure heat exchanger, which is used for the discharge of the reactor and the heat transfer of the raw oil and circulating hydrogen. Now the high pressure heat exchanger is mostly U tube double shell side heat exchanger, the heat exchanger can achieve pure countercurrent heat transfer, improve the heat transfer efficiency, reduce the area of high pressure heat exchanger. The utility model is characterized in that the utility model has the advantages of compact structure, good sealing performance and convenient assembly and disassembly.
The operating conditions of the high pressure heat exchanger are high temperature, high pressure and hydrogen, and there are many static sealing points, so it is easy to leak.
3 high pressure air cooling
The operating conditions of high pressure air cooling for high pressure and hydrogen, is an important equipment in hydrogenation unit, North China refinery hydrocracking device, high pressure air cooling two leak, the device was forced to shut down, therefore, high pressure air cooling design, manufacture and use should be paid more attention.
4 high pressure separator
Effect of high pressure separator is the process of oil gas water three-phase separation, high pressure separator operation conditions for high pressure and hydrogen, the operating temperature is not high, in the presence of water and hydrogen sulfide under corrosive material is enhanced, when in use should be paid more attention. In addition, the liquid level of high pressure separator hydrogenation unit is very important, if the control is not good will have serious consequences, the level is too high, easy to bring into the liquid circulating hydrogen compressor, the compressor damage level is too low, prone to high pressure, low pressure channeling accident, a large number of circulating hydrogen rapidly into the low pressure separator, at this time, if not the low pressure separator safety valve open or discharge is not enough, will be a serious accident. Therefore, from the security point of view is very important to the high-pressure separator.
5 reaction heating furnace
The operating conditions of hydrogenation reaction heating furnace are high temperature, high pressure, hydrogen, and open flame, and the operating conditions are very harsh. Hydrogenation reaction furnace tube material is generally high Cr, Ni alloy steel, such as TP347.
Furnace type hydrogenation furnace for pure radiation chamber of double side radiant heating furnace, the purpose of this design is to increase the intensity of heat radiation tube, reduce the number and length of elbow tube, to reduce the amount of furnace tube, reduce the system pressure. In order to recover the waste heat of the flue gas and improve the thermal efficiency of the heating furnace, a common heat recovery boiler system is provided.
6 new hydrogen compressor
The role of the new hydrogen compressor is to feed the raw material hydrogen into the reaction system, the general import and export of the compressor pressure difference, the flow is relatively small, more use of reciprocating compressors.
Reciprocating compressor compression ratio of each level is generally 2-3.5, according to the hydrogen gas pressure and reaction system pressure, generally 2 to 3 compression.
Most parts of the reciprocating compressor are reciprocating parts, and the flow of the air flow is pulse, so the reciprocating compressor can not run for a long period.
Reciprocating compressor is generally driven by motor, connected by rigid coupling, motor power, low speed, the use of synchronous motor.
7 cycle hydrogen compressor
The function of the circulating hydrogen compressor is to provide circulating hydrogen for the hydrogenation reaction. Recycle hydrogen compressor is &ldquo of hydrogenation unit; ”. If the recycle hydrogen compressor is shut down, the hydrogenation unit can only emergency shutdown.
Recycle hydrogen compressor is the circulation work in the system, the population pressure is generally small, the flow is relatively large, the general use of centrifugal compressor. Because of the small molecular weight of the circulating hydrogen, the energy of the single stage impeller is smaller, so the general speed of the circulating hydrogen compressor is higher (8000-10000r / min), and the series is more (6 ~ 8).
Circulating hydrogen compressorIn addition to the bearing and shaft end seal, almost no relative friction components, and the use of sealed compressor dry gas seal and floating ring seal, instrument monitoring and diagnosis system, perfect plus so circulating hydrogen compressor can long cycle operation, without the use of preparation machine.
Circulating hydrogen compressor is driven by steam turbine, which is because of the high speed of steam turbine, and its speed is adjustable.
