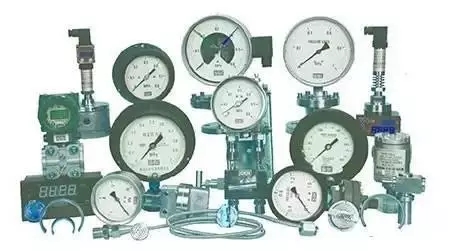
The instrument plays an important role in detecting, displaying, recording and controlling the technological parameters in the process of industrial production.
The detection process is the basic means of understanding and control of industrial production, can accurately understand the whole process only at any time, and control, in order to ensure the smooth production process, with high productivity, small consumption of the production of qualified products. So, don't look at the instrument inconspicuous, but it is the most indispensable! In this paper, we introduce the selection of automatic instruments, temperature instruments, pressure meters, flow meters and level meters. The content is very comprehensive!
[1. general principles of automatic instrument selection]
The general principles for the selection of instrumentation (components) and control valves are as follows:
1. process conditions
In the process of temperature, pressure, flow rate, viscosity, corrosion, toxicity, ripple factor is the main conditions to determine the selection of instruments, it is related to the selection of instrument rationality, the service life of the instrument and workshop fire, explosion, security and other issues.
2. importance of operation
The importance of the parameters of each detection point in operation is the basis of selecting, indicating, recording, integrating, alarming, controlling and remote control of the instrument. In general, little impact on the process, but often need to monitor variables, optional indicator type; an important variable to always need to understand the change trend, should be recorded; and some of the process of great influence, and to monitor the variable should be set to control; related to the material balance and power consumption the measurement requirements or accounting variables, are advised to set up some may affect production or product; safety variables, are advised to set up alarm.
3., economic and unity
The selection of the instrument is also decided by the scale of investment, and the necessary economic accounting should be carried out under the precondition of meeting the requirements of process and automatic control to obtain the appropriate performance / price ratio.
In order to facilitate the maintenance and management of the instrument, the uniformity of the instrument should be noticed in the selection. Try to choose the same series, same specifications, models and products of the same manufacturer.
4. the use and supply of instruments
Selection of instruments should be more mature products, proven by field use, reliable performance; at the same time, we should note that the selection of instruments should be sufficient supply of goods, will not affect the progress of construction projects.
[type selection of 2. temperature instrument]
(I) general principles
1. units and scales (scales)
The scale (scale) unit of a temperature instrument adopts a Celsius temperature (centigrade).
2. detecting the insertion length of the element
The choice of insertion length shall be based on the principle that the detected element is inserted into the measured medium and the temperature is sensitive and representative. But in general, in order to facilitate the exchange, often the whole device unified selection of one to two block length.
When installed on flues, furnaces and masonry equipment with insulation materials, they should be chosen according to actual needs.
Check the element protection sleeve material should not be less than equipment or pipe material. If the product cover is too thin or corrosion resistant (such as armored thermocouple), additional protective sleeve shall be added.
Installed in flammable and explosive places on the zone of electrical contact temperature instruments, temperature switches, temperature detection (measurement) components and transmitters, explosion-proof type should be used.
(two) selection of local temperature instruments;
1. accuracy level
General industrial thermometer: use 1.5 or 1.
Precision measurement and laboratory thermometers: grade 0.5 or 0.25 shall be used.
2. measuring range
The highest measuring value is not more than 90% of the upper limit of the measuring range of the instrument, and the normal measuring value is about 1 / 2 of the upper limit of the measuring range of the instrument.
The pressure thermometer shall be measured between 1 / 2~3 / 4 of the upper limit of the measuring range of the instrument.
3. bimetallic thermometer
In meeting the requirements of measuring range, working pressure and accuracy, priority should be given to selection.
Watchcase diameter generally choose φ 100mm, in the poor lighting conditions, high position and observation distance of the place, should choose φ 150mm.
Instrument shell and protective pipe connection mode, generally should use universal type, or in accordance with the principle of convenient observation, select axial or radial type.
4. pressure thermometer
Applicable to 80 DEG C, low temperature, can not be observed near vibration and the accuracy is not high on the spot or on site display.
5. glass thermometer
The utility model is only used for measuring special occasions with higher accuracy, less vibration, no mechanical damage and convenient observation. However, glass mercury thermometers are not suitable for mercury exposure.
6. base type instrument
In situ or site installation, measurement, control (adjustment) instrument, should choose base type temperature instrument.
