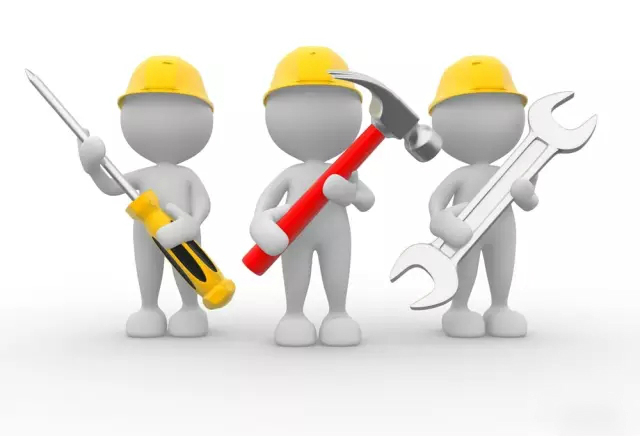
Shop operator safety regulations
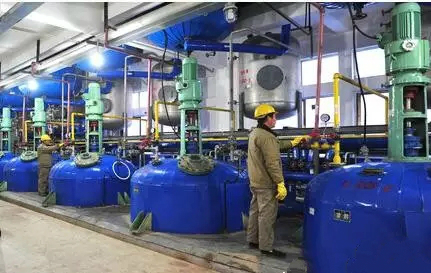
Reactor before driving:
1, check the kettle, blender, rotating parts, auxiliary equipment, indicating instruments, safety valves, piping and valves are in line with safety requirements.
2, check the water, electricity, gas meet the safety requirements.
Reactor driving:
1, before feeding the reactor should open the mixer, no noise and normal, the material will be added to the reactor, the number of feeding may not exceed the requirements of the process.
2, open the steam valve, first open the valve, open the intake valve. Open the steam valve should be slow, so that the jacket preheating, step by step, the pressure inside the jacket is not allowed to exceed the specified value.
3, steam valve and cooling valve can not start at the same time, steam pipeline gas is not allowed to hammer and collision.
4, open the cooling medium (water, 7 degrees of water, salt water, Leng Yichun) valve, the first open circuit valve, the valve into the road. Cooling medium pressure shall not be less than 0.1 MPa, and shall not be higher than 0.2 mpa.
5, water ring vacuum pump, to open the pump water, when the pump stops, the first stop after pump water, and should be excluded in water pump.
6, screw dry vacuum in strict accordance with the operating rules.
7, at any time to check the operation of the reactor, abnormal parking should be found.
8, cleaning the reactor, or the use of alkaline brush reaction kettle, be careful not to damage the enamel.
After reactor shutdown:
1, stop stirring, cut off the power supply, close all kinds of valves.
2, the reactor must be according to the requirements of the pressure vessel for periodic technical inspection, inspection is not qualified, shall not drive.
Reactor maintenance:
All reactor maintenance once every three months, maintenance check valves and pipes leak, stirring shaft is smooth, there is no abnormal noise reducer, bearing oil has not changed black or below the horizontal line, the kettle body and the pipe pressure gauge verification once every six months, the safety valve and a kettle. Once a year. Fill in the "reactor maintenance inspection record form".
Matters needing attention:
1, feeding must check whether the valve failure, the washer is loose steam leakage.
2, the feed should prevent entrainment of bulk metal or debris, for large pieces of hard materials, shall be crushed after accession, to reduce the temperature difference between the material and the tank wall, avoid cold or hot pot material feeding tank.
3, the use of steam heating, through the control of steam pressure rise rate of 0.1MPa per minute slowly heating; cooling, can be slowly into the cooling medium.
4, observe the reaction time and pressure index changes.
5, the mechanical seal cavity lubrication (sealing fluid) should be clean, not with solid particles, regular lubrication.
6, often check the reactor in good condition, such as when the material is found in the kettle body material, immediately notify the maintenance class repair or replacement reactor.
Safety rules for post operation of incinerator

First, the principle of proficiency
Although the incinerator system adopts the automatic control mode of operation of furnace safety procedures burned, but not the operation of the whole system of laissez faire, only rely on equipment automatic control is not safe, but the efficiency is very low.
