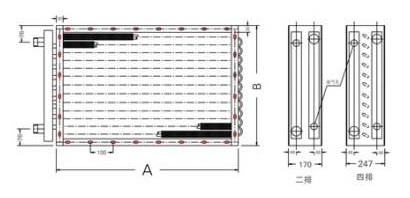
First section plate heat exchanger installation
Plate heat exchanger is determined by its structural characteristics, and its installation is more convenient and flexible. The following items should be noted in the assembly and installation of the plate heat exchanger.
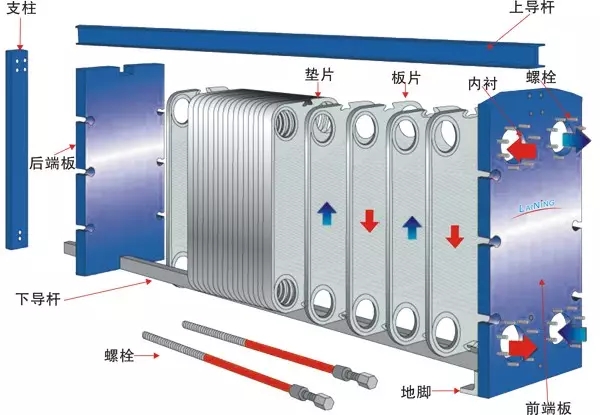
Part assembly of plate heat exchanger
A heat exchanger assembly, both manufacturing plant parts to the use of units shipped, on-site assembly, or use the unit open plate heat exchanger in equipment maintenance after assembly, must be carried out in the following order.
1. Read random documents (certificate, material certificate, flow chart, assembly drawing and packing list etc.).
2. Check whether the material of plate, nozzle and gasket meet the requirement of corrosion resistance of medium in heat exchanger.
3, according to drawings to check whether all parts are complete, model and size is consistent with the drawings.
4, the plate of the gasket slot clean, and evenly coated with adhesive, stick on the gasket, and then the plate neatly folded together, press a certain weight.
5, according to the design flow chart for assembly, and in accordance with the order of clamping. When tightening, tighten 1, 2, 3, and No. 4 nuts, then tighten 5, 6, 7, 8, 9, and No. 10 nuts.
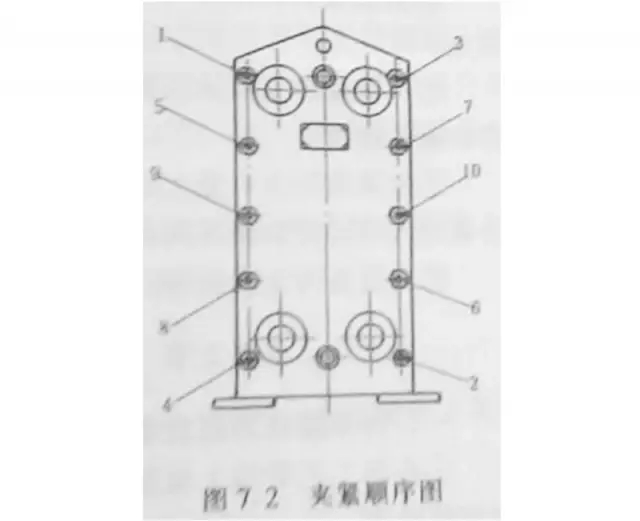
6 、 hydraulic test should be carried out on one side. The test pressure is 1.25 times the design pressure of the equipment. The pressure is 30min, check all the sealing box welding parts, no leakage is qualified.
Two, use the system installation of the unit
The installation of the system in use refers to the installation of the equipment from the manufacturer to the operating unit or the equipment repaired by the unit to the application station. This should be done in the following order.
1. Place the equipment on the foundation and anchor the anchor bolt.
2. Check whether the cold and hot medium inlet and outlet of pipe are in accordance with the equipment. Considering the convenience of overhaul, it is better to use the nipple when connecting the pipe to the heat exchanger.
3. The thermometer and the pressure gauge shall be installed in the inlet and outlet of the cold and heat medium of the heat exchanger.
Three, heat exchanger parts assembly and equipment installation notice
1, lifting equipment should pay attention to the center of gravity.
2, to pad groove bonding gasket, should ensure that the gasket and the plate gasket slot, no sand, oil, iron filings and solder and other debris, so as not to damage the seal, causing leakage.
3, when the bolt tightening force should be uniform, and continuously measuring two pressing plate inside the distance, to ensure the parallelism between the pressing plate two deviation is not more than 3mm. to the specified size and clamping to reach the corresponding parallelism, so as to avoid the partial pressure or slide gasket gasket groove. At the same time, the side clamping side canvass, observe whether there is a gasket, plate dislocation phenomenon.
