[introduction] reactor is the comprehensive reaction vessel, the pressure generated in the reaction process of the sealing requirements. Mechanical sealing effect will directly affect the operation of the reactor, the serious will result in production, safety accidents and environmental pollution, such as immeasurable losses.

Sealing device for reaction kettle
The seal of the reaction vessel includes two major types: static seal and dynamic seal.
The reaction kettle, usually in the flange, flange and cylinder pipe flange, manhole, hand hole, thermometer, pressure gauge, take over the mirror over the other parts of the leak by static seal, because the sealing surface is relatively static. Static seal is relatively good solution, generally use various forms of static sealing gasket.
The gap between the stirring shaft and the kettle body leak, the stirring kettle body shaft and the stationary rotating (head) has a relative motion, to prevent leakage of the medium must be used for dynamic sealing device: mechanical seal and packing seal.
Packing: packing has the advantages of simple structure, convenient assembly and disassembly, but because there are some packing fatal weakness, causing it to short service life, high parameter conditions (high temperature, high pressure and high speed and high vacuum conditions) not applicable.
Mechanical seal: mechanical seal is widely used in the reactor, the reactor can according to the specific conditions, consideration of the structure design, special mechanical seal for reactor material selection, lubricating and cooling measures, in order to meet the requirements of process.
Compared with the soft packing seal, mechanical seal has the following characteristics:
Seal in the long cycle of operation in a very reliable seal, leakage rate is very small, the amount of leakage is generally only soft packing seal 1/100;
The service life of oil and water medium is generally up to 1 ~ 2 years or more, even in the medium of chemical industry, it can be more than half a year;
Mechanical seal friction power consumption is small, and the friction power is only 10% ~ 50% of soft packing seal.
Two, reaction kettle mechanical seal structure

The mechanical seal by the static ring and moving ring, an elastic element, a spring seat, a fastening screw, a rotating ring auxiliary seal ring and the static ring auxiliary seal ring and other components, anti rotation pin is fixed on the cover to prevent rotation of the stationary ring. The moving ring and the static ring can also be referred to as compensation ring or non compensation ring according to whether they have axial compensation capacity.
The moving ring and the shaft rotate together, and the moving ring and the static ring are closely jointed to form a sealing surface to prevent the medium from leaking. The ring on the seal chamber fluid pressure makes the surface pressure on the static ring end face, and generate the appropriate pressure and keep a very thin liquid film and achieve the purpose of sealing ring on the end in two.
The pressure element generates pressure, even if the reaction kettle is not working, the end face also keeps fit, so as to ensure that the sealing medium is not leaked, and the impurities are prevented from entering the sealing end face. The sealing element for sealing the gap between the ring and the shaft, the static ring and the gland of the gap, while the elastic element of vibration, the reactor impact cushioning effect.
Three, reaction kettle mechanical seal failure and treatment

