One, delayed coking process, coke tower and hydraulic coke removal equipment
The production technology of delayed coking unit is divided into two parts, coking and coke removal, coking is continuous operation, and the other is the gap operation. Because the industrial device generally has two or four coke tower, so the entire production process is still continuous operation.
1, coke tower
(1) the structure of the coke tower
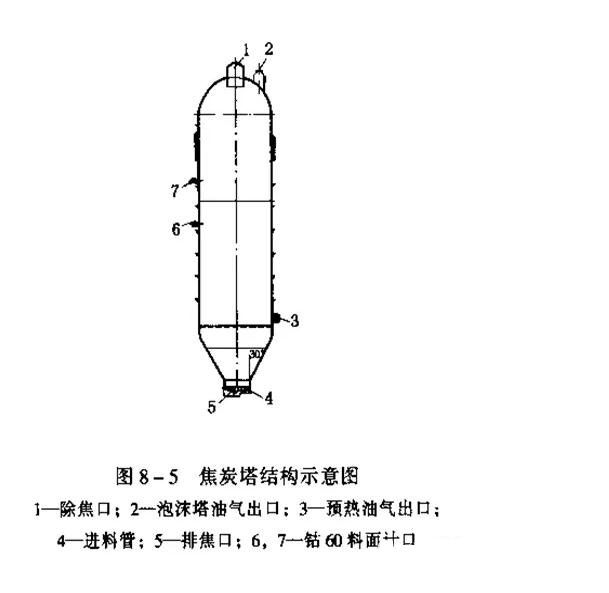
The coke tower is a hollow cylinder made of thick boiler steel plate, which is a place for coking reaction. General coke tower height of 30 meters in the following is appropriate. Too high to operate, easy to produce vibration or damage to the tower wall, and a waste of steel.
The top of the tower with coke export, oil and gas exports; the side of the tower with level indicator, delayed coking chemical reaction is mainly generated by coke in the coking tower are accumulated in the tower. With the continuous introduction of oil, coke layer gradually increased; in order to prevent the foam layer out of top oil and gas pipelines caused by coking and fractionating tower, at different height positions of the coke tower is a high level monitoring of coke. The bottom of the tower is a cone, and the bottom end of the cone is a coke discharging port, and the bottom of the tower is opened when the normal production is closed by a flange cover.
(2) attention to the operation of the coke tower
Exchange tower:
1) to change the conditions in front of the tower tower, notice: dispatch duty, monitor, operator site to confirm the feed cut off valve, the main oil gas isolation valves are open, spare valve, oil valve is closed, the bottom cover, feeding unit, oil gas line leakage.
2) trade process, pay attention to the new indoor furnace outlet pressure, Tata bottom and top pressure changes, such as abnormal, timely cut back to the old tower, the new tower small steam blowing, then find out the reason to the new tower.
Small steam blowing: blowing steam must pay attention to the bottom pressure, through the tower bottom pressure to determine whether the gas blowing through the coking (such as the discovery of the high bottom pressure appropriate from the big to the steam line to supplement the amount of steam, pay attention to minimize the impact on the fractionation tower).
Blow steam: steam blowing before drying to the hot water tank, blowing on the waterline. After emptying (check air unblocked) open air cooling, if not timely phenomenon of blowing.
Small water supply: attention to steam with water, stop blowing steam, cold coke tower bottom temperature decreased after water has been feeding tower (note to prevent overpressure), then stop the isolation valve after the small steam blowing, prevent oil sticking down.
Large water supply: B point, the preparation of large water, pay attention to the bottom of the tower pressure, the pressure drop to the water, until the two sets of pump.
Change overflow: A point, the observation tower temperature, top pressure, calculation of cold water tank level drop and tower bottom pressure situation, change overflow.
Stop the pump water: observation tower body temperature is to meet the conditions, stop the pump ready to water. According to the rising speed of the liquid level of the hot water tank and the pressure drop of the bottom of the tower to control the water discharging speed.
Pour water: after settling for 1.5 hours after the open air cooling water cooling, water, with water velocity control after cold temperature is not greater than 40 degrees.