4, hydraulic test of liquid generally use water. Water temperature should not be lower than 5 degrees Celsius. Test should be slowly raised. After the test is completed, loosen the compression nut properly, release the water, then tighten the nut and clamp to the original size.
5, the heat exchanger should be left around a certain space for repair, and its size and the size of the plate.
6, the bolt should be coated with butter, when conditions should be set on the protection tube, so as to avoid rust and bruised threads.
7 if the maximum pressure at the pump outlet is greater than the maximum equipment pressure, the pressure relief valve and the safety valve shall be installed at the entrance of the equipment.
8, when the equipment is full of liquid and with pressure, it is not allowed to clamp the nut.
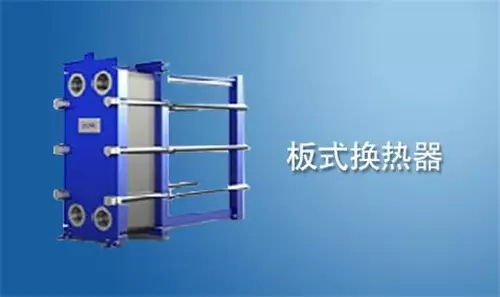
Second section plate heat exchanger operation
I. operation of the car and matters needing attention
1, in the new process pipeline use, we should pay attention to the elimination of impurities in the pipeline, so as not to plug the heat exchanger.
2, if the use of sewage as cooling medium, or to recover the waste heat of the sewage, or medium containing granular solids, it is necessary to install the filter at the entrance of the heat exchanger or decontamination device, so as not to plug the heat exchanger.
3, the cooling water (heating) temperature is more than 40 degrees, should be softened as soon as possible, so as not to heat exchanger fouling, affecting heat transfer effect,
4, check the pipe connections correctly, avoid two kinds of media mix, causing adverse consequences.
5. Check the inlet valve of the cold and hot medium before driving and turn off the outlet valve.
6, after completion of the above work, you can boot. Start the cold, hot medium pump, slowly open the inlet valve of the cold medium, and then open the inlet valve of the hot medium, so that the medium slowly into the heat exchanger, so as not to heat too high.
7, check all the sealing surface and all welds have leakage and other abnormal phenomenon.
8, slowly warming up, simultaneous determination and calculation to meet the requirements of the process. After satisfying, can enter the normal operation.
Two, normal operation and inspection
1, always check all the sealing surface and weld seam of heat exchanger, observe the abnormal phenomena such as leakage or not. If leakage is found, it should be marked on the leak in time and be processed after shutdown.
2, regularly check the pressure gauge, thermometer, observe whether there is abnormal phenomenon.
3, when parking, first slowly turn off the hot and cold medium inlet valve, and then turn off the two medium outlet valve. On the contrary, first open the outlet valve, then slowly open the inlet valve.
4, the media should be tested regularly on the low side, so as not to have high-pressure side media mixing. In case of leakage, stop processing should be stopped.
Three, stop operation and notice
1, stop before you stop the pump, cut off the power supply.
2, after stopping the pump, first slowly turn off the hot medium inlet valve, and then turn off the cold medium inlet valve. Finally, turn off the outlet valve for the two medium.
3, if the pipeline is equipped with vent valve, should open.
4, for high temperature medium and corrosive medium, should try to make the equipment empty, so as not to open the equipment when scalding, wounding and corrosion equipment.
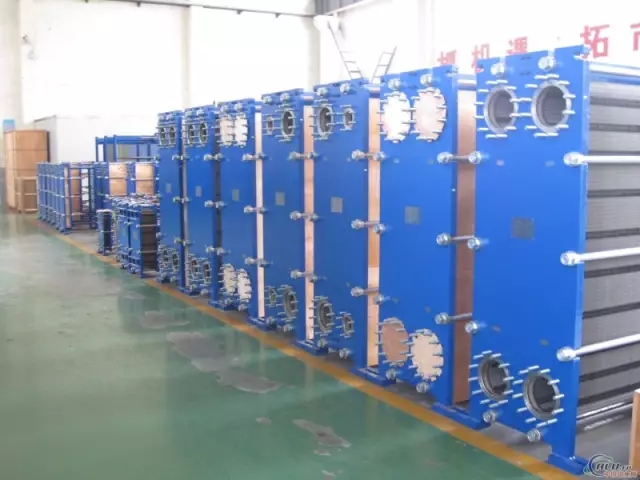
Four, common operation fault diagnosis and treatment
(1) operating conditions deviate from process requirements
The new heat exchanger production if not up to the requirement of process, should carefully check the original design parameters, design calculation, assembly is correct, and then decide whether to increase or reduce the heat transfer area and change process combination.
If the plate heat exchanger starts running, it is positiveNormally, after a period of operation, deviates from the process requirements, such as a rise or decrease in the pressure drop, or a rise or fall in the temperature at the outlet of the medium.