8 automatic back flush filter
The raw material of hydrogenation contains mechanical impurities, if not removed, it will be deposited on the top of the reactor, so that the reactor pressure difference is too large to be forced to shut down, shorten the operation cycle. Therefore, the hydrogenation of raw materials need to be filtered, and now use automatic backwashing filter.
Automatic backwash filter inside the Johnson filter, the filter can filter out ≥ solid impurities 25 / 1m, when the filter pressure difference is greater than the set value (0.1 ~ 0.18MPa), backwashing start-up mechanism, backwash, wash away the impurities on the filter.
Risk factors and preventive measures
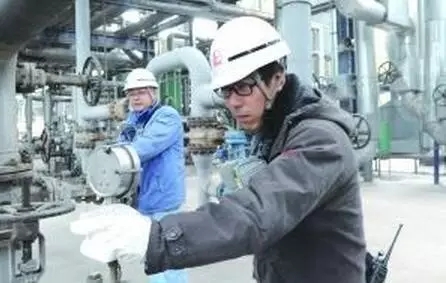
1 the risk factors and preventive measures during the shutdown
1 the risk factors and preventive measures
(1) hydrogenation reaction system, drying oven
Hydrogenation reaction system, drying oven to remove water in the reaction system, natural water and crystal water removal of refractory material in the heating furnace, sintering of refractory material, increase the strength and service life of refractories. The heating furnace stove, device should be the introduction of fuel gas, should be airtight and isolation work earnestly in the gas feed gas before ignition, the general requirements of oxygen content in the fuel gas is less than 1%. Preventing gas leakage and channeling to other systems. The ignition of the heating furnace should be thoroughly cleaned with steam, which can not be residual flammable gas. The heating furnace should be strictly according to the baking curve heating and cooling, avoid excessive heat, rapid evaporation of refractory material in water caused by furnace wall collapse.
(2) hydrogenation reactor catalyst loading
The catalyst loading should be carried out strictly according to the catalyst loading scheme, and the loading of the catalyst has an important influence on the operation and operation cycle of the hydrogenation unit. The catalyst should be carefully examined before and after loading, and the dust content of the catalyst should be checked. Catalyst loading is the best choice in the dry and sunny weather, to ensure uniform catalyst loading, reaction will occur during startup or drift or &ldquo device; hot ” influence the normal operation of the unit. When the catalyst loading staff need to enter the reactor, therefore, special attention should be paid to the staff labor protection and safety problems, need to wear protective clothing, with a breathing mask for oxygen or air into the reactor, the staff can not take other debris, to prevent foreign bodies into the reactor (general catalyst by professional professional company).
(3) substitution of hydrogenation reaction system
The replacement of the hydrogenation reaction system is divided into two stages, that is, the replacement of the air environment for the nitrogen environment, the nitrogen environment for the hydrogen environment. Need to pay attention to in the air replacement for nitrogen environment, oxygen content after the completion of the replacement should be < 1%, otherwise the system into hydrogen dangerous; in nitrogen environment replacement for hydrogen environment should pay attention to, make the system have a suitable gas average molecular weight, to ensure the operation in a circulating hydrogen compressor the suitable conditions, the general hydrogen purity for 85% more.
(4) hydrogenation reaction system airtight
Hydrogenation reaction system of gas is a very important work in hydrogenation unit in start-up stage, the main purpose of work is to find the leak tightness, eliminate the hidden danger in the plant, to ensure the safe operation of the device. The air tightness of the hydrogenation reaction system is divided into different pressure levels, and the medium used in the low pressure gas phase is nitrogen. Because of the hydrogenation reactor material with cold brittleness, general requirements of the system pressure is greater than 2.0MPa, the wall of the reactor temperature is not lower than 100 DEG C, so hydrogen 2.0MPa airtight after the first recycle hydrogen compressor open reaction furnace ignition system, heating, when the reactor wall temperature greater than 100 DEG C, the system pressure, as air pressure stage.