Coke tower is rotated, namely when a coke tower coalescence to a certain height, the raw material will switch to another coke tower through the four way valve. The coke tower of the coke tower is cooled by steam first, and then the coke is carried out.
2, hydraulic coke removal equipment
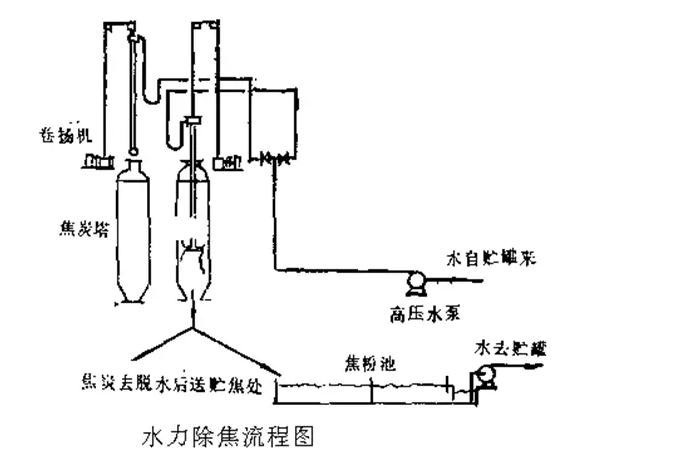
High pressure hydraulic coke removing method has been used in the present coke removing equipment. Hydraulic coke removal method, that is, the use of 11.8MPa high pressure water in addition to coke. The rest of the coke coke fell into the pool, at the same time with the bridge crane grab truck loading stored or sent elsewhere.
(1) the structure of the coke removing device
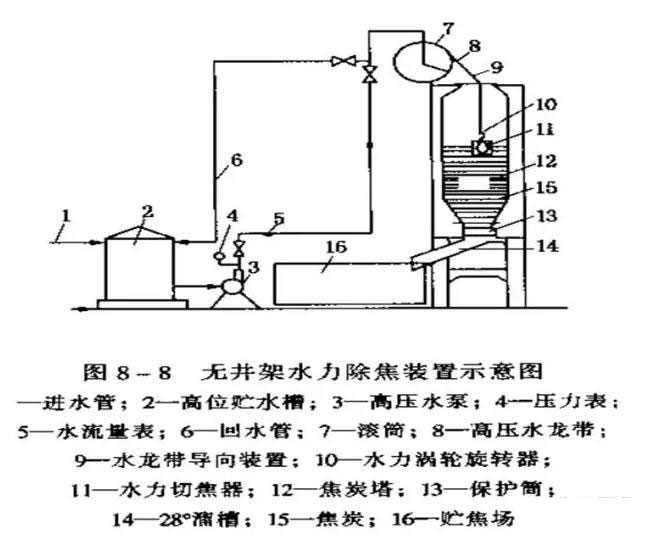
There are two forms of the hydraulic power removing device: the derrick and the derrick and the non - derrick.
(2) except Jiao Yuanli
High pressure water conveying by high pressure pump, nozzle, hydraulic hose through the drill pipe to the coke cutting device, high pressure water hydraulic coke cutter nozzle from the high-pressure jet, by the strong impact of high pressure jet of the petroleum coke cutting down, and make the water outflow from the bottom of the tower. The drill pipe constantly lift and rotate until the coke tower, in addition to the net so far all petroleum coke.
(3) the parameters of high pressure water
High pressure water pressure — — according to the introduction, the coke tower per meter diameter, need water pressure ~2.72MPa.
High pressure water flow — — under a given pressure and the flow is proportional to the impact force, according to the statistics of the United States Pacific company, high pressure water flow in the coke tower diameter 5~6.5m, about 170m3/h.
Larger diameter of the coke tower, the pressure of high pressure water flow increase is not obvious, when the diameter of 7~7.5m, for 180~190m3/h.
At present, the self-designed large diameter 8.4-9.6 meters, decoking water pressure is 28-31.5MPa, in addition to coke flow is about 280m3/h.
