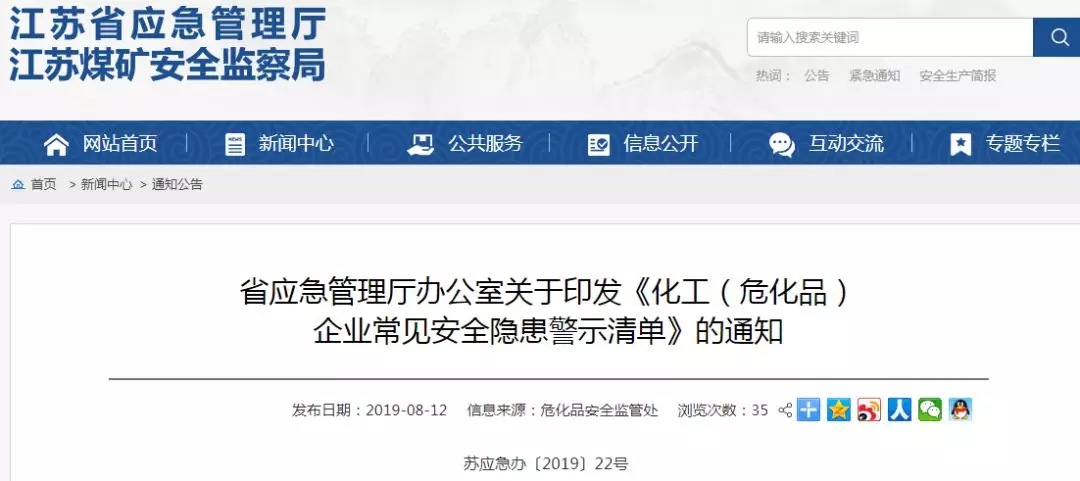
On August 12, the office of Jiangsu Emergency Management Office issued a circular on Issuing the Warning List of Common Safety Hidden Dangers in Chemical Industry (Dangerous Chemicals) Enterprises.
The notice pointed out that in order to further guide chemical (dangerous chemicals) enterprises to carry out the work of hidden danger investigation and management, enhance the operability of enterprise hidden danger investigation and management, promote enterprises to actively implement the main responsibility of safety production, effectively prevent and resolve safety risks, Jiangsu Provincial Department has carefully combed the in-depth inspection and guidance issued in the past two years. The potential safety hazards have formed the Warning List of Common Safety Hidden Hazardous Chemicals Enterprises (hereinafter referred to as the Warning List).
There are 244 items in the Warning List, including 86 unsafe behaviors of human beings, 102 unsafe states of objects and 56 management defects.
The notice pointed out that the "Warning List" is a frequent and repetitive problem that does not meet the safety production requirements in the daily work of the principal responsible persons, managers at all levels and front-line employees of chemical (hazardous chemicals) enterprises. It is a problem that chemical (hazardous chemicals) enterprises must prohibit or avoid in their daily safety production work. What happened is a supplement to the Guidance Table for the Deep Inspection of Safety Production of Hazardous Chemicals in Jiangsu Province.
Annex: Warning List of Common Safety Hidden Dangers in Chemical (Hazardous Chemicals) Enterprises
I. Insecurity of Human Beings (86 Articles)
(1) Labor Discipline (7 articles)
1. Drinking at work and in class after drinking.
2. Crossing, leaving and sleeping posts, and doing things unrelated to the post during the period of their posts.
3. Replacement or change of posts without permission.
4. Being late for work and leaving early, he fails to fulfill the formalities for taking leave as required.
5. Failure to dress and wear safety helmet as required to enter production and construction sites. Wear electrostatic clothing or nailed shoes into flammable, explosive devices or tank areas.
6. Smoking in non-smoking areas.
7. The principal person in charge has been out of his post for a long time without performing his duties.
(2) Technological Discipline (17 items)
8. Failure to conduct inspection tours as required, and failure to report and deal with the hidden dangers and problems found in time.
9. Failure to fill in operation records and succession records as required, and no signature of succession personnel.
10. The process alarms that appear are not handled and recorded in time.
11. Not operating in accordance with the operating procedures; unclear or unfamiliar with process control indicators and operating procedures.
