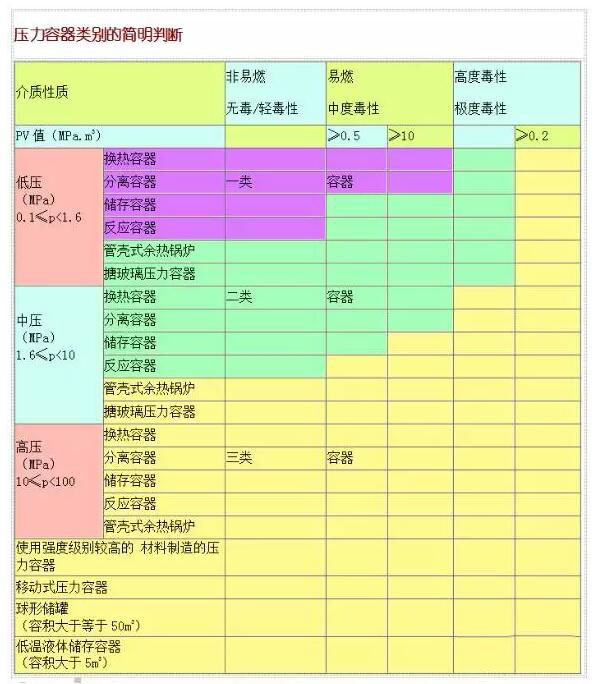
1, pressure vessel in the selection of materials should be considered when the performance?
The selection of pressure vessels should consider the mechanical properties, chemical properties, physical properties and technological properties of the materials.
2, pressure vessel compression element with steel, should adopt what kind of steel?
Steel for pressure vessels, which should be used as a killed steel in oxygen converter or electric furnace. The standard tensile strength limit value is greater than or equal to 540MPa or low alloy steel and &mdash austenite; ferrite stainless steel plate, as well as for the design of temperature is lower than the -20 low temperature steel and low temperature steel forgings, outside the furnace scouring process should also be.
3, pressure vessels with the application of cast iron material restrictions?
Iron shall not be used for containing utmost and high or medium pressure and poisoning hazards, the design is greater than or equal to the explosive medium pressure vessel pressure element 0.15MPa, and shall not be used for pressure parts of tubular waste heat boiler.
4, the general design of pressure vessel, shall at least indicate what content?

(1) the name, category, design and manufacture of the pressure vessel;
(2) working conditions, including work pressure, working temperature, medium toxicity and the degree of explosion hazards, etc.;
(3) the design conditions, including design temperature, design load (all load should be considered including stress), medium (component), corrosion allowance, welding coefficient and natural conditions, the liquefied gas storage tank shall indicate the loading coefficient, to define the content storing container is stress corrosion the corrosive medium shall be indicated;
(4) material grades and standards for major compression components;
(5) the main characteristic parameters (such as the volume of the pressure vessel, the heat exchange area and the number of the heat exchanger, etc.);
(6) design and service life of the pressure vessel (the number of cycles of the surface of the fatigue vessel);
(7) special manufacturing requirements;
(8) heat treatment requirements;
(9) non destructive testing requirements;
(10) pressure test and leak test requirements;
(11) requirements for the prevention of corrosion;
(12) the specifications and special requirements of the safety accessories (except for the technical coefficient);
(13) the location of pressure vessel plate;
(14) packing, transportation, site assembly welding and installation requirements.
5. What are the requirements of the opening position of the pressure vessel inspection hole?
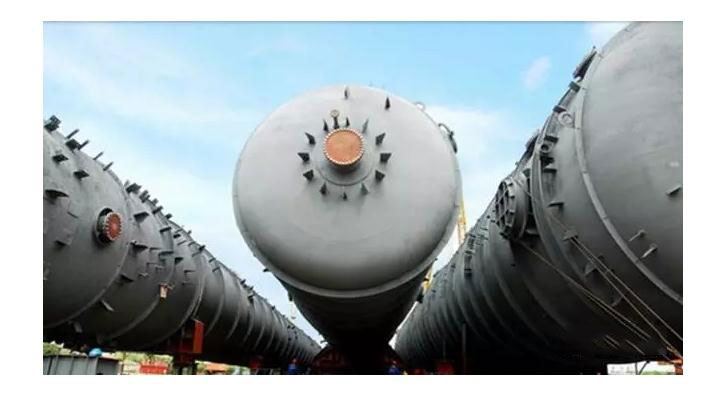
(1) the opening of the inspection holes shall be reasonable and appropriate to facilitate the observation and cleaning of the interior;
(2) the hand hole should be opened on the head or in the vicinity of the cylinder head.