(4) safety precautions for delayed coking process
Coking unit due to the technical characteristics of its own, namely the production characteristics of continuous and intermittent, both chemical reaction under high temperature conditions, and toxic gases, operating conditions change, coupled with the characteristics of processing residue and coking easy to fire, so the accident probability larger.
Refer to the safety precautions in the operation process, we must first say that the device has a risk of which parts, and then can be targeted to put forward measures.
(5) dangerous part
1) raw oil buffer tank
Two kinds of residual oil can be stored in cold and heat. When the cold and hot oil are switched to each other or the raw oil is water, it is easy to cause the sudden boiling and the accident.
Four) the 2 way valve of the coke tower
Coking tower for the operation of the important equipment, if you can not switch, will result in a shutdown; in addition, four through the valve due to the friction and adhesion of coke and other effects, easy to leak fire.
3) high pressure water pump
Start high pressure water pump in addition to coke, as a result of water pressure up to 13-15MPa, flow 140 cubic meters, once the pipeline, flange leakage, high pressure water spray, easy to cause injury accident.
(6) note
1) raw oil buffer tank
Should pay attention to check the buffer tank into the oil before the water storage is put into the oil, the speed can not be too fast, into the oil tank after the liquid level should be controlled at 40-60%, and should strengthen the dehydration. When cold, hot oil exchange, should first tank residue liquid level control in the 20-30%, until the bottom of the water storage and dehydration, and then slowly into the tank. Often pay attention to the originalChange of material properties and oil outlet temperature, when the hot vent valve, steam tank top, this is the sign of suddenly boiling, immediately shut down or cut off the inlet valve to prevent tank at. When necessary, can open the roof of the valve after the valve, the valve will be placed in the memory of the air pipe to sweep the oil, so as not to block the pipeline.
Four) coke tower 2 way valve
Before switching the four - way valve, should pay attention to check the screw sleeve, its loose should be appropriate, the direction should be correct, whether the four - way valve has normal steam seal. If the four valve cannot be switched, cannot regain its original position, and the oil line pressure continues to rise, according to emergency venting. Four way valve should be equipped with carbon dioxide fire extinguishers or fire vapor, etc., and in good condition.
3) high pressure water pump
In the process of cleaning, if the high pressure water pipe line or the flange gasket rupture, high pressure water spray out, there is a threat to the safety of people and equipment, should immediately stop the high-pressure water pump.
4) other parts
Water injection heating furnace tubes, the key is whether the coking reaction and the furnace tube, according to the process card requirements, strict control. Coke Talaota for large blowing in the vent tower, emit large amounts of exhaust gas, which contains chloride and other toxic substances, endangering the health of workers, should be discharged to the gas pipe network. Coke tower in addition to the focus of the source of water for circulating water, it has been used for a long time, repeatedly, its sulfide, volatile phenols, cyanide and other toxic and harmful substances concentration will gradually increase, to deal with circulating water for regular drug purification. Supervision and inspection found that excessive concentrations of toxic substances in the water, in addition to the timely switch to fresh water, should be immediately cleaned.
Two, catalytic reforming process - reactor
The industrial reforming reactor according to the internal wall lining is divided into cold wall and hot wall reactor; according to the flow direction of oil and gas in the reactor is divided into axial and radial reactor reactor; according to the catalyst in the reactor is flowing into the fixed bed reactor and moving bed reactor. At present, the industrial reactor such as no special instructions for hot wall radial fixed bed or moving bed reactor.
1, fixed bed radial reactor and axial reactor
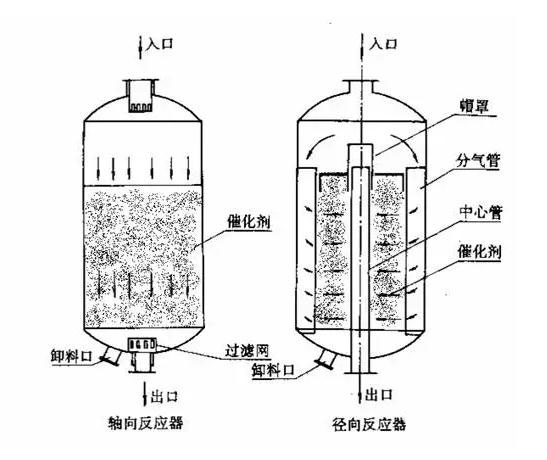
The main differences between the two structures are: the axial reactor catalyst bed is thick, the material is large in the bed layer pressure drop, and the radial reactor catalyst bed is thin.
