[PROBLEMS] the plate tower, plate tower in the field of research and development still exist for a long time, high resistance gas distribution gradient of liquid level uneven, liquid flow and mass transfer process in the presence of backmixing and dealing with the problem under the condition of long-term stable operation of equipment can not be easily foaming systems; the problems in the process of long-term research in the past basically no breakthrough, lead plate for tray efficiency and range can not be improved greatly in practical industrial applications, but also become the focus of the plate tower technology innovation.
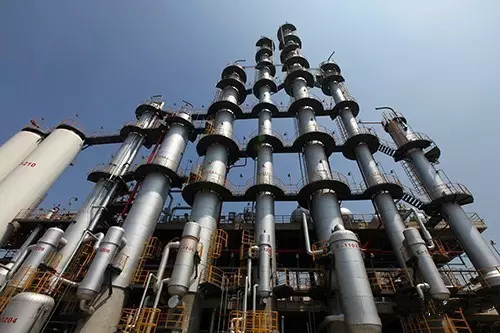
The plate tower, also known as liquid blocking with liquid or gas-liquid contact in the flooding, produce a lot of bubbles in the process, these bubbles are stable the gas-liquid mixture volume increased exponentially, the liquid flow is blocked seriously, lead to the tower plate and the downcomer liquid accumulation system, a substantial increase in column pressure drop and entrainment serious.
But do you know “ full countercurrent PFST tray &rdquo?
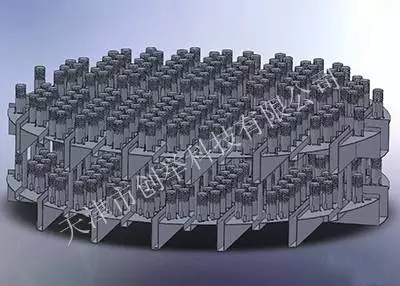
Figure 1 full countercurrent PFST tower plate
Full counterflow non backmixing jet tray, referred to as the full countercurrent PFST tray (Patent No.: 201210513678), with full countercurrent and liquid hold down global two new concept as the guiding ideology, according to theoretical calculation of chemical process simulation, from the experimental data to optimize the structure of the tray, according to different problems put forward the improvement of different structure.
There are some problems such as liquid level gradient and liquid phase mixing:
Improve the way - using the separate flow plate (i.e. guide groove structure);
Entrainment problem and resistance problem:
Improve the way - the use of three-dimensional jet full countercurrent mass transfer unit;
Easy foaming system:
Improve the way - using a plurality of long narrow strip of liquid drop volume, each drop tank bottom is provided with a plurality of downcomer.
A demonstration of the structure of full reflux and no mixing jet tray
The traditional trays are bubbling mass transfer tray, such as F1 float valve or its derivative. This kind of tray can not solve the problem of mass transfer and separation of large liquid, easy to foam and difficult separation system:
In the process of radial flow in the tower, there exists a concentration gradient, the mass transfer driving force decreases and the plate efficiency decreases;
The large liquid volume leads to the increase of the liquid level gradient on the plate and the uneven distribution of the gas;
Foaming system, bubble state transfer, no defoaming ability, extremely easy to cause flooding;
The existing plate circulation and drift, stagnation in the tower near the wall, forming &ldquo dead ” mass transfer;, plate efficiency decreased.
The upstream PFST tray is a large amount of liquid drop of liquid jet tray. The tray downcomer system using liquid drop drop liquid spray, gas phase mass transfer unit by injection, can solve the problems caused by the mass transfer efficiency decreased, foaming ratio and liquid gas.
1, multi drop liquid
1.1, the data in each point on the liquid phase is at an initial concentration (upper plate down of the liquid and gas phase), the contact is in a condition of high mass transfer. The longer the liquid flow on the tray, the greater the loss of mass transfer.
1.2, to reduce the gradient of the liquid surface, so that the uniform distribution of gas.