12. Improvement of process or operation procedures without safety assessment.
13. Use compressed air to feed and press flammable and explosive materials.
14. Use atmospheric tank under pressure; Open reactor and vessel cover under pressure.
15. Process operation within the explosion limit of combustible gas.
16. When using nitrogen seal or transporting material, the nitrogen pipeline does not have check valve, so there is a risk of high pressure series and low pressure.
17. When separating flammable organic solvents by centrifuge, no nitrogen protection measures were taken.
18. When abnormal situations occur in the operation, they do not report in time and change the operation without authorization.
19. External personnel take the place of their own staff.
20. The blind board on site is not numbered and listed.
21. The sampling valve was not closed in time after sampling.
22. Operators leave the site when dangerous chemicals are loaded and unloaded and dewatered in tank area (cut water, cut alkali, etc.).
23. Unauthorized modification of relevant process parameters, alarm and interlocking parameters in DCS system and safety instrument system.
24. Before starting the belt conveyor, there was no check and confirmation and no warning bell.
(3) Other Disciplines (26 articles)
25. Scrub equipment, clothing, tools and ground with gasoline, volatile solvents in flammable and explosive areas.
26. Knock, impact and operate in flammable and explosive areas with spark-prone tools such as ferrous metals.
27. Use non-explosion-proof communication, lighting equipment and non-explosion-proof tools in flammable and explosive areas.
28. Unauthorized suspension of flammable, toxic, fire sound and light alarm system and safety interlocking system.
29. Close or adjust video surveillance facilities or shut down all kinds of alarm sounds without authorization.
30. Blocking fire passages and arbitrarily misappropriating or damaging fire fighting facilities.
31. Failure to inspect and maintain emergency protection facilities and equipment as required.
32. Can't use emergency protection equipment and equipment correctly and skillfully.
33. Do not wear special protective equipment to engage in hazardous operations in toxic, harmful, corrosive media and asphyxiating environment.
34. Carry out loading and unloading of dangerous chemicals vehicles (ships) without electrostatic grounding according to regulations.
35. The rotating equipment has not been shut down and the live equipment has not been shut down for maintenance.
36. Vehicles entering the production area are not equipped with fire retardants or vehicles entering the production area for speeding.
37. Managers command and force risky operations in violation of regulations.
38. No suitable and effective personal protective articles were provided for employees.
39. Safety signs such as prohibitions, warnings, instructions and prompts are not set or missing on site.
40. Do not participate in safety training and team safety activities without any reason.
41. Failure to participate in or organize safety inspections as required.
42. After the change of equipment and technology, the rules and regulations have not been revised in time.
43. Hazardous chemicals are not classified and stored according to the national standards, and dangerous chemicals are stored in excess and super-varieties, which are mixed with prohibited substances.
44. Hazardous chemicals are filled in excess of the approved loading capacity.
45. Before loading and unloading dangerous chemicals, the wheels are not fixed and the keys are not handed over to the post personnel for safekeeping.
46. Open storage of liquefied petroleum gas, liquid ammonia or liquid chlorine in solid bottles.
47. When goods are stored in hazardous chemicals warehouses, the top distance, lamp distance, wall distance, column distance and stacking distance & ldquo; five distance & rdquo; do not meet the requirements.
48. Employee & ldquo; Level 3 & rdquo; Safety education less than 72 hours.
49. Employees & ldquo; Level 3 & ldquo; Safety Education and Contractor Employees'Entry Safety Education Examination papers are not corrected or carefully corrected, and they are given marks at will.
50. Failure to participate in & ldquo; Level 3 & rdquo; SafetyEducational training or qualified without post skill training examination.
(4) Special assignments (36 items)
51. Special work permits such as fire and access to restricted space have not been processed in accordance with regulations.
52. Risk identification was not carried out before special operations such as fire, operation in restricted space, etc.
53. There are some missing items in the special work safety certificate, which exceed the prescribed validity period, the signer and approver do not meet the requirements, and the time for signing and approving the work permit is not filled in to minutes, so the work permit is examined and approved in advance.
54. Closing valves are used to isolate and isolate the working parts from the production system when igniting and entering the confined space. No isolation measures are taken to install blind plates or to disconnect a section of pipeline.