2, overlapping reactor
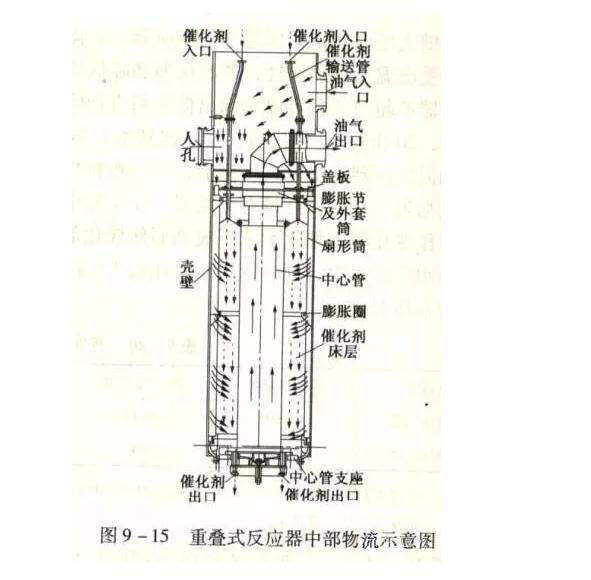
3, parallel reactor
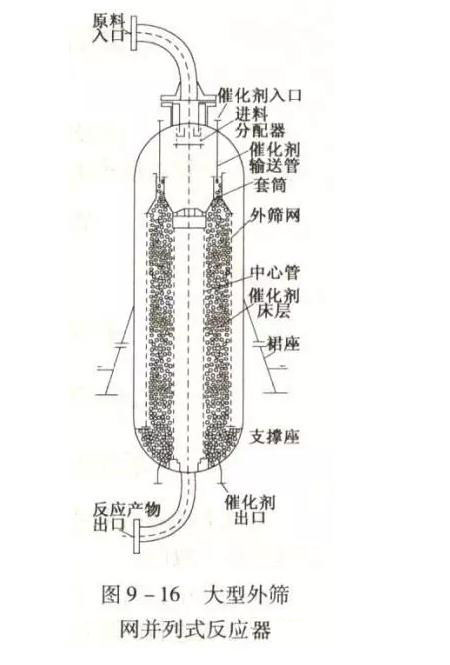
4, the reactor material attention
(1) due to the harsh reaction conditions, the reactor material selection and protection to meet the requirements of process conditions and to ensure the safety of the premise. In addition to the strength of steel to meet the conditions, but also consider the hydrogen corrosion and hydrogen sulfide corrosion phenomenon. There are hydrogen corrosion and hydrogen permeation, hydrogen bubbling, hydrogen embrittlement and metal removal in four ways, in order to prevent the corrosion of hydrogen used before the insulation to prevent, now commonly used methods that use double surfacing hot wall tube.
(2) the hydrocracking process of raw materials in general and sulfur, so the selection should also fully consider the harm, hydrogen sulfide corrosion of equipment. Therefore, generally used in the 21/4Cr-1Mo, he has a good hydrogen corrosion resistant performance and high creep strength.
Three, hydrogenation cracking process - hydrogenation cracking reactor
Hydrogenation reactor is the main equipment of hydrogenation unit. According to the process features, the hydrogenation reactor is mainly divided into two types, which are fixed bed reactor and fluidized bed reactor. Mainly consists of two parts, the cylinder and the inner parts.