(5) cold oil fractionation system
Cold oil fractionation system is to test the fractionation system of pump, instruments and other equipment, cold oil fractionation system should pay attention to the correct process changes, do not run oil and without oil leakage.
(6) thermal oil fractionation system
The purpose is to heat oil fractionation system check the running status of distillation system of thermal equipment, ready to receive the reaction of oil. When the temperature of the heating system is about 100~C, the water cut should be paid attention to in order to prevent the pump from pumping out. Heat up to 250 degrees Celsius should be carried out when the heat tight.
(7) the temperature rise and pressure rise of hydrogenation reaction system
When the temperature rise and pressure rise of the hydrogenation reaction system should be carried out according to the requirements of temperature rise and pressure speed, the heating speed of the system is about 20 DEG C, and the speed of the system is not more than 1.5MPa / h. Such as temperature, speed is too fast to cause system leakage.
(8) vulcanization and passivation of hydrogenation catalyst
The catalyst of hydrogenation reaction is oxidation before starting, and the oxidation catalyst has no hydrogenation activity. Method of catalyst have wet curing and dry curing two methods, curing agents are commonly used carbon disulfide, DMDS, sulfide catalysts were very high H2S concentration system, sometimes as high as 1% or more, therefore, should pay special attention to the problem of hydrogen sulfide poisoning.
The new hydrocracking catalyst has high hydrocracking activity. In order to suppress this activity, it is necessary to. For anhydrous ammonia passivation agent. When the hydrocracking catalyst is passivated, the hydrogen sulfide concentration in the system should not be less than 0.05%.
(9) the hydrogenation reaction system is gradually changed into raw oil
After the completion of the vulcanization and passivation process of the hydrogenation catalyst, the low nitrogen oil of the hydrogenation reaction system needs to be switched into the raw oil gradually. In the process of switching, the change of the temperature rise of the reactor should be paid close attention to.
(10) device operation and adjustment
After the completion of the material transfer process of the hydrogenation reaction system, the operation of the device should be further adjusted so that the quality of the product is qualified.2 the risk factors and preventive measures during shutdown
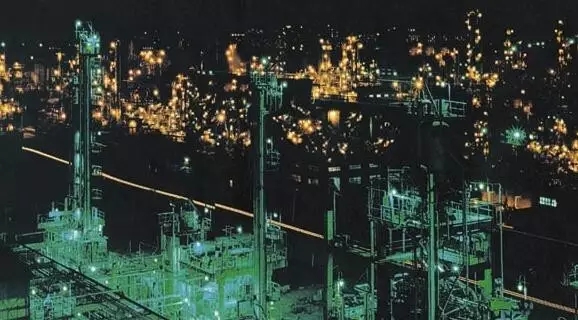
(1) cooling and lowering of the reaction system
Hydrogenation plant shutdown first reaction system cooling down. In this process, we should follow the principle of cooling down. To reduce the amount of material into the reaction system, the airspeed decreases, increase the rise of hydrogenation reactor temperature, prone to reaction temperature &rdquo “ fly phenomenon. The so-called “ fly temperature ” is the reactor temperature rising rapidly, so that the phenomenon of uncontrolled.
(2) replace the whole system with low doubt
The raw oil hydrogenation unit is generally heavy, high pour point, during a shutdown in easy condensation catalyst, pipelines and equipment. To avoid the above situation, in shutdown before the application of low pour point oil replacement system, with low pour point oil is the second oil.
(3) stop reacting feed pump
When the feed is cut off, it should be noted that the reactor temperature should be appropriate, so that the cracking reactor has no obvious temperature rise.
(4) circulating oil and hydrogen gas extraction in the reaction system
Cut off the reaction after feeding, reaction furnace heating, with oil storage in catalyst by thermal cycle hydrogen, determined according to the requirements of catalyst heat hydrogen temperature should be provided, usually flail degrees Celsius, the temperature of hot hydrogen extraction can not be too high, in order to avoid the hot hydrogen reduction catalyst.