7. temperature switch
It is suitable for occasions where temperature measurement requires contact signal output.
(three) the selection of central temperature instrument;
1. detecting (measuring) components
(1) according to the range of temperature measurement, the corresponding thermocouple, thermal resistor or thermistor are selected.
(2) thermocouples are suitable for general occasions. Thermal resistance is applied to the absence of vibration. Thermistors are suitable for occasions requiring rapid measurement of reaction speed.
(3) according to the requirement of the response speed of the measuring object, the following detecting and measuring element can be used:
Thermocouples: 600s, 100s, and 20s three;
Thermal resistance: 90 ~ 180s, 30 ~ 90s, 10 ~ 30s and < 10s four;
Thermistor: < 1s.
(4) according to the use of environmental conditions, the wiring boxes are selected according to the following principles:
Ordinary type: a place with better conditions;
Splash proof or waterproof: damp or open-air place;
Flameproof: flammable and explosive places;
Socket type: only for special occasions.
(5) the thread connection can be used in general, and the flange connection shall be used for the following occasions:
Install on equipment, lining, pipes, and non-ferrous pipes;
Crystalline, scarred, plugged and strongly corrosive medium;
Flammable and explosiveVirulent medium.
(6) thermocouples and thermal resistance used for special occasions:
When the temperature is higher than 870, the hydrogen content is greater than 5%, the inert gas and the vacuum occasion, the tungsten rhenium thermocouple or the blowing thermocouple is selected;
Surface and armored thermocouple and thermal resistance of equipment, pipe outer wall and swivel surface temperature;
Wear resistant thermocouples are used in media containing solid particles;
In the same detecting element protection bushing, multipoint (support) thermocouple is used when multipoint temperature measurement is required;
In order to save the special protection tube material (such as tantalum), to improve the response speed or to request the device to be bent, the armored thermocouple can be used.
2. transmitter
The transducer shall be used in the measurement or control system that is compatible with the standard signal display instrument.
In order to meet the design requirements, it is recommended to use the integration of measurement and transmission.
3. display meters
(1) single point selection of general display indicator, multi-point display should use digital indicators, request access to historical data, should use the general recorder.
(2) signal alarm system, should be selected with a contact signal output indicator or recorder.
(3) it is better to choose medium recording instrument (such as 30 point recorder) for multi-point recording.
4. selection of auxiliary equipment
(1) when a display instrument is used at many points, a switch with reliable quality shall be selected.
(2) temperature measurement using thermocouples below 1600 DEG C, when the cold end temperature changes so that the measurement system can not meet the accuracy requirements, and supporting the display instrument and the cold end temperature automatic compensation function, should choose the cold end temperature automatic compensator.
(3) compensating wire
A. according to the thermocouple number, graduation number and the use of environmental conditions, should be used to meet the requirements of the compensation wire or compensation cable.
B. use different levels of compensation wire or compensation cable according to the ambient temperature:
20 ~ + 100 DEG C with ordinary level;
40 ~ 250 heat-resistant grade C.
C. if there is a power cut, heating or strong current or magnetic field, shielded or compensated cable shall be used.
The cross-sectional area of the D. compensating wire shall be determined by the reciprocal resistance of its laying length, and by the display of the instrument, transmitter or computer interface, allowing the input external resistance.
[type selection of 3. pressure gauges]
(1) selection of pressure gauges
1. select in accordance with the use of the environment and the nature of the measuring medium
(1) closed type plastic pressure gauge should be chosen in the circumstance of strong corrosivity, dust and easy spraying liquid.
(2) dilute nitric acid, acetic acid, ammonia and other general corrosive medium, should use acid resistant pressure gauge, ammonia pressure gauge or stainless steel diaphragm pressure gauge.
(3) dilute hydrochloric acid, hydrochloric acid gas, heavy oil class and its similar strong corrosive, containing solid particles, viscous liquid and other media, diaphragm pressure gauge or diaphragm pressure gauge should be used. The material of the diaphragm or diaphragm must be selected according to the characteristics of the measuring medium.
(4) crystallization, scarring, and high viscosity and other media, diaphragm pressure gauges should be used.
(5) where strong mechanical vibration, vibration proof pressure gauge should be selected or marine pressure gauge.
(6) in inflammable and explosive situations, if the electric contact signal is needed, the explosion proof electric contact pressure gauge shall be used.