1.3, under the condition of large liquid to gas ratio, multi drop liquid can effectively control the thickness of liquid layer on the tray, so that the liquid layer can be controlled in a reasonable range.
2. High mass transfer efficiency
2.1, spray tower plate with gas-liquid contact surface, because the liquid phase is liquid droplet formation to enhance injection amount of droplet dispersion for gas-liquid contact provides a high surface area, which is compared with the bubble state mainly due to the high mass transfer efficiency.
2.2, the liquid phase is dispersed phase, the liquid is dispersed into droplets, so that the liquid phase of the molecular transport distance and the continuous phase of the bubble state compared to shorten greatly, thereby enhancing the transmission speed.
3, with defoaming effect
The jet tray has the function of self defoaming, and is especially suitable for easy foaming system. Gas carrying liquid and flow into the cap, and not like a floating valve tray in gas passing through the liquid layer on the tray, the liquid flow is basically not gas containing liquid, so the possibility of falling liquid pipe flooding is greatly reduced.
4, no return mixed
The guide groove will not contact the liquid on the tray (initial liquid liquid) and contact (end of liquid) are separated, the full realization of liquid phase mixing, vapor-liquid countercurrent contact to let. The plate can also be used to have no gradient of liquid level, concentration gradient and temperature gradient.
5, drag reduction
Spray tray gas does not pass through the plate on the liquid layer, only need to overcome is that part of the liquid gas pressure drop caused by gravity, so the smaller plate pressure drop under low load and low F1 type float valve, 20% ~ 30% F1 valve than the high load, and the load is larger and more pressure reduction.
6, processing capacity
Spray tray, due to the special structure of the gas cap, leaving cap horizontal or downward direction jet, which widened the gas-liquid separation space and time, the possibility of gas entrainment is greatly reduced, which makes the plate hole gas channel plate opening rate can be greatly improved, can reach 20% to 30%. While the opening rate can also allow the operation of the gas velocity ratio of the tower plate is generally higher than 1.5-2.0 times.
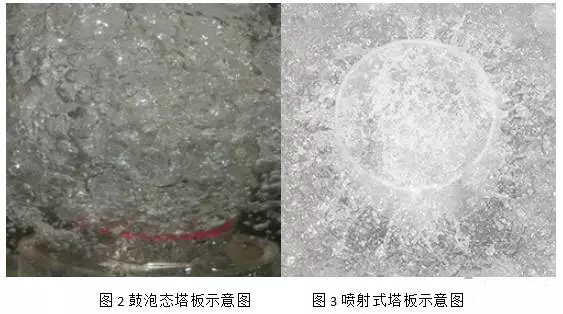
Figure 2 and figure 3 are for the moment of mass transfer and mass transfer form bubble state plate and ejector plate diagram and high speed camera photos, from the legend can be seen in the bubbling state of plate gas into the liquid layer plate is dispersed bubbles upward movement of liquid with bubbles do rolling up and down movement when the gas is dispersed phase liquid as the continuous phase, and the jet tray (such as full countercurrent PFST tray), gas through the orifice to the liquid will lift, crushing, to cover the top baffle side hole jet impingement, and then gas as the continuous phase and dispersed phase liquid.
The experimental results show that, compared with the traditional floating valve tray, the full countercurrent PFST tray has the advantages of high mass transfer efficiency, less entrainment and entrainment. It realizes the gas-liquid phase in the uniform concentration of tower plate of gas-liquid phase drift has a very good improvement; drop zone Suozhanta cross-sectional area is very small, can improve the utilization rate of the tower section, increase the handling capacity of at least 20% more than traditional valve trays; because the liquid on the tray in the flow pathShorter travel can be reduced to a corresponding level, reduce the surface gradient, avoiding backmixing of liquid phase in the plate, but also reduce the foaming liquid blocking and flooding problems be solved effectively; it has the characteristics of pressure drop and mass transfer separation equipment for small.