Failure and treatment of mechanical seals
Causes and phenomena of failure
Reactor in the operation of the seal face often wear, thermal crack, deformation, damage, etc., screw, screw, spring will be used for a long time relaxation, fracture and corrosion. Auxiliary seal ring will also appear cracks, distortion and deformation, rupture, etc..
Fault handling method
1, mechanical seal parts if a failure occurs, will need to replace parts or improve the machining accuracy of parts, improve the machining precision and the reaction kettle mechanical seal itself and other components on the mechanical seal effect is very good.
2, in order to improve the sealing effect, the friction surface of the moving ring and static ring is smooth and the whole degree is higher. The width of the friction surface of the moving ring and the static ring is not large, generally between 2 and 7 mm.
Causes and treatment of vibration and heating failure of mechanical seals
Causes and phenomena of failure
1, the reactor operation process, by mechanical wear and chemical erosion, will make the dynamic and static ring fitting end surface roughness, and the gap between the ring and the sealing cavity is too small, due to the vibration caused by the collision vibration.
2, sometimes due to the sealing surface (corrosion resistance and) poor thermal performance, or the lack of cooling or end face in the installation of particulate impurities, will cause vibration and heat seal.
Fault handling method
1, if the moving ring, static ring and sealing cavity is too small, it is necessary to increase the sealing cavity diameter or reduce the rotation outside diameter, at least to ensure that the 0.75mm gap.
2, if the pair of friction pair is improper, it is to change the dynamic ring, static ring material, so that its temperature resistance, corrosion resistance. This will reduce the vibration of mechanical seals and heat.
Causes and treatment of mechanical seal leakage
Leakage cause of mechanical seal static pressure test
Mechanical seals do not pay attention at the time of installation, often will seal scratches, deformation, damage, cleaning up not only with granular impurities, or because the positioning screw loosening, capping machines and equipment is not pressed, the accuracy is not enough, so that the sealing surface is not fully fit, will cause the leakage of the medium. If the sleeve is leaking, the collar seal assembly has not been pressed or not enough compression or damage.
Mechanical seal periodic or intermittent leakage causes
Mechanical seal of the rotor components of periodic vibration, axial channeling larger, will cause leakage. The mechanical seal surface have certain pressure, so as to play a role in sealing, spring which requires mechanical seal to a certain amount of compression, a thrust to seal face reactor rotation so that the sealing surface sealing the required pressure.
In order to ensure that this pressure, mechanical seals can not have too much to the shaft of the channeling, generally to ensure that within 0.25mm. But in practical application, due to the unreasonable design, manufacturing error, assembly error and other reasons, often lead to a large amount of axial channeling, there is periodic or paroxysmal leakage.
Causes of frequent leakage of mechanical seals
There are many reasons for the frequent leakage of mechanical seals:
1, due to the sealing surface defects caused by regular leakage;
2, auxiliary sealing ring caused by the frequent leakage;
3, spring defect caused by leakage;
4, other also include the rotor vibration caused by leakage, transmission, tight and check parts of the quality is not good orThe leakage caused by loose, mechanical seal auxiliary mechanism caused by leakage, as a result of the problem caused by the media often leakage, etc..
Ways to reduce the leakage of mechanical seals
1, assembly must be clean and smooth. Mechanical seal parts, tools, lubricants, cleaning materials must be clean. Seal static ring wiping with softgauze.
2, truing chamfering rounding. Shaft sealing end cover of chamfer to trim smooth, rounded the shaft and the end cover to the sanding polishing.
3, the auxiliary seal ringassembly rubber auxiliary seal ring for gasoline, kerosene soaked not washing, so as to avoid premature aging swell deformation.
Staticring after the assembly with the hand presscompensation ring, check whether in place, whether the flexible elastic snap ring is reliable positioning. After the moving ring is installed, it must be ensured that it moves in the shaft.
Mechanical seal vibration partial big and processing method
Causes and phenomena of failure
Mechanical seals if the vibration is too large, will eventually lead to seal failure. But lead to excessive vibration causes of mechanical seal mechanical seal is not always their own reasons, other parts of the reactor is the vibration source, such as shaft design, machining precision and bearing, coupling the parallel degree of difference, radial force and other reasons.
Fault handling method
When installing shaft, sealing cavity, mechanical seal itself, it should be cleaned to prevent impurities from entering the sealing installation site. And reasonable design of the axial force of the balance device, so that the installation of mechanical seals installed in the axial direction of the rotor ≤ 0.3mm, the elimination of axial channeling.
Four, reaction kettle mechanical seal type selection method and principle
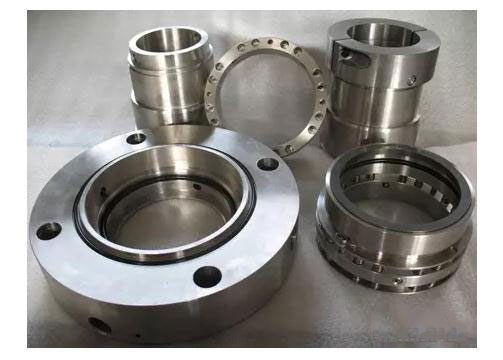
Mechanical seal according to the working conditions and the medium properties are different, high temperature resistance, low temperature mechanical seals, pressure resistant, corrosion resistant mechanical seal, light hydrocarbon medium particle medium mechanical seal and adapt easy vaporization of the mechanical seal, should choose different according to different use types and materials of mechanical seal.
Main parameters of type selection
1, sealed cavity pressure (MPA)
2, fluid temperature (c)
3, working speed (M / S)
4, the characteristics of fluid
5, the installation of sealing effective space, etc..
The basic principles of selection
1. According to the pressure of the sealed cavity, the sealing structure is determined by the balance type or the non balanced, single end face or double end face and so on.
2, according to the working speed, determine the use of rotary or static, hydrodynamic or non-contact type.
3, according to the temperature and fluid properties, to determine the friction pairs and auxiliary seal materials, and the correct choice of lubrication, washing, thermal insulation, cooling and other mechanical seal circulation protection system, etc..
4, according to the installation and sealing of the effective space, determine the use of multi spring or single spring or waveform spring, built-in or external.
In the design and selection of mechanical seal, it should be fully considered its application conditions, select the appropriate sealing structure and parts of materials, to prevent the design caused by improper seal failure.
Five, reaction kettle mechanical seal daily maintenance, maintenance
1, mechanical seal cooling liquid in each class to check again, with insufficient number of coolant to the oil pan height of about 2/3, the cooling liquid changed once a month, and do the record.
The 2 day, before starting to check the mechanical seal tight hoop screw loosening, static ring spring between the compaction degree and a clamping ring and the spring seat are distorted, jump phenomenon, if timely adjustment, and do the record.
Process equipment network finishing release, reproduced please indicate the source.