The solution to this problem is..:
1. Check whether the entrance parameters of hot and cold medium conform to the original design value. If not, try to adjust to the original design value. If the inlet parameter has been changed and cannot be adjusted to the original design value, the design calculation shall be re determined to determine the increase or decrease of the heat exchange area or the change of the flow combination.
2, if the inlet parameters of cold and hot medium are consistent with the original design value, and when the export parameter is not up to the design value, it should stop, disassemble the check board, stop or block the plate and so on, and deal with it in a timely manner.
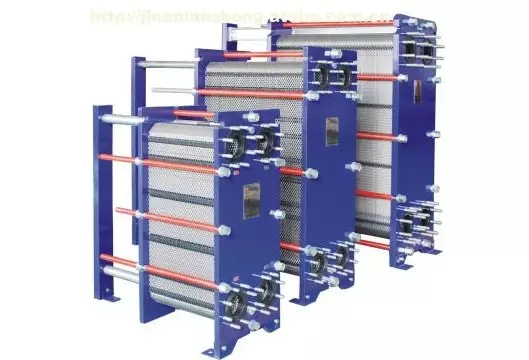
(two) leakage occurs in plate heat exchangers
As the plate heat exchanger has a longer sealing perimeter and a thinner plate, leakage may occur during use. Leakage can be divided into two kinds of internal leakage and external leakage
1, plate heat exchanger leakage
This is the leakage of fingerboard type heat equipment in the medium to outer space. This leakage is generally easy to spot. The main cause of this leakage is the aging of the gasket, corrosion or plate deformation. When this leakage occurs, it should mark the leaking part in time and open the equipment to replace the gasket or plate.
2 、 the inner leakage of plate heat exchanger
This refers to the two kinds of medium in the heat exchange equipment. For some reasons, the high pressure side medium leaks to the low pressure side. This leakage is generally difficult to detect in time. The main causes of the leakage are plate perforation, cracks and corrosion. The method of detecting leakage is to test the medium at low pressure side and judge from the change of its composition.
The leak check method is:
(1) disassemble the plate heat exchanger and remove the dirt on the surface of the plate. After drying, the heat exchanger is reassembled. A hydrostatic test with a pressure of 0.2~0.3Mpa on one side. After the other side of the water is removed, the test is stopped, the heat exchanger is switched on, and the side of the test piece is carefully observed, wherein the wet plate is a plate with holes or cracks.
(2) at the scene, we can also use light transmission and color inspection methods to detect waste plate. All scrap plates and gaskets to be checked shall be replaced and reassembled for use.
(three) the plate and plate of the plate heat exchanger is dislocated
The plate and plate dislocation phenomenon is easy to occur for the plate heat exchanger with large change of medium flow and pressure, and is a multi plate combined and long-term use. When the plate is dislocated, it sometimes leaks outside quickly. Although some leaks are not instantaneous, it is a hidden danger of leakage, so they must be dealt with in time.
The main reasons causing the dislocation are: the plate deformation of heat exchanger; the gasket of plate heat exchanger is slipping away from the gasket groove. In dealing with this dislocation, the deformed plates and the shims that slide off the gasket shall be replaced in good time.
(four) the simple treatment method of plate heat exchanger in the absence of maintenance equipment
Plate heat exchanger in use process, whether the plate deformation, cracks, perforation, or gasket aging and fracture, need to be replaced in time. If the field does not have enough spare parts, and heat exchange equipment and spare neither taifen, cannot stop, should be easy to processing the scene.
Methods simple processing is the plate damage and leakage of the plate pairs (A board +B board), if the number is not too much, to reduce the number of channels is not much, after assembly may continue to use, not great influence on production.
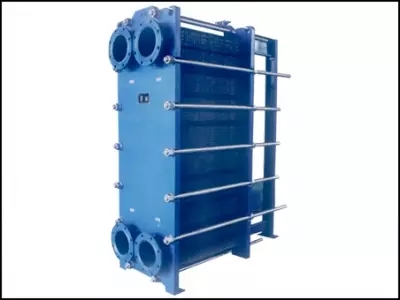
Third section plate heat exchanger maintenance
Plate heat exchangers should be repaired regularly, except for maintenance under special conditions. As plate heat exchanger is easy to assemble and disassemble, and maintenance is simple, it is not necessary to use special tools and equipment. According to the different situation in different ways can be used, if the device is not only the leakage, heat transfer system K decrease, can not open the heat exchanger, and the cleaning liquid to the equipment within the cycle number of hours in a closed system. There is no such condition on the spot, and after removing the equipment, it is found that the scale is not too serious. The water can not be removed and the water can be washed directly with a soft brush.
I. normal operation and maintenance
1, equipment needs to be repaired, should be installed in accordance with the reverse reverse heat exchanger.