6, what pressure vessels can not open inspection holes?
Meet one of the following conditions:
(1) a pressure vessel with an inner diameter of less than or equal to 300mm;
(2) the pressure vessel is provided with a detachable head cover, a cover plate, etc., or other can switch the cover, the size of the head cover, the cover plate or the cover is not smaller than the size of the check hole;
(3) no corrosion or slight corrosion, no internal inspection and cleaning of the pressure vessel;
Pressure vessel for (4) refrigerating device.
7, pressure vessel with the liquid level gauge should meet what requirements?
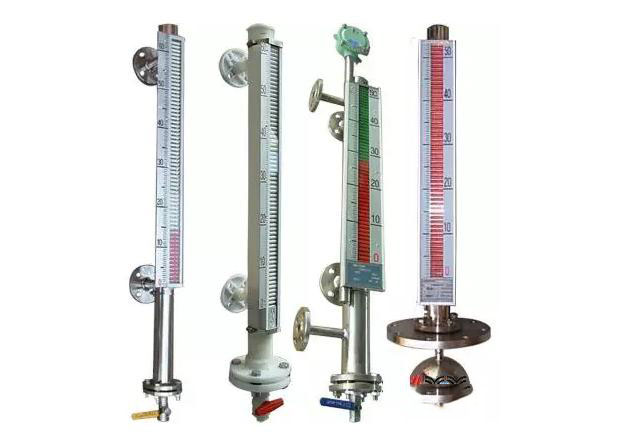
The level gauge used for pressure vessels shall be in accordance with the relevant standards and shall meet the following requirements:
(1) according to the pressure vessel ring, the maximum working pressure and temperature of the correct choice.
(2) in the installation of the use of low, medium pressure vessels with the liquid level gauge, should be 1.5 times the nominal pressure gauge of the hydraulic test; high pressure vessels of the liquid level gauge should be carried out 1.25 times the nominal pressure gauge test.
(3) the pressure vessel containing the medium below 0 degrees C shall be used for the selection of anti frost level gauge.
(4) the cold area outdoor use liquid level meter, liquid level should be selected with jacket or thermal insulation structure design.
(5) for flammable, toxic degree of extreme, highly hazardous medium liquefied gas pressure vessel, should prevent leakage protection device.
(6) requirements indicating liquid level gauge smooth, should not use the float type liquid level gauge (standard).
(7) mobile pressure vessels shall not be allowed to use glass plate level gauge.
8, the pressure vessel cylinder plate welding groove form mainly has several?
The pressure vessel cylinder plate welding groove mainly in the form of single V groove, double V groove, single U groove, double U groove, X groove five.
9, pressure vessel welding defects are mainly several?
There are seven kinds of defects, such as gas hole, slag inclusion, crack, undercut, incomplete fusion, wrong side edge, deformation and so on.
10, some of the container plate why preheating?
Container plate welding to be pre heating is due to the choice of material properties of the container, is to reduce the welding crack, residual stress and other welding defects.
11, why can not change the use of pressure vessels?
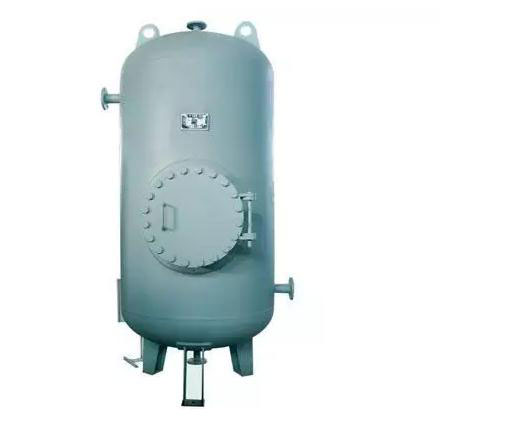
The pressure vessel is designed and manufactured, the equipment used in strict accordance with the national laws and regulations, the change of use is not allowed in general, once the change of use will be operating temperature, pressure, medium is equal to the change may cause accidents. After the declaration, the local quality and Technical Supervision approved, the party can transform it with.
