The world's first set of coke oven tail gas to ethylene glycol plant in Erdos City, Inner Mongolia to start construction. This is the world's first set of coke oven waste gas to produce ethylene glycol single device; domestic first set of 100,000 tons of high-temperature Fischer-Tropsch synthesis industrialization demonstration device in Shaanxi in the future energy start-up success, high-temperature Fischer-Tropsch synthesis technology development success, means that our country has mastered another powerful weapon!
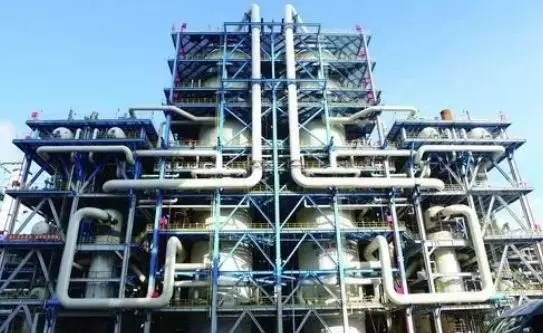
Coke oven tail gas is a combustible gas produced in the production of coke and tar products. Most coke oven tail gas of coking enterprises is discharged through combustion. Recently, the world's first coke oven tail gas ethylene glycol plant in Erdos City, Inner Mongolia Etok Banner started construction. After completion, coke oven exhaust can be turned into treasure.
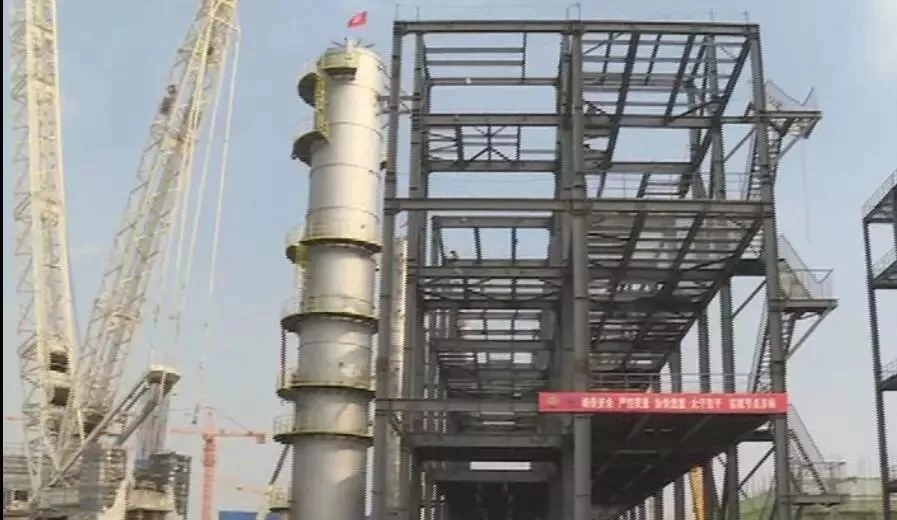
At the construction site of the second phase project of Jianchao Coking Co., Ltd. in Etok Banner, it can be seen that the workers are stepping up the installation of the main equipment of the project.
The 2.8-million-ton coking and 600,000-ton ethylene glycol project under construction is a key project for the industrial restructuring of Jiancheng Coal Coking Co., Ltd. in Etok Banner, with a total investment of 6 billion yuan. The project adopts the technology of syngas to produce ethylene glycol from Shanghai Pujing Chemical Technology Co., Ltd. The coke oven tail gas is used as raw material and stored and pressurized through a gas holder. The process of desulphurization, decarbonization and syngas separation produces 240 thousand tons of ethylene glycol per year.
The general manager of Etok Qijian Coal Coking Co., Ltd. introduced that the project is currently in the installation stage of equipment, and is expected to be completed in April next year. The project is to use coke oven gas to produce ethylene glycol. The production cost is 1000 yuan lower than that of petroleum route. After the project is completed, a new comprehensive utilization route of coke oven gas has been opened up, the added value of coke oven gas has been increased, the utilization of coke oven gas has been reduced to the maximum extent, and the utilization rate of carbon can reach 9%. More than 9%.