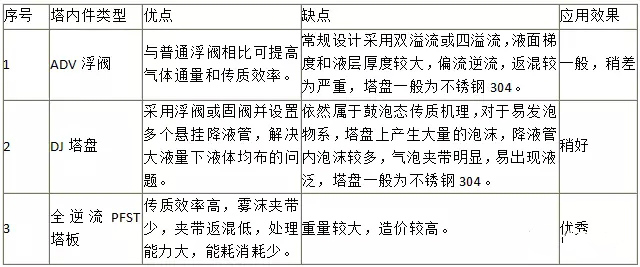
Comparison of advantages and disadvantages of several kinds of tray
Two, the technical innovation of the full counter current tray
1, theory and technology innovation
1.1. A new concept of separated flow is proposed for the first time. The liquid separated flow tray (initial liquid mass transfer and liquid separation), rely on the separated flow plate (i.e., a guide groove set on the tray) will not form a separate liquid phase, mass transfer and mass transfer to complete the two part. The tray without mixing, no retention, no bias; while maintaining each transfer unit are mass transfer in high force, high efficiency and uniform monomer to ensure the overall efficiency. These features can not be achieved by traditional trays.
1.2, put forward the concept of liquid holding bubble. Liquid descending plate tower tube design, especially for the foaming system separation, the main consideration from the downcomer flooding, to avoid flooding in industrial production in submerged tower.
The foaming systems design of reduced liquid pipe, we reduce the vapor backmixing from the point of view, the residence time and increase the volume flow rate of the liquid drop control tank to extend the liquid, so that more air bubbles from the liquid overflow broken, reduce the entrained liquid on the bubble, we decreased the gas mixing objective.
The board will not contact the liquid flow on the tray (initial liquid liquid) and contact (end of liquid) are separated, the full realization of liquid phase mixing, vapor-liquid countercurrent contact to let.
The plate can also be used to have no gradient of liquid level, concentration gradient and temperature gradient.
2, structural innovation
2.1, set up a number of long narrow strip drop tank, a plurality of long narrow strip of the tank are evenly distributed on the tray, each drop tank bottom is provided with a plurality of downcomer, liquid descending pipe is provided with a liquid guide hole, the downcomer through the downcomer opening into the tank to fall.
Drop tank, the tank design for narrow strip, Suozhanta smaller cross-sectional area, especially suitable for large amount of fluid condition, and under the same condition of the traditional multiple downcomer trays and shower trays, the level is low, low pressure drop, eliminating the bubble mass transfer mechanism;
A design of reduced liquid pipe, liquid shunt, anti clogging ability; by adjusting the drop tank depth, downcomer diameter and downcomer into the drop tank depth can freely adjust the plate thickness on the liquid layer, can adjust the liquid residence time, reduce foam, improve the gas-liquid separation efficiency;
The utility model is characterized in that the utility model is characterized in that the separation time of the gas liquid in the downcomer is increased, the operation elasticity of the downcomer is increased, and the entrainment of the mist is reduced.
2.2, a guide groove is set, will have mass transfer and mass transfer of liquid are not isolated, the gas-liquid mass transfer through liquid can be directly from the guide groove down liquid flow to the next stage, avoid and without gas-liquid contact liquid on the tray back mixing, the liquid group between concentration and gas component the concentration of the formation of maximum difference, thus greatly improve the driving force of mass transfer and tray efficiency.
2.3, the mass transfer unit uses the stereo jet transfer unit, its high efficiency of gas liquid mass transfer characteristic, pay attention to gas-liquid contact time and space, reduce the entrainment, the gas-liquid contact in the tray of the mass transfer zone become uniform, cross flow, jet mass transfer, through the shunt plate the liquid without contact on the tray (initial liquid liquid) and contact (end of liquid) are separated, the full realization of liquid phase mixing, vapor-liquid countercurrent contact to let.