12, the container is not more than 80mm, can not be detected in one side welding, how to deal with?
Cylinder and head of vessel diameter does not exceed 800 of the last ring closure weld, when using single welded butt joint without plate, and unable to carry out X-ray or ultrasonic testing, does not allow for testing, but requires the use of gas protection welding.
13, what is the pressure test?
Hydraulic pressure test. Gas-liquid combination test.
14, hydraulic test, what is the requirements of the experimental liquid?
The test liquid with water, can also be used to other liquids will not lead to the occurrence of danger; test the temperature of the liquid should be below the flash point or boiling point.
Austenitic stainless steel container water for hydraulic test should be removed after the water stains clean, when unable to meet this requirement, should control the chloride ion content of water does not exceed 25mg/L.
Carbon steel Q345R steel liquid containerPressure test, the liquid temperature shall not be less than 5 degrees Celsius, other low alloy steel shall not be less than 15 degrees, if the thickness of the material caused by other factors such as temperature increases without ductility. It is necessary to raise the temperature of the test liquid.
15, hydraulic test eligibility criteria?

No leakage; no visible distortion; no abnormal sound during the test.
16. What kind of conditions can be carried out for the pressure test?
The volume is too large, can not bear the weight of the water; complex structure, hydraulic pressure test is not sufficient to test the various parts of the pressure test requirements; due to the structure design, the water is not suitable for the (such as not to test residual liquid container); the other is difficult to overcome the difficulties, such as the large container water supply difficulties.
17, air pressure test and gas-liquid combination pressure test of qualified standards?
(1) in the process of pressure test, pressure vessel without abnormal noise, after liquid soap or other liquid leak check no leakage, no visible deformation is qualified;
(2) for gas-liquid combination pressure test, the outer wall of the container should be kept dry, after inspection without liquid leakage, with liquid soap or other liquid leak check no leakage, no abnormal noise, no visible deformation.
18. What is the purpose of the pressure vessel to carry out the pressure test?
The overall strength, stiffness and stability test of container inspection; compactness of welded joints; sealing performance verification of sealing structure; to eliminate or reduce the peak value of residual stress, local discontinuous zone stress; closed effect on micro crack, crack tip passivation.
19, what is the leak test? When to carry out?
Air tightness test and ammonia leak test, halogen test and ammonia leak test etc..
The degree of toxicity of the medium is extreme, highly hazardous or not allowed to have a trace of leakage of the container, the pressure test should be qualified after the leak test.
20, what kind of situation to do air tightness test? How to carry out?
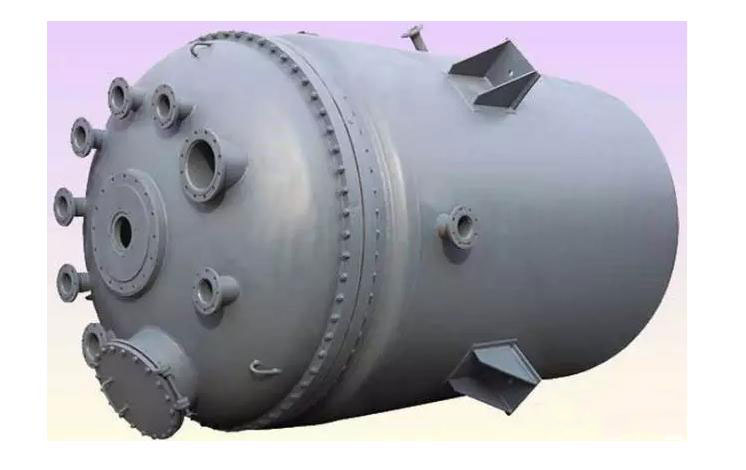
(1) the toxicity of the medium is extreme, highly hazardous or not allowed to have a trace of leakage of the container, the pressure test should be qualified after the leak test.