In order to operate safely and efficiently, it is necessary for every operator to grasp the structure and principle of the whole system on the basis of the understanding of the performance of each equipment and the operating rules.
Second, the starting principle
1, the first stage should be starting air and garbage, shutdown stop is superior, the back Shun stop principle, if subordinates did not start, and start the superior may cause congestion, overload fault; during shutdown, if not stop will have similar fault.
2, before the start of the general, alarm, monitoring device should be started, so that they are in a state of monitoring, power supply must be continuously to the instrument. In order to record the status parameters of the whole working process.
Third, before the start of preparation
1, confirm the boiler working state is normal.
2, confirm the waste heat boiler is in normal state (for reference of waste heat boiler operation standard).
3, check the oil and hydraulic oil, check the grate is no exception, and then start the hydraulic device, further confirm the current and voltage and driving state.
4, confirm the status of the air baffle under the grate, and then turn it off.
5, send the garbage into the grate, and will be filled with garbage hopper.
6, the fan baffle all closed, when the fan to achieve the rated speed, adjust the furnace pressure is -50Pa--30Pa.
Note: prior to the start of the fan to confirm the flow of cooling water. Furnace pressure is -80Pa, the highest -20Pa. When to open the furnace gear plate, the furnace pressure drop to -80Pa.
7, to confirm the fuel system, fuel pump (a pump) is working properly, start the blower, open the steam supply valve and confirm the steam pressure.
Fourth, start
1, after the ignition of fuel injector, confirm the flame stability, open the main valve oil, a fuel ignition device, so that it is in a low load combustion (injection amount, low oil), according to the situation after the ignition, waste incineration, adjusting the oil valve, when the temperature reaches 750 DEG C, stop feeding. Stop oil, first of all should be slowly reduced oil supply, and then observe the furnace mild waste combustion, and then stop the oil.
2, according to the principle of reverse start all the ash conveyor, keep the ash machine water level is normal, confirm no blocking.
3, pay attention to the waste heat boiler pressure and temperature will not rise too fast.
4, when the incinerator temperature rises to 400 degrees, adjust the air baffle under the grate incinerator, in order to ensure the required air, gas should control the rate of temperature rise, rise too fast on the furnace wall and the smoke exhaust channel detector on the negative.
5, when up to 600-750 DEG C burning garbage is stable, depending on the situation, the one nozzle switch to waste oil, can also ignite two nozzle, and can be put into use, waste water sludge nozzle.
6, everything is normal, into the normal operation, the operator should often patrol, adjust the working state of the equipment.
Fifth, stop furnace
1, the feeding hopper in garbage all input furnace cover, feeding hopper cover, when the garbage is not continuous combustion, stop supplying air to the grate, to prevent the resurgence, when no flame, slow speed and reduce the furnace grate gear plate for air volume, at the same time, should pay attention to reduce as much as possibleIn order to prevent positive pressure in the furnace. It is important to stop before the fan, should closely monitor changes in temperature.
2, cooling water should be continuous supply. Until the waste heat affected the equipment to fully cool. After shutdown, check and repair the breakdown of the equipment to start the operation.
Sixth, emergency treatment
1, blower and fan due to failure to stop running, the furnace is burning, will lead to a wind baffle machine, fully open, and should reduce the intensity of combustion flame, prevent channeling into other places, and is ready to resume operation after the operation. Stop for a long time, should be extinguished the fire (such as the fire extinguished naturally, while paying attention to the water level of boiler grate, temperature and exhaust temperature).
2, ash removal system in a certain level of failure, should first of all the ash removal machine. Its steps in accordance with the stop, to restore normal reverse.
3, if the cooling water and boiler feed water stop, should cease fire immediately, except in a short time to restore supply.
Maintenance items:
Weekly maintenance items
1, fan bearing grease, dust removal impeller.
2, if there is a loose screw lock.
3, check the emergency discharge switch.
4, check and remove dirt. The cyclone combustion, and clean.
5, add rolling bearings, air compressor oil.