The plate can also be used to have no gradient of liquid level, concentration gradient and temperature gradient. At the same time to eliminate the influence of drift, the viscous flow and the gradient of liquid level, the tray efficiency upgrade. Figure 4 is the schematic diagram of the three dimensional injection process of full countercurrent PFST tray:
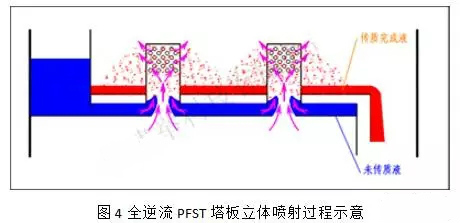
Three, the successful application of carbon in the field of extraction of four cases
1, C4 extraction distillation rectification
Isobutene by C4 butene isomerization unit, separation unit, MTBE synthesis unit and MTBE cracking unit. Among them, the processing capacity of C4 separation unit is 120 thousand tons / year (not containing ether carbon), and MEK and NFM are used as extractant. The characteristics of this system are that the liquid gas is relatively large, easy to foam and the separation is difficult. The core equipment for extractive distillation, extraction distillation, A B stripper, see figure 5.
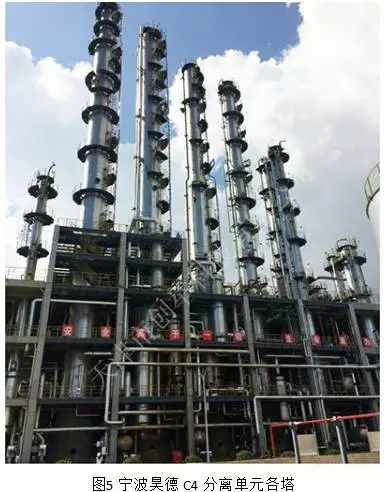
2, C4 extraction distillation and stripping, solvent regeneration tower
The main body of the device equipment including extraction distillation and stripping, solvent regeneration tower.
The device drive 65 hours postprocessing ability and product indicators that reach or exceed the design value: isobutane product concentration 98% (design value = 96%), olefin products concentration 66% (design value = 60%), and the unit runs smoothly. The stable operation of the extraction tower temperature is 118.8 degrees centigrade, the design temperature is about 132 degrees Celsius, the stripper stable when operating temperature is 165 degrees centigrade, the design temperature of 172.9 DEG C, the steam consumption of two tower was significantly lower than the design value, the energy-saving effect is remarkable. The technology reflects the production of fast, stable operation, less solvent consumption (only 60% of the design value), low energy consumption.
Four. Conclusion
In summary, the countercurrent PFST tray is applied in the transformation of C4 by extractive distillation tower, through production practice proved to be successful and effective:
1, full countercurrent PFST tray is very suitable for large diameter, liquid gas ratio, foaming difficult separation system has been successfully applied in the deep processing of extractive distillation on carbon four. The successful application of this technology provides a new engineering example for the design of large liquid to gas ratio and easy foam separation tower at home and abroad.
2, the upstream PFST plate technology, to achieve a qualitative breakthrough in improving the performance of plate tower, increase processing capacity, improve the operation index, reduce steam consumption, while reducing the extractant loss, and increase in investment, efficiency, energy saving and environmental protection is obvious.
3, wide prospects: full countercurrent PFST plate technology in the domestic chemical fertilizer, oil refining, petrochemical, coking, biochemical, pharmaceutical, chemical and other industries with similar conditions the project has good popularization value, is a new technology with less investment and quick results, with the economic and social comprehensive significant benefits.
Application of chemical industry in ChinaThe separation of the tower tens of thousands, the tower plate technology has broad applicability, with the improvement of technology and application, it will bring huge economic benefits and social benefits to the industry, is expected to reach 50% market share, will increase in energy saving brought tens of billions of dollars of social benefits. With the promotion of products, will be favored by domestic and international markets.
Process equipment network release, please indicate the source.

WeChat official