1, reactor tube
The hydrogenation reactor can be divided into two kinds according to the structure characteristics of the reactor and the hot wall reactor:
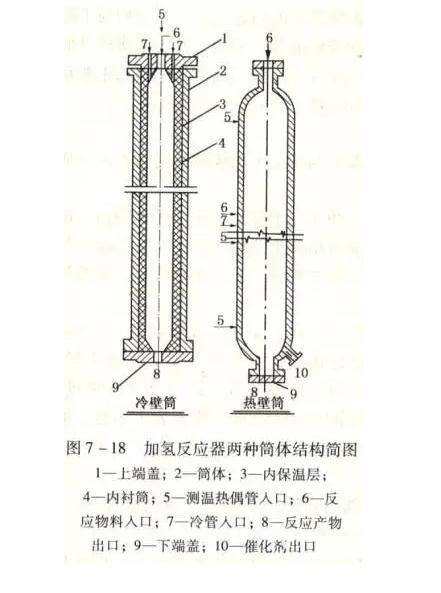
The wall hot wall reactor for direct contact with the media, the wall temperature and operating temperature are basically the same, so called hot wall reactor. Although the hot wall hydrogenation reactor manufacturing more difficult, one-time investment is higher, but because it can ensure long period safe operation, has been widely used in the international.
2, reactor components
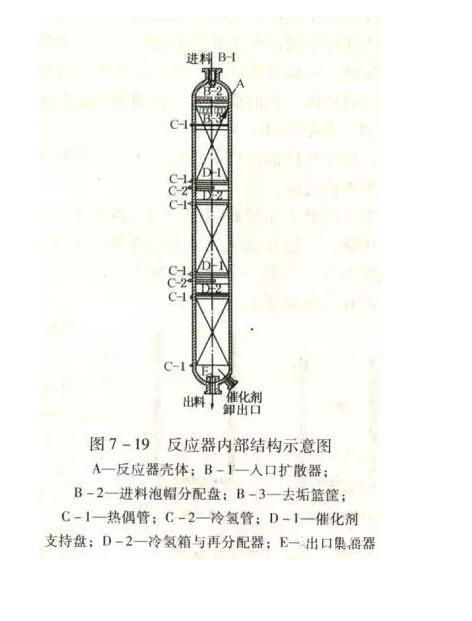
The diffuser entrance (1) (B-1)
The first part is the diffuser entrance into the reactor in the medium, it is placed in the top of the reactor and its role is: will enter the media spread to the whole cross section of the reactor; to prevent fluid shock directly through gas-liquid distribution plate; disturbance to the gas-liquid two-phase mixture, the pre allocation effect. Schematic diagram as follows:
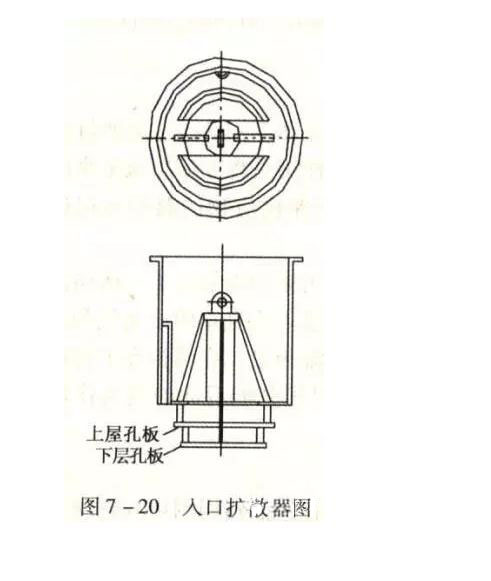
(2) distribution plate (B-2)
In the catalyst bed, the distribution plate is used for the homogeneous reaction medium, the flow condition is improved, the good contact with the catalyst is realized, and the radial and axial uniform distribution is achieved. The distribution plate consists of tower plate and the plate on the uniform distributor, distributor of various forms, as shown below:
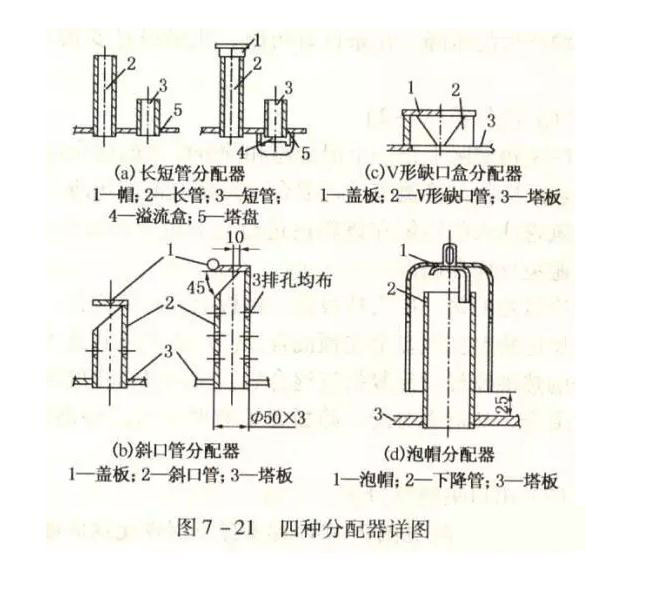
(3) Antisludge basket (B-3)
At the top of the hydrogenation reactor on the catalyst bed sometimes with detergent and basket, bed together on ceramic ball into reactor filter medium.