(2) air tightness test shall be carried out after the hydraulic test is qualified. On the design requirements of the pressure test of the pressure vessel, whether it is required to do air tightness test, should be specified in the design pattern.
(3) of carbon steel and low alloy steel pressure vessel, the test gas temperature not lower than 5 DEG C.
(4) when the pressure vessel carries out the gas tightness test, the safety accessories shall be fully equipped.
(5) the gas used in the gas tight test shall be dry, clean air, nitrogen or other inert gases.
(6) the pressure of the air tightness test should be indicated on the drawing.
(7) the test pressure should be increased slowly, reaching the required test pressure for 30 minutes after the pressure. Leakage inspection of all welds and connection parts, small containers can also be immersed in water inspection. If there is a leak. Hydraulic test and air tightness test after repair. No leakage after inspection is qualified.
21, common head type? The advantages and disadvantages of various head?

Convex head (elliptical head, butterfly head, spherical head and hemispherical head, flat head, cone head).
(1) from the force of the situation, followed by: hemispherical, oval, saucer shaped, conical, flat cover the worst;
(2) from the manufacture, the flat cover is easiest to make, and the second is the cone, the shape, the ellipse, the shape of the hemisphere;
(3) although the force effect is not good, it is good for the discharge of the fluid.
22, the inner pressure cylinder and spherical shell thickness in the calculation of the coefficient of the weld joint coefficient refers to the weld joint coefficient?
The coefficient of the welding seam in the cylinder formula is the weld coefficient of the longitudinal weld (i.e., a kind of weld). The weld coefficient of spherical shell is the minimum weld coefficient of each weld on the spherical shell, which includes the weld coefficient of the spherical shell connected with the cylinder.
23, what are the two types of external pressure vessel damage? What are the two aspects of the design of the external pressure vessel?
External pressure vessel damage mainly due to insufficient strength caused by damage and lack of stability caused by the failure of the two kinds of failure; design should include strength calculation and stability check.
Due to instability often occurs before the strength failure, the stability calculation is the main consideration in the design of the external pressure vessel.
24, pressure vessel failure form?
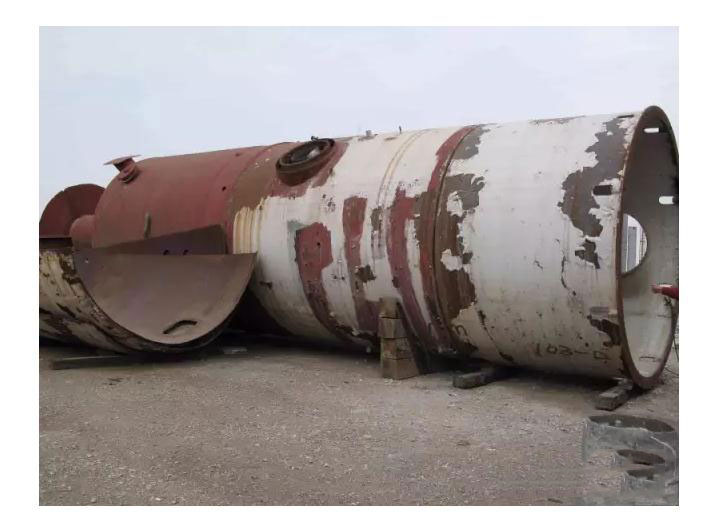
Pressure vessel is lost due to mechanical load or temperature load is too high and the ability to work properly, known as failure. Form include:
(1) strength failure: caused by the failure of the material to yield or fracture;
(2) the failure of the stiffness: the container has a large elastic deformation, resulting in transport installation difficulties or loss of working capacity;
(3) stability failure: the shape of a sudden change in the shape of the load resulting in loss of ability to work;
(4) leakage failure.
25. What is the main difference between the conventional design method of pressure vessel and the method of analysis and design?
(1) the conventional design method is to calculate the maximum stress of the element with a thin film stress based on the elastic failure criterion, and to calculate the maximum stress of the element.
In the container, the large edge stress and other local stresses are embodied in the form of enhancement coefficient, and the maximum profit of the gauge and the local stress is the same as the strength of the film.