6, clean and filter, filter, filter Y filter element.
7, remove coke ash, atomizer.
Two, monthly maintenance
1, cleaning burner nozzle and ignition electrode rod.
2, the replacement of rolling bearings, air compressor oil.
Three, the quarterly maintenance items
1, replace the fan, air compressor belt.
Four, annual maintenance
1, replace the rolling bearing.
2, replace the fan bearing.
3, repair off refractory mud.
4, replace the burner nozzle, ignition electrode rod.
Safety operation rules for drying room
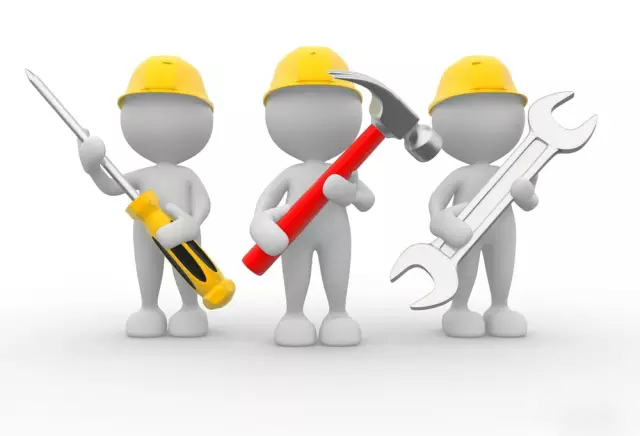
1, the use of drying in front of first check the drying room with no debris and dangerous goods, ventilator, instrumentation, piping, emptying valve, anti explosion door and other ancillary equipment is good, if a fault should be excluded.
2, where inflammable and explosive dangerous goods are not allowed to put into the drying room.
3, open the drying door should be ventilated before entering the drying room.
4, the product into the drying room should be carefully checked, the location should be appropriate, heavy pressure light, classified storage, to prevent the dumping of rolling.
5, close to confirm that no one inside the drying room, everything is normal can be closed, and then send the electricity or gas.
6, the vacuum drying room should be divided into several times the vacuum degree to the process requirements.
7, the electric drying room should check the electric wire and joints are connected firmly, the insulation is good, the room has no metal ride even. When opening the vacuum must be reduced to zero, safe operation. When you first start the fan transmission when the door opened, first disconnect the power supply off ventilator.
8, drying room steam control valve to regulate the safety of personnel, it is prohibited to toggle if there are problems in a timely manner.
(1) to have water cooling to open the cooling water, and check whether the flow of water;
(2) the first open water bypass valve and drain valve, open the steam valve and bypass valve will be closed by the return after a certain period of time;
(3) start fan, check into the exhaust valve is open.
9, inside and outside the room should be kept clean and dry, not to pile up the roof. The room is strictly prohibited from drying clothes and other sundries.
10, oven use must be in accordance with technical regulations, is strictly prohibited to use.
11, the workplace is strictly prohibited open fire and smoking. Near the drying room to install fire equipment, the operator should be familiar with the use of methods.
12, baking must have more than two people on duty, no two people at the same time off. In the semi dry material, should be timely to break bulk materials, rolling material. When the material is dry, it shall inform the personnel of the analysis room to take samples, and after the test is qualified, the material can be rolled.
The mechanic operation safety regulations
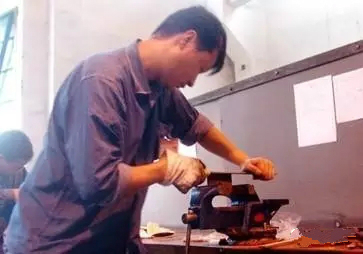
General
1, abide by the laws and regulations of hazardous chemical industry production safety, laws and regulations, company, factory rules and regulations, strict implementation of operating procedures, safety regulations. Familiar with the technical and equipment performance of the industry, not illegal operation.
In 2, under the leadership of maintenance manager, responsible for the full jurisdiction of all mechanical equipment in the area of responsibility for safe operation and maintenance, maintenance, repair, replacement, installation and adjustment, maintenance fitter, welders strictly comply with safety procedures, maintenance procedures and other maintenance management and security system; the personnel must ensure that the area of responsibility under the jurisdiction of the safe and reliable operation of all equipment within the scope of.