At present, the main installation of the project is being tightened up and is expected to be completed and put into operation in April 2019.
As early as June 2017, the first high-temperature Fischer-Tropsch synthetic process industrial test facility in China was launched in Yankuang Group Shaanxi Future Energy and Chemical Co., Ltd. 1 million tons / year coal indirect liquefaction demonstration project plant. Among them, Shanghai Yankuang energy technology R & D Co., Ltd. invested 100 thousand tons of industrial demonstration plant.
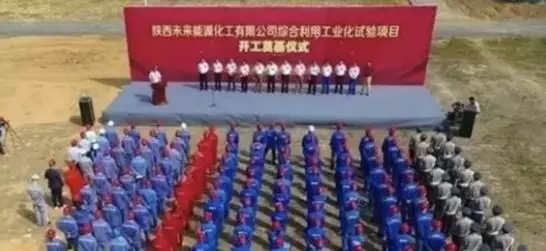
Shaanxi Future Energy and Chemical Co., Ltd. 1 million tons of low-temperature Feito synthetic kerosene project as & ldquo; 12th Five-Year Plan & rdquo; during the national coal deep processing demonstration project, on the basis of successful commissioning and maintaining a safe and stable long-term operation, the follow-up 4 million tons (2 million tons of low-temperature, 2 million tons of high-temperature) kerosene project has been listed in the country. Home & ldquo; 13th Five-Year Plan & rdquo; Coal Clean Utilization Development Planning, this industrial test device is designed for more reasonable and efficient construction of high-temperature coal oil projects and tailor-made.
In the whole process, the high-temperature Fischer-Tropsch synthesis is different from the low-temperature Fischer-Tropsch synthesis in process flow, catalyst, reaction conditions and so on. The carbon number distribution of the products is narrow and the olefin content is higher, especially - alpha; - olefin content is high. The petrochemical industry can be produced by advanced separation and deep processing technology. Fine chemicals and specialty chemicals that are difficult to obtain.
The unit was successfully commissioned on August 25, 2018, and on September 19, the unit was successfully commissioned. It operated continuously and steadily for 168 hours at full load. This is the first set of high temperature Fischer-Tropsch synthetic industrial demonstration plant in China, which is developed independently and has full intellectual property rights. Its completion and commissioning laid a technical foundation for the construction of China's million-ton industrialized plant, but also marked that the high-temperature Fischer-Tropsch synthesis technology fully qualified for industrialization. After learning the good news, academicians and experts who had been to Shaanxi Future Energy and Chemical Co., Ltd. to investigate the construction and commissioning of the project said: & ldquo; The success of the development of high-temperature Fischer-Tropsch synthesis technology means that our country has mastered another powerful weapon. ”
The operation data show that the reaction temperature of the demonstration unit is 300 ~370 C, and the CO conversion rate is over 99%, which is much better than the design value; the conversion rate of syngas is 92%; the hydrocarbon products are mainly olefins, the content is over 60%, and the carbon number distribution of liquid products is mainly below C20. The high-temperature Fischer-Tropsch synthesis technology used in the demonstration project was independently developed by a research team led by Dr. Sun Qiwen, General Manager of Shanghai Yankuang Energy Technology Research and Development Co., Ltd., Director of State Key Laboratory of Coal Liquefaction and Coal Chemical Industry and Chairman of Shaanxi Future Energy and Chemical Co., Ltd. The technology adopts iron-based catalyst and fixed fluidized bed reactor innovatively, which has low direct investment, high catalyst activity, low unit consumption and can be replaced on-line, good production stability, high on-line rate of plant and low operation and maintenance cost. The high temperature of Fischer-Tropsch synthesis can produce 4.0 MPa high grade steam by-product, which is beneficial to the comprehensive utilization of energy and the reduction of energy consumption per unit product.