55. No fire safety analysis or analysis results are not qualified for operation.
56. Before entering the confined space, the concentration of combustible gas, oxygen and toxic gas were not analyzed.
57. Safety analysis was not conducted again after fire and interruption of operation in restricted space for more than one hour.
58. The sampling and analysis parts are not consistent with the fire operation parts, and the sampling and detection points are not representative.
59. No safety warning or hard isolation measures have been set up in the confined space.
60. When the same operation involves two or more types of fire, access to restricted space, blind block extraction, operation at high altitude, hoisting, temporary power consumption, soil movement and circuit breaking, the corresponding procedures for operation examination and approval are not handled simultaneously according to regulations.
61. Safety measures for fire and operation in restricted space are not confirmed or signed by the same person.
62. There is no special guardianship on the site of fire and operation in restricted space.
63. First-class and super-class fire operations fail to do “ one vote, one video ”.
64. The igniter has no valid special operation qualification certificate.
65. Handle or sign and approve the fire safety certificate for demotion.
66. Failure to do the work of ignition & ldquo; one point, one certificate and one person & rdquo; unauthorized change of scope of operation.
67. Fire, access to confined space and other special operations have not been completed for acceptance and signature.
68. Operators who fill in special work safety certificates such as fire, access to restricted space and so on are inconsistent with actual workers on site.
69. Oxygen and acetylene cylinders have no safety accessories such as shock rings and caps, and acetylene cylinders are not equipped with tempers. Oxygen, acetylene tracheal aging, chapped.
70. Lighting voltage in confined space is more than 36V, and operating voltage in humid container and narrow container is more than 12V.
71. There are no emergency evacuation facilities or measures for cleaning and overhauling in confined space.
72. When the autoclave is repaired, the power supply is not cut off and the warning sign of &ldquo is tied up; someone is repaired and the closing of &rdquo is forbidden.
73. Seatbelts are not fastened in operation at high altitudes, and the seatbelts are not fulfilled “ high hanging and low using ”.
74. Use scaffolding that has not passed the acceptance test, and the scaffolding is not tied firmly.
75. Throwing materials, tools and other debris at high altitudes.
76. Unauthorized demolition and alteration of scaffolding, steel grille, guardrail, cover plate, protective net and other protective facilities.
77. Use electrical equipment and electric tools that are not equipped with leakage protectors.
78. The power supply and electrical components of the corresponding explosion-proof grade are not used in fire and explosion dangerous places.
79. Use unqualified insulating tools and special protective devices for electrical operation and operation.
80. Temporary power distribution panels and boxes on site have no voltage and danger identification, no rainproof measures, and the pans, boxes and doors can not be firmly closed or unlocked.
81. Handheld and mobile electric appliances that exceed the safe voltage are not equipped with leakage protectors and power switches one by one to achieve “ one machine, one gate, one protection ”.
82. Lifting hook lacks anti-wire rope dropping device.
83. There are violations of & ldquo; ten non-hoisting & rdquo; in hoisting operations.
84. Pipeline, pipe rack, pole and electromechanical equipment are used as hoisting anchor points.
85. There is no safety warning sign or rope on the hoisting site, and no special guardianship.
86. There are defects or hidden dangers in construction and maintenance tools, and no inspection certificate is pasted.
2. Insecurity of objects (108 articles)
(1) Technology Major (27 items)
87. Temperature, pressure, liquid level and other over-control indicators.
88. The set process index, alarm value and interlocking value do not meet the requirements of process control.
89. The setting value of low liquid level alarm or interlocking for inner floating roof tank is lower than the height of floating plate support, which has the risk of falling bottom of floating plate.
90. Major hazards are not equipped with uninterrupted acquisition and monitoring system of temperature, pressure, liquid level, flow rate, composition and other information. They do not have the functions of information remote transmission, continuous record, accident warning, information storage and so on. Information is stored for less than one month.
91. Reaction equipment, storage tanks and other equipment do not set up on-site temperature, pressure and liquid level instructions as required.
92. Emergency cut-off facilities bypass did not take control measures, emergency cut-off facilities were not put into use or use bypass.