(2) analysis design method: the plastic failure and elastic failure criterion as the basis, and various container stress, accurate calculation, and the stress classification, different forms of damage according to different stresses, respectively the strength of different conditions, in order to calculate the thickness of the element.
26, how to divide the thin walled vessel and the thick walled vessel?

In accordance with the thickness of T and the radius of curvature of the ratio of R, general MAX&le (t/R); 0.1 is called the thin shell, and thick shell. For cylindrical shell with the diameter of the outer diameter of the wallpaper MAX&le (Do/Di) K=; 1.1~1.2, it is called the thin wall cylinder.
27, the inner pressure of the cylinder and spherical shell, the difference between the film stress?
(1) the same: two to the film stress, and everywhere.(2) different: two times of the axial stress of the cylinder in the cylinder to the film. The two direction film in the spherical shell is equal to the film, and its value is equal to the axial stress in the equal diameter cylinder. For this purpose, the wall thickness of the spherical shell is only half of the diameter of the cylinder.
28, edge stress characteristics?
(1) the local — — the stress in the edge to the bending stress mainly, but its scope of action is not, in the direction of the direction, from the edge of the rapid decline.
(2) self limiting — — edge stress is due to satisfy the deformation of adjacent elements, when the stress reaches the yield point of the material, the material plastic deformation, the deformation coordination are met.
Once the deformation is met, the plastic flow of the material is automatically suspended. For this reason, the stress and deformation can be automatically restricted.
29, oval head and butterfly shape of the limelight why with straight?
To avoid the connection between the head and the cylinder and the overlap of the edge stress zone.
30, what is the stability of the container and the critical pressure? What are the characteristics?
The container under the effect of compressive stress, failure shape change suddenly caused the collapse into loss of the stability, the wall stress stress from the original film state of mutation bending stress minimum outer container is deflated when the compressive stress is called the critical pressure.
As long as there is compressive stress in the thin wall vessel, it is possible to lose stability. The internal pressure of the standard ellipsoidal head, due to the existence of the transition region around the film compression stress, it is also a stability problem, so it will be the minimum thickness to be restricted.
31, what types of instability? What is its characteristic?

Circumferential instability and meridional instability.
The circumferential instability is caused by the stress of the circumferential compression film of the vessel, and the buckling is caused by the axial compressive stress of the vessel.
Container circumferential instability, the cross section from round to waveform, meridional instability, the cross section is circular, the longitude changes from a straight line to the wavy line.
32, what is the elastic instability and non elastic instability? Can the high strength steel be used to replace the low strength and rigidity to improve the elastic stability of the container?
Instability of film wall compressive stress is less than the proportional limit of the material, the stress and strain in accordance with Hooke's law, known as the elastic instability, because the critical buckling pressure and the yield limit of material not only with elastic modulus and Poisson ratio, elastic modulus and Poisson number and various steel ratio difference not so with high strength steel instead of low strength and stiffness is invalid.
If the proportional limit instability of compression wall stress is greater than the material, stress and strain is very linear, called non elastic instability, critical pressure and non elastic instability when the yield limit, available at the time of high strength steel instead of low strength steel.
33. How to design the outer pressure spherical shell?
Elliptical head under internal pressure is “ chemotaxisround phenomenon ” in &ldquo, the external pressure under the action of &rdquo, flat phenomenon; trend; produce circumferential tensile film stress transition zone and the head, there is no instability problems, but in the “ the spherical part of ” there is compression of thin film stress and as the external pressure shell, so they need to shell stability calculation. In the case of elliptical head, the &ldquo is required to be calculated; the spherical part ” the equivalent spherical shell radius. Thirty-four