(7) special pressure gauges shall be used for the following measuring media:
Gas ammonia, liquid ammonia: ammonia pressure gauge, vacuum gauge, pressure vacuum meter;
Oxygen: oxygen pressure gauge;
Hydrogen: hydrogen pressure gauge;
Chlorine: chlorine resistance pressure gauge, pressure vacuum meter;
Acetylene: acetylene pressure gauge;
Hydrogen sulphide: sulfur resistance manometer;
Lye: alkali resistance pressure gauge, pressure vacuum meter.
2. level of accuracy
(1) general measurement of pressure gauges, diaphragm pressure gauges and diaphragm pressure gauges, should choose 1.5 or 2.5.
(2) the pressure gauges for precision measurement and verification shall be of class 0.4, class 0.25 or class 0.16.
3. exterior size choice
(1) pressure gauges mounted on pipes and equipment, nominal diameter &phi, 100mm or φ 150mm.
(2) the pressure gauge installed on the instrument pneumatic pipe and its auxiliary equipment, nominal diameter is &phi, 60mm.
(3) a pressure gauge installed at low illumination, high position and difficult to observe the indication value; nominal diameter is φ 200mm or φ 250mm.
4. selection of measuring range
(1) when measuring the steady pressure, the normal operating pressure shall be 2 / 3~1 / 3 of the upper limit of the instrument measuring range.
(2) when measuring fluctuating pressure (such as pump, compressor and fan outlet pressure), the normal operating pressure shall be 1 / 2~1 / 3 of the upper limit of the instrument measuring range.
(3) when measuring high and medium pressure (greater than 4MPa), the normal operating pressure shall not exceed 1 / 2 of the upper limit of the instrument measuring range.
5. units and scales (scales)
(1) all units of pressure instruments shall be used as legal units of measurement. Namely: kPa (Pa), kPa (kPa) and MPa (MPa).
(2) for international design projects and imported instruments, international standards or corresponding national standards may be adopted.
(two) selection of transducer and transducer
(1) transmitter should be used when transmitting standard signals (4 to 20mA).
(2) in case of inflammable and explosive, pneumatic transmitter or explosion-proof type electric transmitter shall be adopted.
(3) the flange type transducer shall be used for crystallization, scarring, blocking, viscous and corrosive medium. Materials that are in direct contact with the media must be selected according to the characteristics of the medium.
(4) when the environment is good, the measurement accuracy and the reliability requirement are not high, the resistance type, inductance type remote pressure gauge or Holzer pressure transmitter can be used.
(5) when measuring small pressure (less than 500Pa), micro differential pressure transmitter can be used.
(three) selection of mounting accessories
(1) measuring water evaporation;When the steam and temperature are greater than 60 DEG C, the spiral or U shaped bend should be used.
(2) when measuring the gas which is easy to liquefy, if the pressure point is higher than the instrument, the separator should be selected.
(3) dust collector should be selected when measuring dust containing gas.
(4) when measuring fluctuating pressure, damper or buffer should be used.
(5) when the ambient temperature is near or lower than the freezing point or freezing point of the measuring medium, heat insulation or heat tracing measures shall be adopted.
(6) the instrument protection (temperature) box shall be used for the following occasions.
Open mounted pressure switches and transmitters.
Pressure switches and transmitters installed in a factory building with severe atmospheric corrosion, dust and other harmful substances.
[four. Selection of flow meters]
(I) general principles
1. scale selection
The instrument scale should meet the requirements of the instrument scale modulus. When the scale reading is not an integer, it is convenient for reading conversion and also can be chosen by integer.
(1) the range of the root mean square
The maximum flow shall not exceed 95% of the full scale;
The normal flow is 70% to 85% of the full scale;
Minimum flow is not less than 30% of full scale.
(2) linear scale range
The maximum flow shall not exceed 90% of the full scale;
The normal flow is 50% to 70% of the full scale;
Minimum flow is not less than 10% of full scale.
2. instrument accuracy
The flow meters used for energy measurement shall conform to the provisions of the general provisions of the enterprise on the allocation and management of energy measuring instruments (for Trial Implementation).
(1) measurement for the settlement of fuel in and out plants; ± 0.1%;
(2) the measurement of technical and economic analysis in workshop, team and process, ± 0.5% ~ 2%;
(3) for industrial and civil water metering, ± 2.5%;
(4) steam metering including superheated steam and saturated steam; ± 2.5%;
(5) measurement of natural gas, gas and household gas; ± 2%;
(6) metering of oil used in key energy equipment and process control; ± 1.5%;
(7) the measurement of other energetic refrigerants (such as compressed air, oxygen, nitrogen, hydrogen, water, etc.) used in process control, ± 2%.