In order to make the whole bed surface to achieve a more uniform distribution, in order to filter into more solid impurities in materials, reduce the pressure drop of the bed, usually in the feed distribution plate of each of the three cap below the first reactor of hydrocracking process, the installation of a metal net woven basket, external uniform loading the size of large small porcelain ball. The basket is fixed on the distribution plate beam with chains.
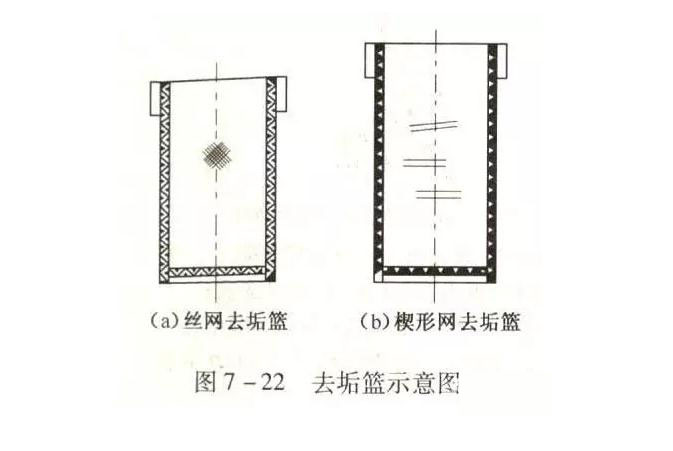
(4) introduction of tubes (C-1, C-2)
See diagram in the C-1, C-2 internal structure diagram of 7-19 reactor.
(5) catalyst support plate (D-1)
If the reactor has more than two catalyst bed, the upper catalyst needs to be supported. Is the two catalyst bed layer separated, sometimes also in the middle of the injection of cold hydrogen.
(6) cold hydrogen box (D-2)
Hydrogen cold box is actually a combination of mixing box and pre distribution plate body, the results as shown below. It is a place for mixing and heat exchange between heat and cold hydrogen in a hydrogenation reactor. It is the role of the material flow down the bed and cold hydrogen injection of cold hydrogen in the box to be fully mixed, absorb the reaction heat, control the reactantTemperature does not exceed the specified value, to avoid the reactor over temperature.
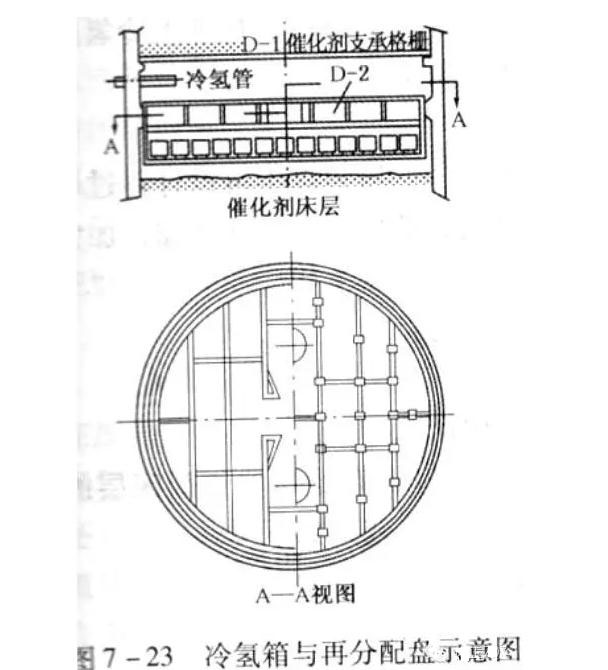
(7) export oil collection device (E)
The utility model can support the role of the catalyst bed layer of the lower layer, and the ceramic ball is filled around the oil collecting device. The structure diagram is as follows:

Four, the catalytic cracking process and riser regenerator
FCC reactor regenerator system equipment mainly regenerator, precipitator, riser reactor and their components and special machinery, special valves etc..