93. The same flammable liquid tank is not equipped with two different types of liquid level measuring instruments.
94. The equipment involved in the key supervision of dangerous chemical process has not realized automatic control, the system has not realized the function of emergency parking, and the automatic control system and emergency parking system of equipment have not been put into normal use.
95. Different process tail gas or materials are discharged into the same tail gas collection or treatment system without risk analysis.
96. If the exhaust gas recovery system of multiple chemical storage tanks is used, it is not qualified by safety certification.
97. Use the technology and equipment listed in the catalogue of backward safety technology and equipment.
98. Installations that may cause serious accidents such as fire and explosion are not equipped with over-temperature and over-pressure detection instruments, sound and light alarms, pressure relief facilities and safety interlocking devices.
99. Under abnormal conditions, the equipment or pipeline that may be overpressured is not equipped with reliable safety relief measures or unsatisfactory safety relief facilities.
100. Safety valve front of high concentration ethylene oxide equipmentNo blasting discs were set. The explosive disc inlet pipeline is not sealed with nitrogen, and the outlet pipeline of the safety valve is not filled with nitrogen.
101. Ammonia relief valve exhaust gas is discharged directly without safety treatment.
102. The capacity of the torch system can not meet the safety release of the device in the accident state. There is no long light, no reliable ignition system and fuel gas source, no reliable anti-tempering facilities, and the liquid separation and condensation of the torch gas do not meet the requirements.
103. There are no process cards in the operating room or the process cards have not been revised regularly.
104. Safety interlocking is not perfect or not in normal operation.
105. There is no approval procedure for removal interlocking and no safety measures were taken during removal.
106. Because of the overtemperature and overpressure caused by the explosion and decomposition of materials, there are no alarm signals and pressure relief and discharge facilities in the reaction equipment which may cause fire and explosion, and emergency cut-off feeding facilities with automatic or manual remote control.
107. Tanks with nitrogen protection facilities, nitrogen sealing system is not perfect or put into use, and there is no accident pressure relief equipment.
108. Propylene, propane, mixed C4, raffinate C4 and LPG spherical tanks and full-pressure LPG tanks are not equipped with leak-proof water injection measures, and water injection pressure and mode are not up to the requirements.
There are no independent emission systems or treatment systems for liquids, low calorific value combustible gases, combustible gases containing oxygen or halogen elements and their compounds, combustible gases with extreme and high toxicity, inert gases, acid gases and other corrosive gases.
110. The storage coefficients of liquefied hydrocarbons and liquid ammonia tanks exceed 0.9.
111. When producing or storing unstable olefins and dienes, no measures were taken to prevent the production of peroxides and autopolymers.
112. Flammable and explosive organic solvents and materials are transported through plastic pipes which are easy to generate static electricity.
113. Operating rules and emergency plans were not issued to the post.
(2) Equipment specialty (37 items)
114. Safety accessories such as safety valves and blasting discs are not normally put into use, and hand valves such as safety valves and blasting discs are not often opened and sealed with lead.
115. Safety accessories of pressure vessels and pressure pipes (including pressure gauges, thermometers, level gauges, safety valves and burst discs) are incomplete, intact, not checked on time and not in validity.
116. The body, foundation, fasteners, appearance and static grounding of pressure vessels and pressure pipes are not perfect.
117. The outlets of explosion relief devices and facilities are oriented to the positions easily accessible to personnel. The outlets of safety valves and blasting discs relating to flammable or toxic media are arranged indoors.
118. The height of exhaust cylinder and exhaust pipe directly discharged from combustible gas to the atmosphere does not meet the requirements of the code.
119. The safety valve outlets of flammable gas and liquid equipment are not connected to the appropriate facilities or systems.
120. Flammable gas compressor, liquefied hydrocarbon and flammable liquid pump are driven by belt.
121. There is no reliable safety device in the rotating part of the rotating equipment.
122. In the discharge ports and sampling ports of equipment and pipelines, measures such as blind plate, wire plug, pipe cap and double valves have not been taken.
123. Pump lubrication does not meet the requirements of & ldquo; Wuding & rdquo; & ldquo; tertiary Filtration & rdquo; Oil level line is not clear, oil cup is short of oil.