2, the equipment used in the petroleum and chemical industry shall be regularly maintained according to the overhaul period.
3, if the medium in the equipment is flammable, explosive or corrosive medium, at least once a year should be repaired.
4, in other industries used in plate heat exchanger, if no leakage, preferably three years, en able to repair once.
Two. Cleaning and protection of plates and sheets
Keeping plate clean is one of the important conditions to maintain high heat transfer coefficient. In the plate and plate, the medium moves along the narrow and tortuous channel, and even if it produces a less thick fouling layer, it will cause the transformation of the flow channel, which will significantly affect the movement of the fluid, increase the pressure drop and decrease the heat transfer coefficient. For example, a sugar factory in the heating use plate heat exchanger, because the two water is not properly handled, the use of only two months in the process of blocking the entire flow channel, can not continue to run.
1. Chemical cleaning
The method is to transfer a chemical solution through the heat exchanger to dissolve and discharge the amount of dirt on the surface of the plate. The method does not need to disassemble the heat exchanger, simplifies the cleaning process and reduces the labor intensity of cleaning. The chemical cleaning is an ideal method because the sheet ripple can promote the turbulent flow of the cleaning liquid and is favorable to the dissolution of the fouling layer.
2 、 mechanical (logistics) cleaning method
The method is to disassemble the plate and brush it with artificial brush so as to achieve the purpose of cleaning the dirt on the surface of the sheet. This method is relatively direct, but it is difficult to clean the thicker and thicker dirt layer.
3, comprehensive cleaning method
For the case of hard and thick scale, it is difficult to clean simply by using the above method. Comprehensive method is to use chemical cleaning method to soften the fouling layer, and then use mechanical (physical) cleaning method to remove the dirt layer, so as to keep the surface clean.
4, cleaning matters needing attention
(1) chemical cleaning, the solution to maintain a certain flow rate, general 0.8-1.2m/s., the purpose is to increase the solutionTurbulence level.
(2) the chemical cleaning solution should be adopted for different kinds of fouling. In addition to the diluted sodium carbonate solution, 5% nitric acid solution can be used for the scale. In the process of producing soda ash, 5% hydrochloric acid solution can be used. But chemical cleaning agents that do not cause corrosion to the plate shall not be used.
(3) the stainless steel sheet is not allowed to be cleaned by the carbon steel brush when the machine (logistics) is cleaned, so as to avoid the corrosion of the plate. At the same time, the surface of the board can not be scratched or deformed.
(4) the cleaned sheets should be washed and dried with clean water, and the sheets shall be deformed when placed.
Three. Characteristics and replacement of gaskets
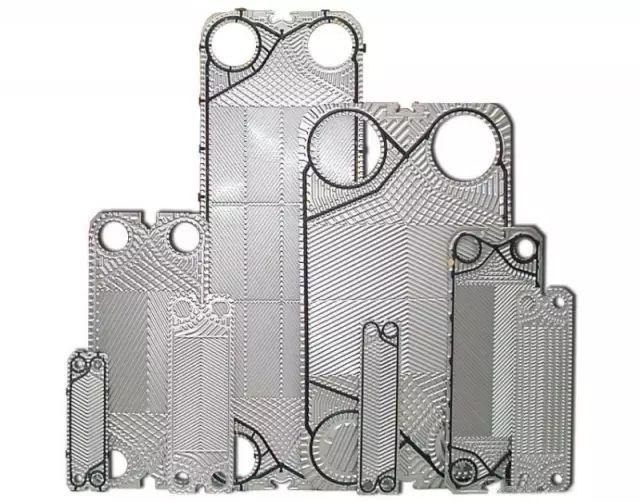
Because the application field of plate heat exchanger is expanding, different medium and process have different requirements of temperature resistance, pressure resistance and corrosion resistance. It is obviously impossible to fit all situations with a “ a universal ” a gasket with different materials should be used for different situations. The usual gasket is hexagonal in shape. The common types of gaskets are natural rubber, chloroprene rubber, NBR, three yuan ethylene propylene rubber, silicone rubber, fluorine rubber, asbestos fiber board, etc..
Plate heat exchanger gaskets in use, if leakage, fracture, aging and other phenomena, should be replaced in a timely manner. The replacement shall be done in the following order.
1, remove the waste gasket. Be careful not to make any scratches in the gasket slot when removing.
2. Remove the residual glue in the gasket trough with acetone, butanone or other ketone solvent.
3 clean the gasket, groove and gasket with clean cloth or cotton yarn.
4. Apply the adhesive evenly in the gasket groove.
5. Put clean new gaskets on the board.
6. The board of the shim should be placed in a flat, cool and ventilated place. It can be installed and used only after natural drying and fixing 4h.
This article source: network editing

Official public micro signal