3. flow unit
Volume flow using m3/h, l/h;
Mass flow using kg/h, t/h;
Under normal conditions, the volumetric gas flow rate is Nm3/h (0, 0.1013MPa).
(two) general fluid, liquid, steam flow measuring instrument type selection;
1. differential pressure flowmeter
(1) throttling device
Standard throttling device
For general fluid flow measurement, a standard throttling device (standard orifice plate, standard nozzle) shall be used. The selection of standard throttling devices must comply with the requirements of GB2624-8l or international standard ISO 5167-1980. If new national standards are stipulated, new regulations shall be applied.
Nonstandard throttling device
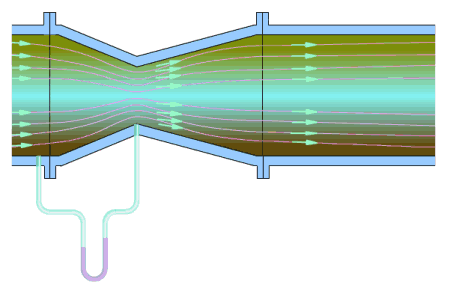
Venturi tubes may be used in accordance with the following conditions:
1. accurate measurements under low pressure losses are required;
2. the tested medium is clean gas and liquid;
3. the inner diameter of the pipe is in the range of 100 ~ 800mm;
4. fluid pressure is less than 1.0MPa.
Double hole plates are available for those who meet the following conditions:
1. the tested medium is clean gas and liquid;
2. Reynolds number is greater than (equal to) 3000, less than (equal)) within 300000 range.
In accordance with the following conditions, optional 1 / 4 round nozzle;
1. the tested medium is clean gas and liquid;
2. Reynolds number greater than 200, less than 100000 range.
The optional round hole plate shall be available to those who meet the following requirements:
1. dirty medium (such as blast furnace gas, mud, etc.) that may produce sediment around the orifice plate;
2. must have a horizontal or inclined pipe.
Selection of pressure taking mode
Should consider the whole project as much as possible to adopt a unified way to take the pressure.
Angle tap or flange pressure are adopted.
According to the use conditions and measurement requirements, you can use the distance to take pressure and other pressure extraction methods.
(2) selection of differential pressure range of differential pressure transmitter
The choice of differential pressure range should be determined according to calculation. Under normal circumstances, according to the level of fluid pressure, should be selected:
Low differential pressure: 6kPa, 10kPa;
Medium pressure: 16kPa, 25kPa;
High differential pressure: 40kPa, 60kPa.
(3) measures to improve measurement accuracy
Temperature and pressure fluctuations of the fluid should be taken into account the temperature, pressure, compensation measures;
When the rotating flow straight pipe length is insufficient or in the pipeline, should consider fluid correction measures, the diameter of the corresponding co opted rectifier.
(4) special type differential pressure flowmeter;
Steam flowmeter
The flow rate of saturated steam, when the required accuracy is not higher than 2.5, and for local or remote accumulation, steam flowmeter can be used.
Inner orifice plate type flowmeter
The micro flow measurement of clean liquid, steam and gas without suspension, when the range ratio is not more than 3 to L, the measuring accuracy is not high, and the pipe diameter is DN < 50mm, the inner hole plate flowmeter can be used. When measuring steam, the temperature of the steam is not greater than 120 degrees centigrade.
2. area flowmeter
When the accuracy is not higher than 1.5, and the range ratio is not greater than 10: 1, the rotor flowmeter can be used.
(1) glass rotor flowmeter
Small volume, small flow, pressure is less than 1MPa, the temperature below 100 DEG C clean transparent, non-toxic, no combustion and explosion danger and no corrosion of glass without adhesion of fluid flow can be used to indicate, glass rotor flowmeter.
(2) metal pipe rotor flowmeter;
Common metal tube rotor flowmeter
Easy to vaporize, easy to coagulate, poisonous, flammable, explosive, magnetic freeMaterials, fibres and wear materials, as well as medium and small flow measurements of stainless steel (1Crl8Ni9Ti) corrosion free fluids, can be used to indicate or transmit signals in place.
Special metal tube rotor flowmeter
1. metal tube rotor flowmeter with jacket
When the tested medium is easy to crystallize or vaporize or have high viscosity, a metal pipe rotor flowmeter with a jacket can be selected. A heating or cooling medium in a jacket.
