A fire in a chemical plant in Jiangsu
Injury to 2 people
Modern Express News: in the afternoon of July 30th, a new workshop in Jiangsu taet new Mstar Technology Ltd, Taixing Development Zone, Taizhou, has a fire, with fierce fire and heavy smoke on the spot.
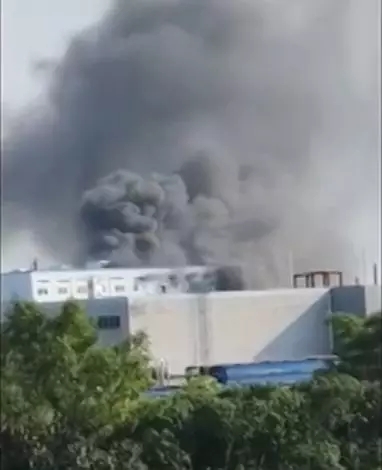
Heavy smoke in the field
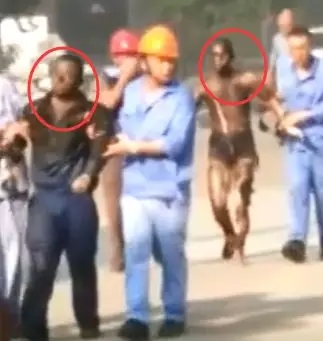
The injured person was supported by the workmate
Video from the people on the scene showed that the whole factory was filled with smoke, with factory workers helping two injured people running to the factory gate, two injured employees black and burned.
According to witnesses at the scene, around 4:30 p.m., he heard a muffled sound coming from the factory area, followed by thick smoke, many factory employees began to run out.
Soon, local firefighting arrived at the scene to fight the blaze.
Around 7 p.m., the Taixing Production Safety Supervision Bureau issued a briefing:
Notified documents:

Notification content:
Around 16:30 on July 30, 2018, a new three workshop in Jiangsu tathel new Mstar Technology Ltd had a fire accident in the process of cleaning equipment, causing 2 employees to be injured. After the accident, Taixing city immediately started emergency plans, city leaders, relevant departments and units quickly rushed to the scene to carry out emergency response. At present, two injured employees have been sent to hospital for treatment. The fire has been mended and the rice has suffered secondary disasters. The cause of the accident remains to be further investigated.
Since June, security accidents have occurred frequently. In this accident, the only thing to be thankful for was no one died. This also reminds us to be vigilant and strictly control the details of each step.
So, the problem comes!
What should we pay attention to in the plant cleaning process?
Cleaning equipment operation process
And safety precautions
1. Cleaning equipment operation process
Before starting the machine, the parts of the production equipment must be checked in section, and there are no sundries on the machine and equipment (such as clothing, gloves, tools, etc.) to ensure that the equipment can be operated in the rear.
Each control cabinet of the production line is divided into power supply, and the voltage condition of the total power supply must be checked before the power supply is supplied, and the power supply must be reached after the voltage is balanced. That is: Vab=Vbc=Vca=380V.
When starting and stopping production equipment, the green logo button on the control cabinet should be pressed in turn. After pressing a single start button, you need to stay for 5 seconds and then press the next start button.
Before the cleaning section is turned on, the two flume must be added to the overflow port to start.
The opening sequence of the cleaning section is: axial flow fan → net belt water removal → brush brush → brush pump → brush wash fruit → scraper lift → pump → dial rod motor → roller conveyor.
The order of the cleaning section stop is as follows: roller conveyor → dialing rod motor → pump → scraper lifting → brush washing fruit → brush pump → brush brush → net belt water → axial fan.
Two. Safety precautions
Before starting the machine, check whether there are foreign objects in the machine, such as stone, wooden stick, etc. if there is foreign matter, it needs to be cleaned before starting the machine.
Before starting the engine, check whether the tank is filled with water.
When starting, you must turn on various motors in turn and do not start at the same time.
During start-up production and start-up of various parts of the motor, attention should be paid to whether the equipment has abnormal sound, if there is abnormal sound, immediately report to the supervisor for shutdown inspection.
If the foreign matter enters the equipment during the production process, it must be shut down immediately. After removing the foreign matter, it can continue to produce.
When you stop, you must ensure that the raw material on the equipment is clean and then shut down in turn.
The electrical control cabinet must be regularly dusting, the dust removal cycle is 3-5 days each time. The electrical control cabinet doors must be locked in the production process. No water can be used to rinse the cabinet and the facilities in the cabinet.
In production, the equipment must be transferred from the special person to the operation. The operator must go through pre job training, and other personnel may not operate the equipment without authorization.
No person shall stand at the mechanical exposure place during the operation of the equipment, and shall not touch the hand into the machine when the equipment is running.
In case of power failure, it is necessary to report immediately to the officer in charge, who is resolved by a professional electrician and must not dispose of it without authorization.
Every day after work, we must clean and clean mud and other debris in the equipment, especially rolling parts, bearings and other moving parts.
-END-