124. There are leakage phenomena in production facilities and storage facilities.
125. Leakage material collection devices and proper disposal of leaked materials are not set up in accordance with national standards.
126. No static electricity removing device is installed at the entrance of the key fire and explosion-proof work area.
127. Lightning and static grounding in tank area, production equipment and buildings do not meet the requirements. Lightning and static grounding are not regularly tested.
128. There is not enough safe passage and working space around electrical equipment and electrical lines, or stacking inflammable, explosive and corrosive articles.
129. Fire-retardant measures have not been taken for cables in dangerous areas of fire and explosion, and measures for preventing oil vapor channeling, corrosion and waterproofing of cable trenches have not been implemented.
130. The filling system of inflammable, explosive, toxic and harmful liquefied gases such as liquefied hydrocarbons, liquid ammonia and liquid chlorine is not used.
131. Distribution boxes and switches of combustible materials warehouse are set in warehouse.
132. Liquefied hydrocarbon, A-B and B-A liquid pipelines with closed valves and high media pressure due to external influences have not taken pressure relief safety measures.
133. There is no flexible connection between the inlet and outlet pipes of storage tanks. There are holes in the fire dike of the tank area.
134. Fixed bolts of explosion-proof electrical equipment and facilities are not all in place.
135. Floor slabs of multi-storey buildings or structures equipped with combustible liquids have not taken measures to prevent the leakage of combustible liquids to the lower floors.
136. No spark-free ground is used in the enclosed workshop which emits Class A gas, explosive dust or combustible fibers with specific air weight.
137. In places where explosive hazardous dust or combustible fibers are emitted, no measures have been taken to prevent dust, fibers from spreading, flying and accumulating.
138. The liquid warehouses of Class A, B and C are not equipped with facilities to prevent the liquid from dispersing, and the warehouses of articles which will burn and explode when wet do not take measures to prevent water immersion.
139. Safety evacuation doors of operation room, control room, workshop, warehouse and other buildings are not opened outward.
140. No protective measures have been taken on the high temperature surface of equipment and pipeline.
141. Pipeline material and flow direction, marking is not clear.
142. Equipment, containers, etc. are not effectively fixed and float directly on the ground.
143. The belt conveyor has no emergency rope-pulling stopping facilities.
144. Cables or steel pipes in electrical lines are not sealed with non-combustible materials when they pass through holes in walls or floor slabs.
145. Containers containing armor and Class B liquids are not provided with sunscreen cooling facilities when they are placed outdoors.
146. Platforms, guardrails and staircases such as operation and patrol inspection are defective or corroded seriously.
147. Chemical plant does not set up double power supply according to national standards.
148. Explosion-proof electrical equipment is not installed and used in explosion dangerous places according to national standards.
149. Electrical equipmentThe safety measures against leakage and electric shock have not been implemented, and the laying of grounding wires is not standardized.
150. The measures to prevent small animals from entering the distribution room have not been implemented.
(3) Instrument specialty (23 items)
151. The leak detection and alarm device is not installed in flammable and toxic gas leakage sites according to national standards.
152. The distribution map of detection points for flammable and toxic gas detectors has not been compiled.
153. The flammable and poisonous gas alarm has not been calibrated and verified in accordance with the prescribed period.
154. Errors in setting the alarm values of the first and second levels of flammable and toxic gas detection and alarm instruments.
155. Flammable and toxic gas detection and alarm devices do not have in-situ sound and light alarm function.
156. Fixed flammable and toxic gas detection and alarm instrument detection and alarm signals were not sent to the control room and field operation room where the operators were resident.
157. There is no UPS power supply in the flammable gas and toxic gas alarm system.
158. The explosion-proof grade of instrument and instrument circuit in explosion dangerous place does not meet the requirement of explosion-proof in area.
159. Measures for preventing small animals, static electricity, dust and waterproofing of cables import and export are not implemented.
160. The labels of interlocking system equipment, switches and terminal rows are incomplete, accurate and clear.
161. Emergency stop button has no anti-collision protection measures.
162. The sensor probe of flammable gas detection alarm and toxic gas alarm is not perfect; the sound and light alarm is not normal, and the fault alarm is not perfect.
163. There is no interlocking sign warning sign for the field detection and execution components of the safety instrument system.