3, must be familiar with the jurisdiction area of responsibility process, there is a risk source category, risk source properties and the required security products, familiar with the working principle of responsibility area of mechanical equipment, improve the ability of self protection and the scene to deal with the problem.
4, the area of responsibility of personnel must be perfected within the jurisdiction of the information industry, information must be equal to the real, including: equipment assembly, blind plate pulling and blocking account, equipment maintenance records etc..
5, responsible for the technical transformation and other related work.
The maintenance fitter safety operation regulation
1, the work must be completed before the full range of protective clothing.
2, repair the machine must cut off the power supply, and so on after the machine stops rotating, can overhaul.
3, handling or remove the work greatly, using appropriate tools, together, not reckless.
4, equipment assembly will work on the stability, the hole shall not finger into the hole, and should pay attention to the belt gear, bite the hand, assembled, observe first hand turning, that there is no problem, and then the electric test.
5, the use of hammer or hammer, hammer should first check whether the firm, are not allowed to wear gloves, and observe around whether there are people or obstacles.
The workpiece 6, quenched, not directly on the hand, the pad copper or other soft things.
7, there must be a wooden scraper, the file can be used, but should be strong. File of iron not touch, is also prohibited by mouth, to prevent iron filings into the eye.
8, the use of wrenches, not too hard, so as not to slip wounding. All use of force wrench.
9, in the inspection and adjustment of the rotating parts of the equipment, we must cut off the power supply, and in the power of a warning sign or guard.
10, high altitude or multi-layer operation, must be fastened seat belt, Dai HaoanFull cap, or additional safety measures to prevent the use of tools or parts of the slide. Transfer tools and parts are not allowed to throw.
11, the use of oil cleaning parts when smoking.
12, fitter must be familiar with the grinding wheel and the hoisting safety operation procedures.
Maintenance welder operation safety regulations
1, the welding site prohibits the release of flammable and explosive materials, fire equipment should be equipped to ensure adequate lighting and good ventilation.
2, in the operation area of 10 meters, should not be stored in oil or other inflammable and explosive dangerous goods (including containers for flammable and explosive gas pipeline produced). If there is such a temporary site, and must be in this operation, the production department and the Department should be informed to the scene inspection, to take temporary safety measures before operation.
3, must wear good protective clothing before work. All employees must wear protective glasses or masks during operation. Should fasten the collar, cuffs tie up welding, wear a good helmet.
4, in the workplace hazardous oxygen and flammable, explosive volatile substances, gas environment, equipment, containers should be replaced by the prior, ventilation, and qualified by monitoring.
5, pressure vessels, sealed containers, broke the vessel, the welding of the pipeline, the pressure must be in advance, open, replace the removal of toxic and harmful substances after cleaning welding. Humid environment, the container should be taken within the corresponding electrical isolation or insulation measures, and into the custody.
6, in the welding, cutting hollow workpiece, must be left out of the pores. Welding in the container, the outside must be set up to monitor, and there are good ventilation measures, lighting voltage should be taken 12 volts. It is not allowed to be welded in a paint or plastic container.
7, electric welding machine to zero (ground) line and arc welding work are not allowed to take on flammable, explosive items, also not allowed in the pipeline and machine tools. The circuit should be well insulated, the chassis grounding must comply with safety requirements. Primary circuit shall be independent or isolated.
Screen protection device 8, electric welding machine must be perfect, electric welding and wire connection should not be exposed to. The two wire joint should be firm. 2 meters and above the height of the work, should comply with the safety rules of height work. Homework is not allowed to work around the loop line. High level operation should be set up monitoring.
9, comply with the relevant provisions of the "gas cylinder safety supervision regulations", seal and color markers such as not allowed to change the cylinders, prohibited the heat source temperature exceeding 40 DEG C to the gas heating, gas in the bottle may not be exhausted, it must keep a residual pressure, residual pressure of permanent gas cylinders should be not less than 0.05 MPa, liquefied gas cylinders should be left a filling quantity of residual gas is 0.5% ~ 1% provisions. Measures to prevent dumping when cylinders are placed vertically.