1, regenerator
The regenerator is one of the key equipment in catalytic cracking unit, its structure and operation conditions directly affect the carbon content of regenerated catalyst and catalyst loss.
The following were parallel device and conventional regenerator burning tank of high efficiency regenerator.
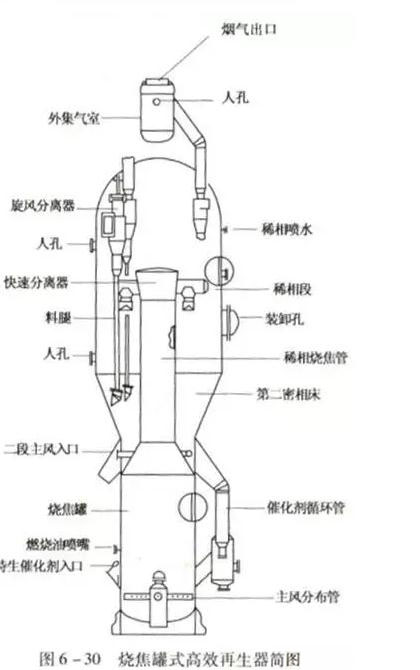
Coke drum regenerator characteristics: high velocity, high temperature, high oxygen content and low catalyst loading, in order to improve the burning efficiency of regenerator, the total coke burning intensity can reach 250-320kg/ (T.H).
From 1970s to early 90s, coke burning drum regenerator has been the mainstream design of our FCC technology, according to incomplete statistics, there are three main types as shown below:
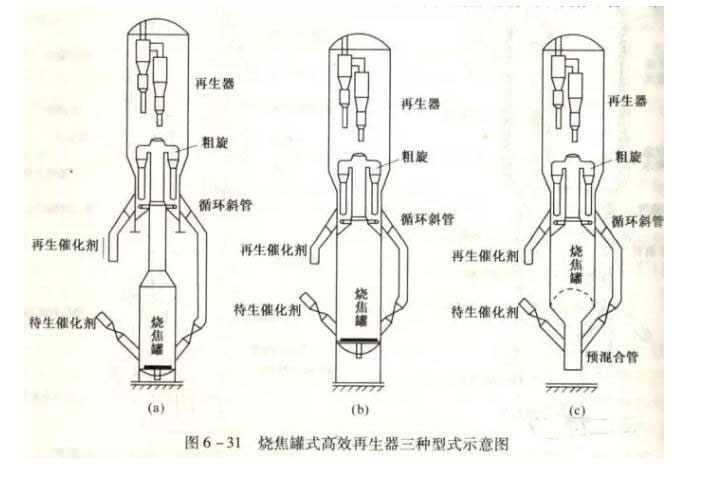
2, riser reactor and the settlement
The reaction system of the catalytic cracking unit is mainly included in the reactor and the two main equipment of the riser reactor. The diagram is as follows:

The bottom end of the lifting pipe is provided with a mixing zone, which is an important area of the mixing, vaporization and starting acceleration of the raw oil and the regenerated catalyst. In order to reduce the degree of warm mixing zone and give full play to the inherent activity of zeolite catalyst, it is necessary to ensure that the catalyst and oil are fully mixed in the initial contact point. As far as the oil and gas and catalyst are flowing through the vertical lifting pipe, the raw material can be evenly distributed to reduce the anti mixing.
Process equipment network finishing release, reproduced please indicate the source.