2. corrosion resistant metal pipe rotor flowmeter
For corrosive medium flow measurement, the corrosion resistant metal pipe rotor flowmeter can be used.
(3) rotor flowmeter;
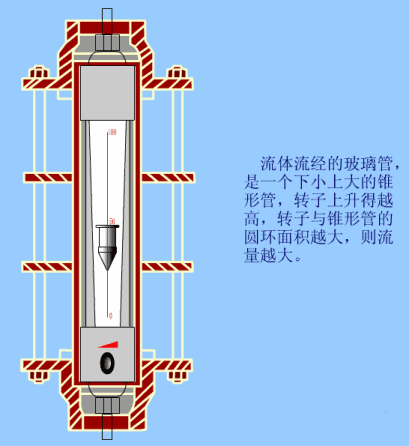
Requires vertical installation with a slope no greater than 5°. The fluid shall be installed from bottom to top and should be vibration less, easy to observe and maintain, and shall be provided with upper and lower shut-off valves and by-pass valves. For dirt media, filters must be installed at the inlet of the flowmeter.
3. speed flow meter
(1) target type flowmeter;
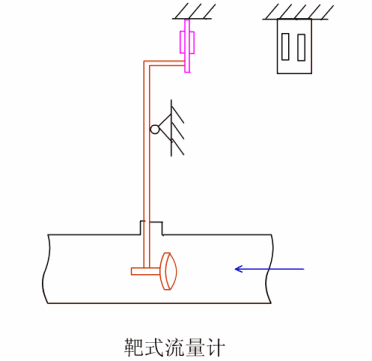
The liquid flow measurement with a higher viscosity and a small amount of solid particles can be used when the measurement accuracy is not higher than 1.5 and the range ratio is no more than 3 to 1.
The target flowmeter is usually installed on a horizontal pipe. The length of the front straight pipe section is 15 to 40D, and the length of the back straight pipe section is 5D.
(2) turbine flowmeter;
Clean gas and kinematic viscosity is not greater than 5× 10-6m2 / s clean liquid flow measurement; when required accurate measurement, the range ratio is not greater than 10: 1, you can use the turbine flowmeter.
The turbine flowmeter shall be installed on the horizontal pipe to fill the whole pipe with the upper and lower cut-off valves and bypass valves, as well as to set up the filter in the upstream, and to set up the drain valve at the downstream.
Length of straight pipe: upstream shall be no less than 20D and downstream shall be no less than 5D.
(3) vortex flowmeter (Carmen vortex flowmeter or vortex flowmeter);
For measuring large and medium flow of clean gas, steam and liquid, a vortex flowmeter can be used. Low speed fluid and viscosity greater than 20× 10-3pa· s liquid measurement, it is not suitable to use vortex flowmeter. The speed of the pipeline should be checked and checked when choosing.
The flowmeter has the characteristics of less pressure loss and convenient installation.
Straight pipe section requirements: upstream from 15 to 40D (depending on piping conditions); upstream rectifier, the upstream is not less than 10D; downstream of at least 5D.
(4) water meter;
When the flow rate of local accumulated water is equal to less than 30: 1, the water meter can be used.
The water meter is installed on the horizontal pipe, and the length of the straight pipe is as follows: the upstream is no less than 8D, and the downstream is no less than 5D.
(three) selection of corrosion, conduction, or flow measuring instruments with solid particles
1. electromagnetic flowmeter
Flow measurement for liquid or homogeneous liquid solid two phase media with conductivity greater than 10&mu and S / cm. With good corrosion resistance and abrasion resistance, no pressure loss. Can measure a variety of strong acid, alkali, salt, ammonia water, mud, pulp, pulp and other media.
The installation direction can be vertical, horizontal, or inclined, and the liquid must be vertical from bottom to top when mounted vertically. For liquid-solid two-phase media, it is better to install vertically.
When installed in horizontal pipelines, should make the fluid filled pipe, and make the transmitter electrodes in the same horizontal plane; the length of straight pipe, not less than 5 ~ 10D in the upstream and downstream of not less than 3 ~ 5D or no requirements (different manufacturers, different requirements).
The transmitter shall not be located in a place where the field strength is greater than 398A / m.
2. non standard throttling device
See above
(four) the selection of high viscosity fluid flow measuring instrument
1. displacement flowmeter
(1) elliptic gear flowmeter;
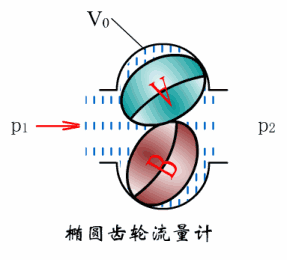
Clean, high viscosity liquid requires more accurate flow measurement. When the equivalence ratio is less than 10: 1, elliptical gear flowmeter can be used.
