[introduction] safety design of chemical construction project should follow the intrinsic safety design principle, the design process is the source of essential safety. The safety hazards in chemical process design should be thoroughly studied, and the systematic safety measures should be taken to eliminate or reduce the risk.
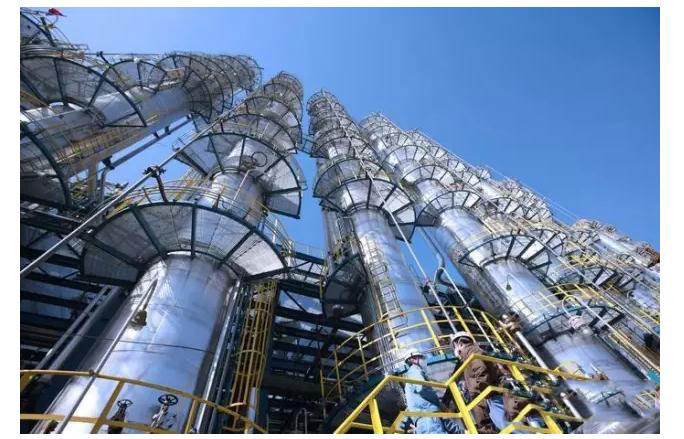
Process safety goal
The chemical production enterprises due to the use of flammable or toxic substances, these substances caused by fire, explosion or poisoning is very dangerous, in addition to many chemical production process also involves dangerous reaction and high temperature and high pressure in harsh operating conditions, these factors increase the fatal damage to the enterprise itself and the harm to the surrounding environment. How to solve these factors leading to disaster? It must be stressed that the principle is to control the source, into the process of intrinsic safety design to reduce the inherent hazard, not only consider the selection of protection against hazards in the environmental impact of new project; process design to minimize, not just by the waste treatment to achieve environmental friendly.
Process must be listed below three to achieve the goal of process safety:
1, in the design conditions can operate safely
2, even if some of the deviation from the design conditions can also be safely processed and returned to the original condition
3, to establish a safe start or stop method
In the regulation of chemical regulations, the risk of the goods is divided into five grades, designers according to the different risk level of chemical products, and then determine the fire spacing, explosion-proof grade, etc..
Chemical risk classification is mainly used in integrated production process, production and storage of raw materials, intermediate products and finished products, physical and chemical properties, and the number of fire explosion hazard and the production process to determine the nature of. It plays a decisive role in the selection of equipment and the operation mode of the instrument and the selection of fire fighting equipment. The instrument and the controller in the explosion danger zone select the corresponding explosion-proof structure or the positive pressure ventilation structure. In the occasion of distributing harmful gas or steam, the monitoring and warning facilities should be set up, and the instrument cable in the fire and explosion danger zone should adopt non combustible material type or flame retardant type. Instrument piping and wiring should be set in the centralized management of instrument instrument room, instrument tubing and wiring and electrical wiring should be laid separately.
Two. Risk identification and control of process design
In the process of production in the whole process of the project, the public auxiliary facilities of the production process, use and production material, main equipment and operation conditions were dissected and analyzed to find out the causes of dangerous and harmful factors of the style, type, location and production, thus put forward the feasible prevention, reduce or eliminate the risk of device to improve the operation, the countermeasures and suggestions of safety device.
Between the chemical production equipment process itself is unique, diversity, then how to ensure the safety of the device design, the following Liu Chengjun cited some control measures.
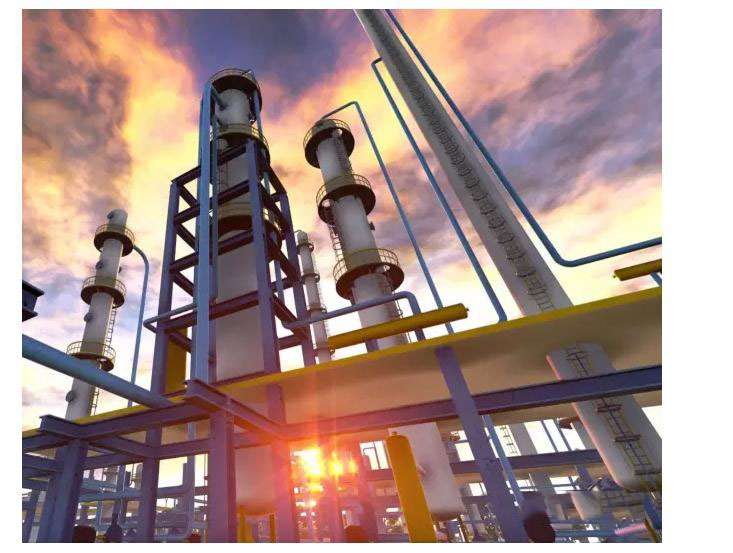
Three, process materials
In the process of production, the production of raw materials and other complex and diverse, the form of its existence is not necessarily, so the risk coefficient is relatively high. In the production of chemical raw materials and products are flammable and explosive, has the characteristics of high temperature and high pressure, may be due to changes in the environment so that the raw material remaining or mixed with air to form explosive gas mixture, once the fire is rapid fire, serious losses. Such as in the production of raw materials, semi-finished products, intermediate products and by-products and storage material, are respectively in solid, gas and liquid, due to the randomness of physical and chemical reactions, these substances in different state, temperature, environment will have the relative physical and chemical reaction and damage characteristics.