(5) cooling and depressurization of reaction system
Hydrogenation reaction system cooling and depressurization at the required speed.
(6) reaction system N: replacement
The reaction system was replaced with N, N: environment, so that the system of hydrogen hydrocarbon concentration < 1%.
(7) unloading catalyst
Use the carbon containing catalyst is prone to spontaneous combustion in the air in the reactor is catalyst unloading operations in the N2 gas environment, must be professional unloading agent company personnel into the reactor for unloading, therefore, the use of N in the catalyst unloading barrel or dry ice to protect the catalyst, the catalyst to avoid spontaneous combustion.
(8) cleaning and anticorrosion of hydrogenation equipment
Equipment and parts of high-pressure partial hydrogenation device, cleaning application of lye in work, in order to avoid the occurrence of corrosion in contact with air, the damage of equipment. In addition, the equipment of the high sulfur system is mainly used to flush the water before the treatment, so as to avoid the spontaneous combustion of iron sulfide in the air.
(9) the oil return and purge
Hydrogenation unit shutdown, the device should be stored in the oil exit and purge clean, to ensure no dead angle.
(10) the treatment of the auxiliary system
After the shutdown of the hydrogenation unit, the torch system, the underground sewage system and other auxiliary systems are cleaned, and the blind plate is used to protect the device and the system so as to enable the equipment to meet the maintenance conditions.
3 risk factors and preventive measures during normal production
1 comply with “ first cooling down after the amount of ” principle
The normal operation of the hydrogenation unit must comply with the “ the first cooling down after the amount of ” “ the first mention of the amount of temperature after the ” the principle of preventing “ fly temperature ” accident occurred.
2 reaction temperature control
The reaction temperature is the most important control parameter, and the hydrogenation reaction temperature and the bed temperature must be controlled strictly according to the technical specifications.
3 high pressure separator liquid level control
High pressure separator liquid level is a very important process in hydrogenation unit control parameters, such as the level too high to recycle hydrogen with liquid, damage to recycle hydrogen compressor; such as the level is too low to high pressure low pressure low pressure part caused by channeling accident, equipment damage, oil and gas leakage, and even more serious consequences. Therefore, we should strictly control the high pressure separator level, often check the accuracy of liquid level meter.
4 reaction system pressure control
Hydrogenation reaction system pressure is an important parameter in process control, reaction pressure effect of hydrogen partial pressure, has a direct influence on the hydrogenation reaction, many factors affecting the reaction of hydrogenation unit of system pressure, pressure control should be economic and reasonable, the control scheme of the convenience of the reaction system.
5 control of the purity of circulating hydrogen
Effect of hydrogen purity of circulating hydrogen partial pressure, has a direct influence on the hydrogenation reaction, hydrogenation unit is an important parameter, many factors affect the circulating hydrogen purity, nature, raw oil catalyst properties, reaction temperature, pressure, hydrogen purity, tail hydrogen emissions and other factors affect the circulating hydrogen the operation conditions for the purity of hydrogen tail emission. Increase the tail hydrogen emission and increase the purity of circulating hydrogen; reduce the purity of circulating hydrogen.
High purity hydrogen cycle, hydrogen pressure will be higher, is beneficial, but the hydrogenation reaction, high purity hydrogen cycle by a large number of emissions of hydrogen, tail at the expense of increased material consumption; circulating hydrogen purity and low hydrogen pressure will be low, is not conducive to the hydrogenation reaction, and hydrogen purity low cycle the average molecular weight, hydrogen, unchanged in circulating hydrogen compressor speed, the system pressure will increase, the power consumption of circulating hydrogen compressor will increase. Therefore, the purity of circulating hydrogen should be controlled properly.
Process equipment network release, please indicate the source.