10, the work is completed, should check the welding work (including the relevant two circuit part) no abnormal condition, and then cut off the power supply, extinct fire.
Manual arc welder safety operation procedures

1, should master the general knowledge of electrical, comply with the general safety regulations for welders; also should be familiar with the fire fighting technology, electric shock and emergency breathing method.
2, work should be checked before welding power line, a lead wire and a wiring point is good, if the line across the roadway should add overhead or protective cover. Two line and shell welding machine must have a good grounding electrode holder of the insulation must be in good condition. Welding return line joints shall not exceed three.
3, rainy days are not allowed to expose the world welding, working in humid areas, should be placed in the shop where there is insulation and wear insulating shoes.
4, the mobile type welder from power network wiring or stitches, and grounding, replace the fuse etc., shall be borne by the electricians.
5, push the knife switch should deflect the body, to push a foot, and then open the electric welding machine; the machine, first turn off the electric welding machine, switch to pull off the power switch.
6, the position of the mobile welding machine, the first stop power, welding power failure, should immediately turn off the welder. Pay attention to the welding cable joint movement should be checked to ensure reliable.
7, in place when welding shall be installed in the arc column cover. We should remind people around not to look at the arc without cover bar.
Should wear gloves, 8 to change the welding rod, the body not to rely on iron or other conductive objects. Safety glasses should be worn when knocking scum.
9, welding non-ferrous metal devices, should strengthen the ventilation detoxification, if necessary, the use of filter mask.
10, repair the gas pipe or welding in a gas leak place, to inform the gas station and fire safety department, get permission to work. Must be closed source, strengthening ventilation work, saving gas to clean out. Repair of machinery and equipment, should be the protection of zero (ground) line temporarily open, after welding and then link.
11, after the start of the welder welding machine, hand and body should not contact the two circuit conductors, such as welding or welding torch, live parts of work table, the welder etc.. Operation in the container, damp, stenotic operation, body sweating summer or rainy days under dry wear clothes, when necessary to the laying of rubber insulation pad. In any case, the operator shall not be part of the welding circuit itself.
12, the work should be completed after the welding machine, and then disconnect the power supply.
Manual welding (cutting) work safety operation procedures
1, strictly abide by the general rules of safe operation and the welder of calcium carbide, acetylene generator, dissolved acetylene cylinders, safe use of water safety rules, rubber hose, oxygen bottle and welding (cutting) torch safety operation procedures.
2, acetylene station shall be operated by hand, comply with acetylene station safety operation rules.
3, work or acetylene station downtime for a long time to work, must check all equipment. Acetylene generator, oxidation bottles and rubber hose joints, valves and fasteners should be firmly secured, not allowed to loose, damaged and leak phenomenon. Oxygen bottle and its accessories, rubber hoses, tools can not grease the dirt.
4, inspection equipment, accessories and pipeline leakage, only with soap water test. During the test, no open flame, no smoking. Strictly prohibit the use of gas leakage test.
5, oxygen bottle, acetylene generator (or acetylene cylinder) and the distance between the fire should be 10 meters or more. If the conditions are not limited to less than 5 meters, and should take measures to isolate.
6, prohibit the use of easy to produce sparks to open the oxygen or acetylene gas valve.
7, gas cylinder equipment pipe freezing, strictDisable fire baking or use tools to knock the frozen block. With warm water of 40 DEG C to dissolve oxygen valve or pipe, acetylene generator, arrester and pipeline can be used hot water or steam heating thawing, or 23% ~ 30% sodium chloride water solution to thaw, insulation.
8, welding site should be equipped with the corresponding fire equipment. Outdoor work should prevent direct sunlight on the oxygen bottle or acetylene generator.
9, pressure vessel and pressure gauge, safety valve, should be regularly sent to the calibration and testing.
10, when the work is completed or leave the work site, to screw on the safety helmet, clean up the scene, the cylinder and acetylene generator in the designated place.
Process equipment network release, please indicate the source.

WeChat official