The elliptical gear flowmeter shall be installed on the horizontal pipe and the dial dial shall be in the vertical plane. The upper and lower shut-off valves and bypass valves shall be provided. Upstream should be equipped with filters.
Micro elliptical gear flowmeter can be used for micro flow.
When measuring the various gasification medium, should add the getter device.
(2) waist wheel flowmeter;
A clean gas or liquid, especially a lubricating oil, requiring accurate flow measurements.
The flow meter shall be installed horizontally, with a by-pass pipe and a filter at the inlet end.
(3) scraper flowmeter;
Continuously measuring the flow of liquid in closed conduits, especially the precise metering of various kinds of oil, can be carried out by using a scraper flowmeter.
The installation of the scraper flowmeter shall allow the fluid to be filled with the pipe and shall be installed horizontally so that the counter figures are in the vertical direction.
When the requirements of accurate measurement and measurement of various oil products, should add the getter device.
2. target flowmeter
The liquid flow measurement with a higher viscosity and a small amount of solid particles can be used when the measurement accuracy is not higher than 1.5 and the range ratio is no more than 3 to 1.
The target flowmeter is usually installed on a horizontal pipe. The length of the front straight pipe section is 15 to 40D, and the length of the back straight pipe section is 5D.
(five) selection of large diameter flow measuring instrument;
When the diameter is large, the pressure loss has a significant impact on energy consumption. The conventional flow meter is expensive. When the pressure loss is large, the flute type uniform velocity tube, the inserted vortex street, the inserted turbine, the electromagnetic flowmeter, the Venturi tube and the ultrasonic flowmeter can be chosen according to the situation.
1. flute pitot tube flowmeter
Clean gas, steam, viscosity less than 0.3Pa·, s of clean liquid flow measurement, when the pressure loss is small, you can choose the flute type pitot tube flow meter.
The flute type uniform speed pipe is installed on a horizontal pipe, and the length of the straight pipe section is not less than 6 to 24D upstream, and not less than 3 to 4D in the downstream.
2. insert type turbine flowmeter, plug-in vortex flowmeter, electromagnetic flowmeter, Venturi tube
See above
(six) the selection of new flow measuring instruments
1. ultrasonic flowmeter
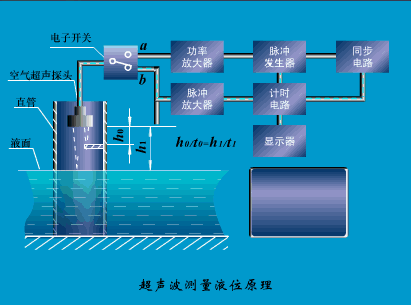
Wherever one can guideThe selection of ultrasonic flowmeter fluid can be sound, in addition to general medium, strong corrosive, non conducting, flammable, radioactive and other harsh working conditions of media, when not using contact measurement, using ultrasonic flowmeter.
2. mass flowmeter
The mass flow meter can be used when measuring the mass flow of liquid, high density gas and slurry directly and accurately.
Mass flow meters can provide accurate and reliable mass flow data without the effects of fluid temperature, pressure, density, or viscosity changes.
Mass flow meters can be installed in any direction without straight sections.
(seven) the selection of powder and lump solid flow measuring instruments
1. impulse flowmeter
The powder and bulk solids flow measurement of free fall, when the requirement of the closed transmission material, should choose the impulse type flowmeter; impulse meter is suitable for any size of various bulk materials, and can accurately measure the dust in many cases, but the bulk material weight shall not be greater than 5% of the weight of a predetermined punching plate.
The installation of the impulse type flowmeter requires that the material must be free to fall and must not exert any additional force on the object under test. The installation angle of the stamping plate, the angle and height between the feed port and the blanking plate have certain requirements, and it has certain relation with the range selection. The calculation should be done before selecting.
2. electronic belt weigher
Solid flow measurement for belt conveyors installed on a belt conveyor that conforms to standard performance. Its frame installation requirements strict, called the frame on the belt position and the distance from the material to the measurement accuracy have influence, should choose a good installation position.
3. track scale
The dynamic weighing scale should be selected for the continuous automatic weighing of railway freight cars.
This article source: chemical belated effort;

Official public micro signal