34. How to consider the thermal stress under internal pressure? Elimination of thermal stress measures?
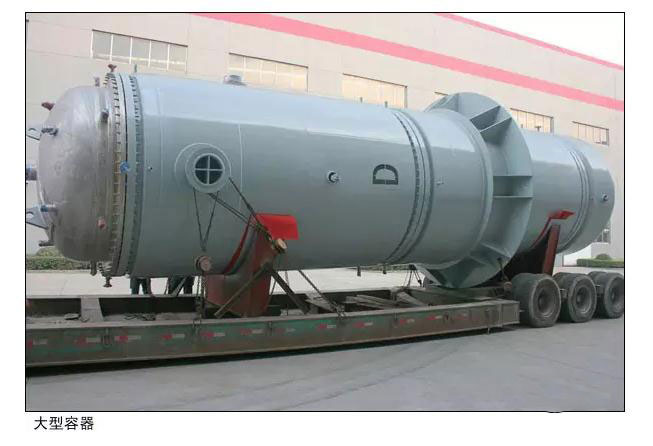
(1) internal pressure heating: the inner wall stress decreases, and the outer wall stress increases, the stress state is likely to deteriorate. When the delta t≤ 1.1P, can not consider the influence of thermal stress.
(2) internal pressure external heating: the inner wall of the comprehensive stress increases, and the outer wall stress decreases, stress state deterioration. Temperature stress must be taken into account.
Measures to eliminate thermal stress:
(1) the heating and cooling rate of the control equipment;
(2) controlling and reducing the thermal deformation of the component;
(3) set expansion joints;
(4) using a good thermal insulation layer.
35, equal area method and the difference between the pressure area method?
Equal area method is based on the compensation of the stress area of the film, which has nothing to do with the force balance. The pressure area method is based on the force balance at the opening of the hole (under the stress of the film). Generally speaking, the larger size of the pressure area method is needed in the open hole.
36, bolt flange connection design including what content?
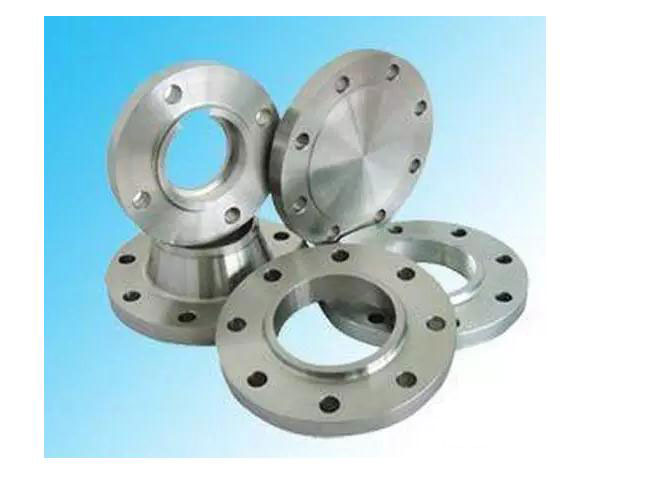
Determine the gasket material, form size; determine the bolt material, the number of specifications; determine the flange materials, sealing surface form and structure size; stress check (all dimensions are not included in the calculation of the amount of corrosion allowance).
37, what is the narrow face flange? What is the wide face flange?
The contact surface of the gasket is located in the range of the flange bolt hole, and the contact surface of the gasket is distributed on the inner and outer sides of the center of the bolt.
38, according to the overall level of the flange is divided into several forms? What are the characteristics?
Loose flange: flange failed to effectively and the container or take over as a whole. The calculation of the container or take over not to bear the flange and the flange torque.
The integral flange: flange, flange neck, and the container or take over the three can effectively connect into a whole structure, joint commitment to the role of flange torque.
Any type of flange: it is a number of welding flanges, which are calculated by the integral flange.
39, the strength of the strength of the flange check when the need to check?
Axial stress, circumferential stress, radial stress, combined stress, shear stress.
40, reasonable design of flange connection, what is the requirement of the gasket load?
In order to bear the flange as small as possible, in the design of the gasket should be controlled as much as possible to control the small gasket load.
For this requirement, the Wa is close to the bolt load determined by the Fp of the Wp of the bolt load as determined by the gasket at the time of operation, when the load Fa is determined by the compression load at the time of operation.
41, reasonable design of flange connection, to determine the diameter of the center of the bolt circle determine what?
In order to bear the flange torque as small as possible, in the design of the bolt as far as possible to control the small diameter of the center of the bolt.Flange radial structure requires that the center circle diameter of the bolt as determined by the flange is close to the center circle diameter of the bolt as determined by the flange ring structure.