164. Instrument system maintenance, anti-freezing, anti-coagulation, waterproof measures are not implemented, instrument is not perfect.
165. There is no obvious warning sign on the site of radioactive instrument.
166. Hazardous chemicals tank farms involving toxic gases, liquefied gases and highly toxic liquids are not equipped with independent safety instrumentation systems and are not put into normal use.
167. Emergency shutoff valve is non-fault-safe type.
168. Hazardous chemicals tank farm which constitutes primary and secondary major hazards has not realized emergency shut-off function or emergency shut-off facilities have not been put into operation.
169. There is no uninterruptible power supply in automatic control and safety instrument system.
170. There are no upper and lower limit alarm devices and automatic interlocking cut-off devices for inlet and outlet pipelines in the gas holder.
171. No level gauge, pressure gauge and safety valve are installed in full pressure liquid ammonia tank, and no temperature indicator is installed in cryogenic liquid ammonia tank.
172. When there is no buffer tank in the station, no easy-to-operate emergency shut-off valve is installed on the loading and unloading pipeline 10 meters away from the crane position of the truck loading and unloading.
173. On-site pressure gauges, thermometers, liquid level meters, etc. are not marked with upper and lower limits. The glass tube level gauge has no protective measures.
(4) Design major (15 items)
174. The distance between overhead power lines and production areas in the area does not meet the requirements of national standards.
175. involving phosgene, chlorine and hydrogen sulfide gas pipelines passing through public areas other than plant areas (including chemical and industrial parks).
176. Class A and B fire hazard devices are equipped with offices, operating rooms, fixed operating posts or lounges.
177. Class A and B warehouses are adjacent to offices and lounges, or there are offices and lounges in the warehouses.
178. Storage tanks of different fire hazard categories are located in the same tank group, and atmospheric and pressure storage tanks are arranged in the same tank group.
179. The side of the control room or cabinet facing the device with fire and explosion danger does not meet the requirements of national standards on fire and explosion prevention.
180. The external safety protection distance of production equipment and storage facilities does not meet the requirements of national standards.
181. The fire protection spacing of the general layout of production and storage facilities in enterprises does not meet the requirements of the specifications.
182. Fire-proof spacing between enterprise facilities and adjacent factories or facilities does not meet the specifications.
183. The gas holder is not located on the upper wind side of the minimum frequency wind direction of the year in the places where people are concentrated, open fires or sparks are emitted.
184. Workshops and warehouses that produce, operate, store and use dangerous goods are in the same building as staff dormitories, and the safe distance between them does not meet the requirements.
185. Adding equipment, facilities and structures at will without formal design or implementation of change procedures.
186. Failure to adopt fire-resistant protection measures for load-bearing steel structures as required by the code.
187. No positive pressure ventilation was used in the on-line analysis instruments when the equipment in the explosion dangerous area was non-explosion-proof.
188. The special pump area of tank group is not arranged outside the fire dike.
3. Management Defects (58 Articles)
(1) Legitimacy and Compliance (Article 19)
189. Hazardous chemicals production enterprises have not obtained safety production licenses. If the safety production license exceeds its validity period, the scope of the license is not consistent with the current situation of the enterprise.
190. Hazardous Chemicals Registration Certificate has not been obtained, and the registration content is inconsistent with the current situation of enterprises.
191. Failure to organize the completion and acceptance of safety facilities for hazardous chemicals construction projects as required.
192. Safety evaluation is not carried out every three years by evaluation units that meet the qualifications prescribed by the State.
193. Major hazard sources of hazardous chemicals have not been assessed, documented and filed as required.
194. The cost of production safety has not been withdrawn and used in accordance with the provisions of the State.
195. The emergency rescue plan has not been reported to the emergency management department for the record.
196. Precursor chemicals have not obtained legal qualifications or certificates for filing.
197. The principal person in charge and the safety management personnel have not been trained and qualified according to law.
198. The number of full-time safety production managers does not meet the requirements because the safety production management organizations have not been set up in accordance with the regulations.
199. No registered safety engineer or safety director is assigned to work in safety management.
200. Construction projects (including long-distance pipelines) for the production and storage of hazardous chemicals have not passed safety review.