Therefore, to have a thorough understanding of the risk characteristics and memorize these substances is an important basis for risk identification, prevention and treatment. In the analysis of the effective identification of hazardous substances in the production process, is studied from the aspects of material, physical and chemical stability, and chemical reaction and combustion, explosion and toxicity characteristics, so as to achieve a minimum of danger.
Four, process route
Chemical production line is often complex process, the production of strong continuity, harsh operating conditions, if a link or equipment failure, that will destroy the normal production chain, resulting in accidents. Equipment maintenance which is in a normal state of continuous production, equipment and process parameters are changed, the process of maintenance after the existing status of the equipment and the process parameters returned to normal values, operational errors and fault rupture prone to this process, the medium leaking into the air or water, lead poisoning and suffocation of environmental pollution accidents. Usually there are a number of other processes in the process of reaction, and we need to pay attention to the use of which process can be a better way to reduce or remove the composition of hazardous substances. As much as possible the use of non-toxic and low risk materials in the process design, if there are special circumstances, try to ease the process conditions of severity, try to reduce the use of high risk and harmful material composition, safety is the first in the concept of strict production, make the best use of them, to reduce environmental pollution.
1, as far as possible the use of hazardous materials: to obtain a certain purpose products, their raw materials or auxiliary materials are not the only. When there is a condition, it should be a priority to use the material with no danger or risk.
2, try to ease the process conditions such as the use of severity: catalyst or better, by dilution using gas feed instead of liquid feed, to slow the reaction intensity.
3, avoid interference and security: by cutting out the superfluous nature of equipment to complete a variety of functions, the use of multiple devices, respectively, to complete a function, in order to increase the reliability of production. Improve the reliability of equipment, automatic control and electric, and the degree of intrinsic safety.
4, as far as possible to reduce the risk of reservoir storage: the greater the risk of reservoir, the greater the loss of the accident and the impact of the larger. Such as the use of membrane distillation instead of distillation, with continuous reaction instead of intermittent reaction, instead of disc drying tower, with flash drying by centrifugal extraction instead of extraction tower etc..
5, reduce the production of waste: process for raw materials, additives, solvents, catalyst carrier, etc. if necessary, whether it can reduce; whether Recyclable recycling; waste to comprehensive utilization, harmless treatment, reduce production waste, make the best use of it, to reduce environmental pollution.
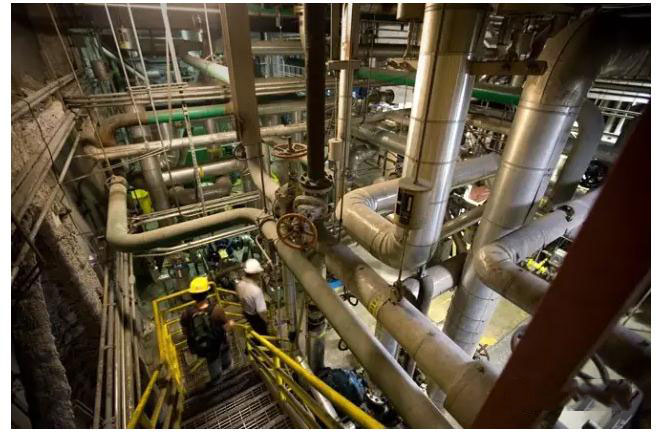
Five, chemical reactionStress device
Chemical reaction is the core of the whole production, generally through the reaction to get the desired product, while the reaction has also brought a lot of risk factors.
1, reactor type selection
According to the status of the reactor in and out of the material, it can be divided into two types of intermittent and continuous. According to the process of the material, it can be divided into two categories: one way and one cycle.
From the structure of the reactor to points, can be divided into the kettle type, tube type, tower type, fixed bed, fluidized bed reactor and other forms, they are suitable for different chemical reactions, according to reaction mechanism to select system.
The characteristics of the reaction device are determined by the process flow of the device characteristics and the composition of the device. There is a close relationship between the process characteristics and equipment characteristics, in the selection of equipment, safety problems of adaptability, carefully study the process, should be based on the relationship between the process of total operating area and the operating characteristics, through the analysis of the equipment to determine the type of equipment.
