On January 7, the reporter learned from the official micro-blog @Linzi release of the Propaganda Department of the Linzi District Committee of Zibo City of the Communist Party of China that at 7:36 a.m. on the 7th, the fire brigade of Linzi District received police from Xindian Street Ziboyuan Fengda Industry and Trade Co., Ltd. and a fire accident occurred in the chemical storage tank. It is understood that the accident location is the pyromellitic anhydride trap in the factory. The fire was put out at 8:40. One person was injured in the accident and is being treated in Linzi People's Hospital. The district government has set up an accident investigation team to carry out the investigation.
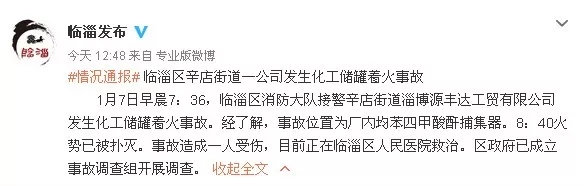
Basic Knowledge of Chemical Storage Tanks (Category and Maintenance)
Storage tank classification
1. Metal tanks: carbon steel tanks, stainless steel tanks, aluminum tanks, etc.
2. Non-metallic tanks: plastic tanks, ceramic tanks, FRP tanks, etc.
3. Metal-nonmetal composite tanks: steel-lined tetrafluoro tanks, steel-lined polyethylene tanks, steel-lined polyolefin tanks, steel-lined rubber tanks, etc.
Maintenance and Repair of Storage Tanks
In order to ensure safe production, safe operation of equipment and improve the service life and labor efficiency of equipment, regular inspection and maintenance of operating machinery and equipment must be carried out in order to prevent mechanical failure from affecting production or causing casualties due to mechanical accidents. Practical production, safety operation rules and safety maintenance management system have been studied and formulated for the annual tank maintenance and repair of this tank.
The maintenance cycle of storage tanks is generally as follows:
Medium repair 60-120 days, overhaul 12 months
Secondary Training: Eliminate Running, Running, Dripping and Leakage
Clean or replace the level gauge to repair or replace the inlet, outlet and sewage valves to clear the cooling water coil. Check and repair safety valve vent fire arrester. Repair the anticorrosive layer and insulation layer. Overhaul: including repairing tank internals in medium repair projects, repairing or replacing barrel joints for cracks and serious corrosion found. Polymer composites can be used for repairing. According to the requirements of internal and external inspection, and after repairing or replacing barrel joints, leak test or hydraulic test should be carried out. Fully remove embroidery and heat preservation. To deal with other problems found in internal and external inspection of storage tanks.
Maintenance methods and quality standards for tank repair, such as opening, repair welding, replacement of barrel joints, should be based on the "tolerance regulations" and other relevant standards, specifications for the formulation of specific construction plans and technical approval by the unit. Material used for repair (base metal, electrode, wire, flux, etc.) and valves should have quality certificates. Valves and fasteners made of old materials must be inspected before they can be used. The fasteners for assembling tanks should be coated with lubricating materials, and the bolts should be tightened diagonally. Non-metallic gaskets should not be reused in general. When choosing gaskets, the corrosiveness of media should be considered. After repairing, the anti-corrosion and heat preservation work can be carried out after passing the inspection.
Repair methods and quality standards for unqualified defects in used tanks:
1. Elimination of Defects by Grinding
2. Welding or patching
3. Replacement of barrel knuckle
4. digging and repairing
5. Fast plugging
This kind of problem can not be solved by traditional on-site repairing welding, and it is dangerous. Because of long construction period and high labor intensity, the replacement medium repairing welding will cause huge loss of shutdown. American Megawa technology can protect equipment quickly, simply and effectively by adopting corresponding technical products according to different equipment, different operation states and different corrosion leakage forms. Especially because of the comprehensive properties of polymer composites, such as chemical corrosion resistance and bonding performance, it avoids the adverse effects of traditional repair welding repair and makes the equipment life after repair. Even more than the new equipment, fundamentally solve the causes of corrosion leakage, help enterprises to improve equipment management level, reduce maintenance costs, improve the competitiveness of enterprises.
Cautions for Safety Maintenance and Maintenance
1. For tanks storing combustible gases and flammable liquids, they should be equipped with necessary fire-fighting equipment. Smoking, lighting and heating in tanks should be strictly prohibited, and their sources of ignition should be brought into tank areas.
2. For storage tanks that store inflammable, explosive, toxic and corrosive media, the relevant regulations on the management of dangerous goods shall be strictly enforced.
3. Before inspection and repair of storage tanks, the power supply of electrical equipment related to storage tanks must be cut off and the equipment handover formalities must be handed over.
4. When the internal medium of the tank is exhausted, the inlet and outlet valves should be closed or the pipes and equipment connected with them should be separated by blind plates, with obvious signs of separation.
5. For tanks filled with flammable, corrosive, toxic or asphyxiating media, they must be treated by replacement, neutralization, disinfection and cleaning, and then analyzed and tested after treatment. The results of analysis should meet the requirements of relevant norms and standards. Air replacement with flammable media is strictly prohibited.
6. In-tank operation, a permit for in-tank operation must be obtained. If the operation is interrupted for a long time, the in-tank work permit should be re-issued.
7. Sampling and analysis should be done 30 minutes before entering the tank. The oxygen content is between 18-23% (volume ratio).
8. When entering the tank to clean up toxic and corrosive residues, wear personal protective equipment.
9. Scaffolds and lifting devices that need to be built must be firm and reliable. Throwing materials and tools inside and outside must be strictly prohibited in order to ensure safe operation.
10. In tank lighting, no more than 24 explosion-proof lamps should be used.
11. When the tank needs to be set on fire, the fire certificate must be processed.
12. In tank operation, guardians must be set up and reliable liaison measures should be taken.
13. Upon completion, the inspectors and guardians jointly inspect the inside and outside of the tank. After confirmation, the guardian can seal the manholes only after signing the work certificate in the tank.
14. When discharging water after pressure test, the atmosphere must be connected to prevent vacuum pumping.
(Source: Luzhong Net-Luzhong Morning Post, Hebei Safety Production Micro-safety)