201. The use certificate of the used or newly added pressure vessel has not been obtained within the prescribed time limit.
Two hundred and twoSpecial operators such as hazardous chemicals safety operations are not on duty with certificates.
203. Boiler, pressure vessel operator, motor vehicle driver, electrician, electric welding and other operators have not obtained special operation qualification certificate.
204. The driver's license, dangerous goods permit and dangerous goods escort certificate of vehicles transporting dangerous chemicals are invalid.
205. Hazardous chemicals safety technical instructions have not been compiled in accordance with the regulations, and safety labels conforming to chemicals have not been pasted or hung on the packaging.
206. Emergency plans for production safety accidents have not been prepared according to the requirements of the guidelines.
208. No risk assessment and change procedures have been performed for process and equipment changes.
208. The principal person in charge of a chemical enterprise does not have more than three years'experience in the chemical industry and does not have a college degree or higher.
(2) Systems and regulations (16 articles)
209. No operating procedures and process indicators have been established.
210. The compilation and content of operation rules do not meet the requirements of the Guidelines for the Implementation of Process Safety Management in Chemical Enterprises.
211. No start-up and shutdown plan has been worked out.
212. No expert review has been organized for the trial production plan, and no inspection and confirmation of safety production conditions has been organized before the trial production.
213. No equipment management system has been established, such as equipment maintenance, inspection tour, anti-corrosion and heat preservation, equipment lubrication, etc.
214. No safety management system for instrument automation control system and safety instrument system has been established.
215. No job-matching responsibility system for safety production has been established, and the responsibility system for safety production of the principal person in charge does not meet the requirements of statutory responsibilities.
216. No hidden danger investigation and management system has been established.
217. No special operation management system has been formulated, such as fire fighting and access to restricted space.
218. No safety management system for major hazardous sources of hazardous chemicals has been established.
219. No change management system has been formulated and implemented.
220. No accident (attempted accident) management system has been established.
221. No contractor safety management system has been formulated and implemented.
222. No ldquo has been established for highly toxic chemicals and explosive-prone chemicals; double acceptance, double custody, double delivery, double locks, double principal accounts & rdquo; etc. & ldquo; five pairs & rdquo; system.
223. No system of leading cadres on duty has been established.
224. The system and regulations are unrealistic and not operable.
(3) Risk assessment and hidden danger management (8 items)
225. Hazardous and harmful factors identification and risk assessment have not been carried out regularly for operation activities and equipment and facilities. Risk inventory has not been established and risk classification management has not been implemented.
226. The principal person in charge does not carry out risk assessment and commitment announcement every day.
227. Hazard and operability analysis (HAZOP) was not carried out as required. The countermeasures and suggestions put forward by HAZOP analysis were not implemented.
228. The safety instrumentation system has not been assessed at the safety integrity level, and the proposed measures have not been implemented.
229. Fine chemical enterprises did not carry out the risk assessment of reaction safety according to the requirements of normative documents.
230. The newly developed production process of dangerous chemicals has not been directly industrialized without pilot, pilot and industrial tests; the first chemical process used in China has not been proved to be safe and reliable in accordance with the regulations.
231. Technological sources are unreliable, and there is no conforming technology transfer contract or safety and reliability demonstration.
232. The hidden danger rectification has not been implemented & ldquo; Wuding & rdquo; and the requirement of closed-loop management has not been fulfilled.
(4) Planning and Taiwanese Accounts (12 items)
233. No annual safety education and training plan has been formulated and implemented.
234. No annual emergency plan exercise plan has been formulated and implemented.
235. No annual equipment maintenance plan has been formulated.
236. No annual inspection plan for pressure vessels and pipelines has been formulated.
237. No safety education and training files have been established.
238. No team safety record was established.
239. Pressure vessel, pressure pipeline account and technical files have not been established.
240. No record of safety accessory ledger and blasting disc replacement has been established.
241. No instrument automation control system or safety instrument system related to safety interlocking management account has been established.
242. Hazardous Chemicals Warehouse has not set up an entry and exit register account, which is inconsistent with the accounts.
243. No safety production management agreement has been signed with the contractor.
244. Contractor safety management files and annual evaluation records have not been established.