2, equipment material
Use of equipment materials should be taken into account, the process fluid velocity, temperature, pressure and fluid reaction characteristics and corrosion characteristics and other factors, choose to meet the corrosion resistance, meet the requirements of strength and processability (especially the weldability and mechanical processing of materials).
At the same time, it should be noted that impurities may also affect the temperature of the chemical reaction, which can lead to abnormal reaction rate, resulting in instability and danger. Some pollution will even play the same role as the catalyst, causing the reaction does not need, so some temperature measurement, the same material should also be exposed to the material should be carefully chosen.
3, reaction conditions control
The chemical reaction in the process of the myriads of changes of material, design a wide variety of materials, to achieve the control difficulty of the phase. For some simple operation, easy control of the reactor, the completion of the control work is also relatively simple. However, the design of the reactor control scheme becomes a difficult problem when the reaction rate is fast, the heat is large or the stability of the reactor is very small.
(1) how to avoid runaway reactions due to the lack of material response or decomposition speed and thermal effect data?
(2) once out of control reaction to reduce the speed of reaction, the reaction stops, or empty?
(3) how quickly the reactants are not involved in the reaction or process?
These are potential risk factors.
Due to the chemical reaction of the instability and unpredictability, the chemical reaction of some material is very stable under certain conditions, people to master the law is also quite familiar with; but if there is, the cooling effect of variation or excessive heating, stirring power failure, excessive reactant addition, reactants to the improper order outside the reactor, fire, heat transfer medium leakage into the container, may occur out of control. Therefore, in the design should ensure that all aspects of temperature control in a predetermined range, so as to avoid the reaction out of control, it is difficult to grasp.
In the process design, the method of reducing the feed rate, the heating rate of some materials, and the method of increasing the cooling capacity, such as the outer circulation cooler, or the multi section reaction are adopted to control the reaction. If cannot avoid, you should consider other protective measures, such as to the reactor into the low temperature medium, cooling the reactor; enter the volatile liquid to the reactor through the evaporation to absorb heat to the reactor; adding inhibitor to inhibit the reaction speed. When the equipment is filled with flammable materials, the use of positive pressure operation, to prevent the external air infiltration equipment, etc..

4, equipment structure
Stand in the chemical process design of equipment safety point of view, especially the high pressure vessel, its requirements are quite strict. From the appearance, not only requires the high pressure vessel itself has a strong structural strength, but also for the container seal storage requirements are more stringent, there must be absolute tightness. Only in this way can we do to prevent the container in the production of burst accident and easy to leak, volatile gas.
Due to some solid and liquid material, its state is not stable, and the air or some environmental exposure may cause significant leakage accidents, such as fire, explosion, poison, consequences be unbearable to contemplate. Therefore, the high pressure and easy sealing structure requirements need to be accurate. In the process of its safe operation, the temperature and pressure fluctuations should always remain tight and tight. If the container is super pressure for some reason, it is possible to be damaged due to excessive plastic deformation. In order to prevent this kind of abnormal situation, the safety pressure release device is generally installed on the container.
5, electrical
Electrical design, should be combined with the requirements of the process, according to whether the work environment is an explosion and fire hazardous environment, the risk level and the state of the dangerous material,
Take appropriate measures to prevent the explosion caused by improper design of electrical equipment and electrical wiring.
(1) in the selection of electrical equipment, should be based on the class and grade of the explosion hazardous places, the classification of explosive mixture, grouping, select the applicable electrical equipment.
(2) to consider the electrical equipment and lines, in particular, the normal operation of the electrical equipment will occur, the layout of the explosion dangerous places outside.
(3) should be installed in hazardous locations, should be arranged in a less hazardous location. The portable electric equipment should be used as little as possible in the explosion hazardous area.
(4) electrical piping wiring, switches, cables should be set tube is arranged in the place without danger, the layout should also be considered to make the power line protection layer of the corrosion damage.
(5) construction and equipment, should be reliable lightning protection and grounding measures; may produce electrostatic equipment, pipeline should prevent the accumulation of static electricity.
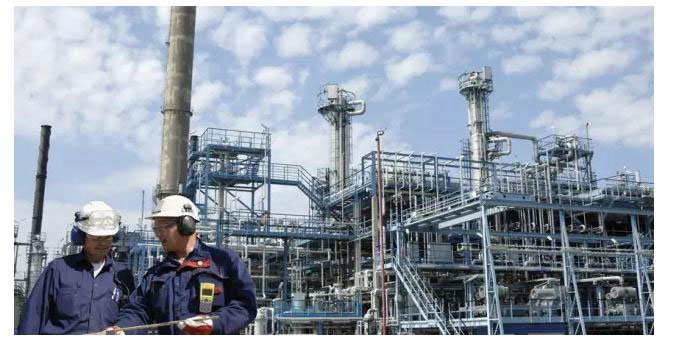
Process equipment network finishing release, reproduced please indicate the source.