42, flange design, in order to obtain the result of the design of the compact flange, the flange of the stress have any requirements?
The three stresses of the flange should be close to the corresponding allowable stress, so that the stress state of the flange should be full, then the strength properties of the material can be fully played.
43, increase the flange cone neck thickness on the flange of the stress is what effect?
Increase the flange cone neck size, the cone neck rotation stiffness increase, while the increase of the proportion of cervical cone bearing, the cone neck and flange of the boundary between the boundary force and torque increases, i.e. the cone neck end boundary force, torque increases, it will cause the axial bending stress.
But because of the cross section of the cone neck and the thickness of the cone, the relationship between the thickness of the cone and the cone is greatly increased, and the stress of the cone neck is reduced.
The boundary force increases, increasing the radial bending moment acting on the inner edge of the flange, which leads to a radial flange ring bending stress increase. The increase of radial bending moment on the inner flange, the flange ring support is increased, so the ring deflection decreases, to reduce stress.
44, overpressure relief devices include a few, what are the advantages and disadvantages, for what kind of pressure vessel does not apply?
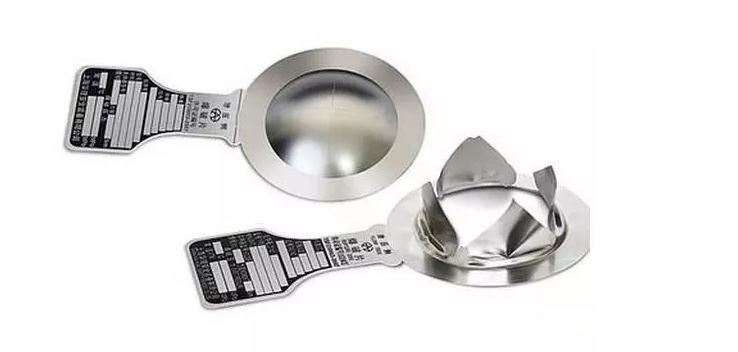
There are three kinds: safety valve, bursting disc device, safety method and combination of bursting disc device.
(1) a safety valve is opened by inlet static pressure automatic pressure relief valve, he relies on the media itself to discharge the fluid pressure to prevent internal pressure exceeds the safety value, when the internal pressure returned to normal, the valve automatically closes to prevent the media continue to discharge.
(2) the bursting disc is a kind of non heavy closed type pressure relief device, which is made by imported static pressure to press the bursting disc to release the release medium, in order to prevent the internal pressure from exceeding the predetermined value. After the pressure is restored, the new bursting disc must be re installed.
All the following conditions must be used blasting piece device:
(1) the medium in the container will result in the failure of the safety valve; no material leakage of the container; the pressure in the container is growing too fast, so that the safety valve can not be adapted; the safety valve can not adapt to the other conditions.
(2) for the medium in the operation process may produce a pressure surge, the reaction rate of detonation pressure vessel does not apply to these overpressure discharge device.
45, low temperature pressure vessel weld detection has any special requirements?
Where the provisions do 100% inspection of the container, its T joint, butt weld, fillet weld, are required to do 100% magnetic powder or penetration testing, and the compression component welding of non compression components of the welding seam also according to the requirements of this section.
46, what is called low temperature and low stress conditions, low temperature stress conditions of the container is the low pressure vessel to consider?
Under low temperature stress conditions, the design temperature of the container or its compression element is lower than or equal to -20 C, but its circumferential stress is less than or equal to the standard room temperature yield strength of steel, and is not more than 50MPa.
When the container or the compression element used in the “ low temperature stress conditions ” if the design temperature increased by 50 degrees Celsius, higher than -20 degrees Celsius, do not have to follow the provisions of low temperature pressure vessel.
47. What are the mechanical properties of welded joints of welded joints?
Tensile, bending, impact test.
48, pressure vessel and its components in what circumstances should be pickling and passivation treatment?
(1) the surface of austenitic stainless steel and composite steel plate with corrosion protection requirements should be treated by pickling and passivation.
(2) the requirements for corrosion protection of austenitic stainless steel parts in accordance with the requirements of the heat treatment, the need to do pickling passivation.
Process equipment network finishing release, reproduced please indicate the source.